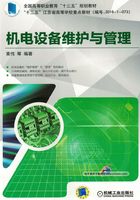
1.2 设备管理发展历史及国外典型维修管理方式
1.2.1 设备维修管理发展过程
1.事后维修阶段
19世纪初,工业生产应用了许多机器设备,如蒸汽机、皮带车床等,开始产生了设备维修问题。初始阶段,设备维修由操作人员兼任维修人员,修理成本低。随着工业生产的发展,设备维修逐步专业化,维修与生产人员分开,形成了专业独立的维修团队。这个过程的形成比较长,一直到20世纪初,设备维修技术才作为专业技术。
由于是简单、独立的单台设备,没有复杂的生产线,设备维修基本是事后维修,也就是不坏不修,坏了再修,停机时间长,干扰了生产的计划性。
2.预防维修和计划维修阶段
随着工业生产技术的发展,出现了生产线,为保证生产的连续,提出了以预防为主的维修方针,也就是预防维修。20世纪40年代,美国研究人员发现预防维修成本低,可以节约费用和时间,并能够保证合理安排连续生产,因此得到重视。1961年,瑞典建立了完整的预防维修管理系统,包括以检查、计划修理、验收、成本核算为主的整套工作制度和方法。
1923年,苏联改变了事后维修制度,提出设备定期修理办法,建立了一套计划预修的理论与制度,开始逐步在机械工业和化学工业企业推行。1967年,苏联在全国形成了统一的计划预修制度。
3.设备综合管理阶段
20世纪60年代后期,有些国家提出了对设备一生的综合管理概念,设备管理进入了新阶段。在使用过程中,设备的大型化、智能化,产生高效益、高效率,但也产生了严重后果,设备故障损失巨大,环境保护、职业安全卫生问题复杂,设备磨损加快,资金消耗大;设备技术密集,技术更新换代迅速,企业投入大,设备使用中减少停机时间,能够计划连续生产,尽快产生效益;现代化设备的社会化程度高,从调研论证、设计、制造、安装、调试、使用、维护维修直至报废,涉及的环节、专业很多,要求设备综合管理。
1.2.2 国内发展过程
1.初级阶段(1949~1958年)
新中国成立后,执行“一五”计划期间,在苏联援建下,重点工程相继建设,设备管理水平得到提高。1956年,设备管理引进了苏联的计划预修制度,适应当时我国的基本状况。经过实践运用,培养出大量的设备管理工程师和维修技术工人,建立健全了设备管理组织,为我国设备管理工作建立了基础。
2.曲折阶段(1958~1976年)
大跃进时期及文化大革命时期,设备和设备管理被破坏,设备质量下降,设备配套能力下降。三年调整时期,国民经济逐步提高,企业的设备管理工作在原基础上,有所创新。
主要创新有:设备管理的方针和原则是“以预防为主,防护与计划检修并重”“专业维修与群众管理结合”等;创立了“三级保养大修制”“三好四会”“润滑五定”“对事故三不放过”等制度;建立了专业维修工厂;开展行业专业性、地区性的设备管理活动,经常性举行设备管理研讨与交流,提高了设备管理经验。1963年,制定了实用性很强的《机修手册》。
3.振兴阶段
改革开放以后,设备管理工作发展迅速,开始学习国外先进的设备管理理论与方法,陆续引进了“设备综合工程学”“全员生产维修”“后勤学”等设备管理科学。1987年7月国务院发布了《设备管理条例》,明确规定设备管理的基本方针、政策、主要任务和要求。《设备管理条例》适应我国企业管理现代化的要求,将现代设备管理的理论和方法与我国具体实践相结合;针对我国设备管理的共性问题,作了原则性规定,具体管理办法则由行业、企业自行决定;改变了过去以修理为主的模式,确定了修理与改造、更新相结合的做法;企业开始重视设备的更新改造投入;初步建立了设备预防维修制度;设备管理要坚持“依靠技术进步”,贯彻“促进生产发展”的方针;确立了设计、制造与使用相结合的原则,维护与计划检修相结合的原则,修理、改造与更新相结合的原则,专业管理与群众管理相结合的原则,技术管理与经济管理相结合的原则。
1.2.3 传统设备管理的局限性
1.传统设备管理主要集中在设备维修阶段
设备维修固然重要,但维修的本质是事后的救护,设计制造过程中的问题,维修中无法解决。具体的维修过程还会产生过剩维修或维修不足问题。设备管理是设备的一生管理,而维修仅仅是上述过程的一个部分。
2.传统的设备管理信息交流不够
传统的设备管理中的设计制造和维修管理互相独立,信息交流少。设备在使用过程中出现的问题不能及时反馈给设计环节,在以后设备改进设计中得到改善。技术、质量、能耗、环保、职业安全卫生、成本等,也是设备管理因素。现在更加强调循环经济。
3.传统的设备管理没有与经济管理结合
传统的设备管理将设备的技术管理与经济管理分割开,偏重设备的技术管理,忽视设备运行中的经济管理。设备管理是企业管理的部分,设备管理不仅仅是为生产服务,还为生产经营服务。
4.传统的设备管理没有体现一生管理
传统的设备管理偏重技术管理,忽视经济管理。传统的设备管理仅仅是围绕具体的设备运行开展活动,现代的设备管理不仅管理设备的一生,还要涉及技术、安全、职业安全卫生、节约节能和节约资源等范畴。因此,设备管理的要求将越来越高。
传统的设备管理局限于维修部门,工作专业。现代的设备管理正在体现“全员性”,与设备相关的员工,均要参与企业的设备管理。
1.2.4 国外典型维修管理方式
1.英国设备综合工程学
设备综合工程学是新兴的设备管理学科。1971年由英国设备综合工程中心Dennis Parkes提出。1974年,英国工商部定义,为追求经济的寿命周期费用,对有形资产的有关工程技术、管理、财务及业务工作进行综合研究的学科。具体讲,就是关于设备、机器、装备、建筑物、构筑物的规划和设计可靠性和维修性。该定义包含了5个特点。
(1)以寿命周期费用量化评价设备管理
以寿命周期费用作为评价设备管理的重要经济指标,并追求寿命周期费用最经济。寿命周期费用是从调研、设计、制造、安装调试、使用、保养、维修、更新改造整个过程的全部费用,达到最经济。
(2)针对工程与管理的研究
综合工程学是对工程技术、工程经济学、工程管理的综合管理和研究。现代设备是机械、控制、液压等系统的高度集中,高精度、高效率,综合了多专业技术的成果。要管好、用好、修好这类设备,必须涉及工程技术的许多专业。
其次,设备管理还要工程经济学,符合经济规律,降低成本提高经济效益。设备添置时进行技术经济分析、正确决策,设备使用时合理的使用维护,设备更新改造时,进行正确的技术方案与经济可行性分析等。
(3)对设备可靠性和维修性设计的研究
在设备工程中,可靠性是指“无故障”,即设备在使用时无故障地执行规定的性能;维修性指“易修性”,即设备维修难易程度的特性。可靠性和维修性影响设备的利用率和维修费用。可靠性和维修性的极限是“无维修设计”,是综合工程学追求的理想目标。
(4)将设备管理的范围扩展到设备的一生
即对设备进行全过程管理,并系统改善每一个环节的机能。从设备的研究、设计、制造、安装,一直到运行维修的全过程。综合工程学运用系统工程的观点和方法进行研究与管理,将设备的整个寿命周期作为研究与管理对象,系统地改善各个环节的机能。
(5)注重信息沟通
综合工程学包含了设备工作循环的反馈管理,从设计、使用、成本信息反馈的管理。设备的添置包括自行设计制造与采购,大部分企业设备的添置,一般从专业厂家采购,使用企业应当与设备制造单位就设备的使用、性能、维护维修性等进行信息的沟通与反馈。无论哪种添置设备,综合工程学都强调了信息反馈管理。
在英国,设备综合工程学的推广,带来了经济效益,设备维修成本下降了50%。目前,设备综合工程学在欧洲、南亚等国家普及。
2.美国的后勤学
(1)后勤学概述
20世纪50年代,美国进入发展阶段,企业生产任务繁重,设备负荷大大增加,设备故障上升1/3。为保证高的生产效率,在生产线关键工段配备了相应的熟练维修技术工人。随着技术发展,生产线机械化、自动化水平不断提高,设备更加复杂,维修专业性要求逐步提高,维修成本及人员成本在不断提高。
设备故障造成停机损失、生产设备废品率上升,因此,在某些汽车厂的装配线,同时配两个维修队,以便迅速排除故障。这促使美国企业必须考虑如何完善设备维修维护的有效组织,促使美国提出设备预防维修。之后,美国还对设备预防维修存在的过剩维修和维修不足等问题,进行了改革,发展成为生产维修。
生产维修除了日常保养外,还有事后维修、预防维修、改善维修和维修预防。针对不同设备,采取相应的维修方式,如对重点设备,实行预防维修,一般设备实行事后维修。
20世纪60年代,美国航天工业和军事的庞大开支,促使进行设备寿命周期研究,1966年7月后勤学学会成立。后勤学确定了维修原则和维修方法。后勤学认为,一个系统应包括基本设备和相应的后勤支援,后勤支援主要有测试、辅助设备、备件、人员培训、器材储备运输、技术资料等,基本设备和后勤支援综合有效的配合,建立优化平衡,才能生成出经济效果好的产品。
(2)后勤学的基本内容
后勤学是系统或设备的规划、设计、试验和评价、制造和评价、用户使用和评价、退役更新等各个阶段加以研究和实施的后勤保障。各个阶段基本内容见表1-1。
表1-1 后勤学的基本内容
(3)后勤保障管理
后勤保障管理是设备所有功能和活动计划、组织、管理、协调及控制。主要包括后勤计划、后勤保障组织、后勤保障控制等,为使设备或系统达到目标任务,各阶段内部应有正确合理的后勤保障计划;设备设计制造中,各项后勤保障能力有机结合;保证主要设备运行和维修中,及时得到有效的后勤保障;不断评价设备全寿命周期总效果,并提出修改方案,即后勤保障分析。
3.日本的全员生产维修
(1)全员生产维修概述
全员生产维修简称TPM,日本工业迅速发展时期,在先后引进美国的预防维修和生产维修的基础上,吸取了英国了综合工程学的原理,结合日本实际,发展成为全员生产维修体制,取得了很好的效果。
20世纪50年代,日本以预防为中心的维修保养职能确立,主要的管理技术有预防维修、生产维修和改善维修。20世纪60年代,确立了设备设计中的可靠性、维修性和经济性的重要性,主要管理技术有维修预防、可靠性工程、维修性工程和工程经济。20世纪70年代,全员全系统生产维修综合效率时代,主要的管理技术有行为科学、系统工程、生态学和设备综合工程学。20世纪80年代以后,以状态为基础的全员生产维修时代,主要的管理技术有设备诊断专家系统、质量维修、FA时代的自主维修、提高设备综合效率。
(2)全员生产维修的要点
全员生产维修追求的目标是设备的“全”效率化、建立设备一生“全”系统、从管理人员到一线工人的“全”体人员参加,称“三全”。全效率是将设备综合维修效率提高到最高;全系统是建立起从设备调研、规划、设计制造或采购、安装调试、使用维护、维修与改造、技术更新直至报废的设备一生全过程的预防维修管理系统;全员是凡是涉及设备一生全过程的相关部门及人员,都要参加到全员生产维修的管理系统。即以提高设备的综合效率为目标;建立以设备一生为对象的生产维修系统,确保寿命周期内无公害、无污染、安全生产;涉及设备的规则、生产经营使用和维修等所有部门;从企业管理人员到第一线操作成员参加;加强生产维修的全程培训。
全员生产维修效果显著,据文献介绍,自全员生产维修推广以来,发展迅速,取得了明显经济效果。在日本,全员生产维修普及率大致达到65%,很多企业的设备维修费用降低约50%,设备开工率提高约50%,许多国家研究TPM管理制度,进行应用推广。
(3)全员生产维修发展现状
1)更加重视操作人员的自主维修。全员生产维修的目标是通过“改善人和设备的素质改善企业素质”来实现。工厂自动化主要体现在设备的自动化、柔性化等,必须培训适应工厂自动化时代要求的关键人员。
全员生产维修应当做到以下几个方面:操作人员要学会自主维修的本领;维修人员应当提高维修机械、电子电气、液压传动、控制等设备的本领,掌握专业维修理论及技术;设计、制造人员应使自动化设备不断接近“无维修设计”,提高设备的可靠性。
2)提高设备综合利用率。日本就设备现场管理提出了提高设备综合利用率的概念,即如何从时间和质量方面掌握设备的工作状态,增加创造价值的时间和提高产品的产量。主要手段有:从时间上增加设备的运行时间;从质量上增加单位时间内的产量,减少废品次品、增加合格产品的数量。
高设备综合利用率的理想目标,就是如何充分发挥和保持设备的固有能力,维持人与设备的最佳状态,达到使“设备故障为零、次品为零”的极限。影响设备综合效率提高的6个因素见表1-2。
表1-2 影响设备综合效率提高的因素
课堂练习
(1)请叙述我国设备管理发展的几个阶段及特点。
(2)请叙述国外典型的设备管理方式及特点。
(3)请叙述日本设备管理的特点,结合我国的实际,查阅资料或到企业调研,谈谈企业中设备管理的具体方式。