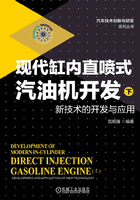
1.6 压入式喷涂铁-铝气缸套
为了在铝气缸体曲轴箱中使活塞环组与气缸套工作表面之间摩擦状况达到最佳状态的材料配对,大多数应用各种不同结构的气缸套,或者直接在铝气缸体曲轴箱中的气缸工作表面热喷涂内部涂层。当今气缸套不仅应用各种不同壁厚方案(镶铸或压入)的灰铸铁气缸套,而且也应用如1.5 节已介绍的镶铸复合气缸套,这种灰铸铁气缸套外部具有AlSi12涂层,以改善其与铝气缸套曲轴箱的结合牢度。
德国Federal-Mogul公司还利用热喷涂工艺开发了一种铁(Fe)-铝(Al)复合材料整体喷涂气缸套(图1-41),其中铁(Fe)内层类似于一层内部热涂层,提供了与普通灰铸铁气缸套相同的摩擦性能优点,而气缸套的外部铝涂层则能获得最佳的热传导性能,它几乎能达到了缸孔内壁涂层的水平,并与通常的滑动配合(Slip-fit)压入装配方法相结合,因此这种Sprayfit(商品名,意即“喷涂配合”,与滑动配合相对应)工艺提供了可靠性与创新的最佳结合,将热结合气缸套优点与内部涂层的功能和性能结合起来。
实际上,这种压入式Sprayfit气缸套在摩托车赛运动和道路摩托车使用中已经受的考验证实是可靠的,而在轿车缸内直喷式汽油机和柴油机上也已经在台架试验中证实了它具有良好的性能,并于2016年年底首次投入批量生产。
(1)Sprayfit气缸套的结构
新开发的Sprayfit气缸套采用机械或热工艺方法结合在发动机机体中,这种壁厚仅1mm的压入式气缸套适用于轻型结构的缸内直喷式汽油机。出于重量的原因,其中铁(Fe)的份额应优化到摩擦学所必需的最小值。这种Sprayfit气缸套由一层采用电弧金属丝喷涂工艺形成的0.4~0.6 mm厚的碳钢内层和一层采用相同工艺直接在该内层上喷涂的0.4~0.7 mm厚的铝(Al)喷涂层组成,在内径珩磨后包括剩下的0.1~0.3 mm厚铁(Fe)气缸衬套在内的最终壁厚为1 mm。Sprayfit气缸套可制成20~300 mm缸径的气缸套。图1-42示出了轻型结构发动机常用的气缸套工作表面断面金相组织的概貌,除了灰铸铁气缸套之外,还示出Nikasil(NiSi碳化物)涂层、热喷涂内部涂层[这里是PTWA(等离子金属丝电弧喷涂)涂层] 和最新的这种Sprayfit气缸套。

图1-41 在回转圆柱形工艺载体上热喷涂制造Sprayfit气缸套的工艺示意图
(2)Sprayfit气缸套的一般性能
因铁(Fe)的质量分数较小,Sprayfit气缸套在重量方面比镶铸气缸套具有明显的优势,例如对于一台4缸直喷式汽油机可减轻足足2 kg,甚至与重量优化的热结合灰铸铁气缸套相比,Sprayfit气缸套还可使每个气缸体曲轴箱的重量减轻0.5 kg。
除了减轻重量之外,Sprayfit工艺的第2 个优点是其薄的铁(Fe)涂层优化了从燃烧室至气缸体曲轴箱的热传导。在上面所述的铁(Fe)涂层厚度情况下,Sprayfit气缸套的导热能力接近于缸孔内壁直接热涂层的水平。图1-43示出了各种不同气缸套工艺在其他情况相同的情况下有限元(FEM)模型中的气缸壁面温度,在压入式气缸套上的热传导测量证实了这些数据。铁(Fe)涂层的厚度可以在热喷涂时灵活地进行调整,因此能够利用这种自由度精确地确定从燃烧室传导出来的热量,必要时甚至可限制散热。
由于现代缸内直喷式汽油机的爆发压力越来越高,而气缸之间鼻梁宽度却越来越小,整个发动机机体的热管理越来越成为研究的课题,因而在部分鼻梁宽度非常小的情况下,在气缸之间鼻梁中要钻冷却液孔,以避免鼻梁温度过高而降低强度。在这种情况下,气缸套的热膨胀性能是十分关键的。在压入式灰铸铁气缸套的情况下,着火运行状态时铝机体的膨胀要比气缸套大得多。为了在热状态下气缸套与机体之间具有足够紧的配合,那么在室温下两者之间必须选择足够大的过盈量,这样在冷态时会导致较大的机械负荷。表1-2 表明具有较小过盈量的Sprayfit气缸套在温度变化的过程中仍能保持不变的配合,而且冷态时气缸之间鼻梁的负荷也要比灰铸铁气缸套小。

图1-42 各种气缸套工作表面断面的金相组织

图1-43 各种气缸套工作表面温度的比较
表1-2 各种运行状态下使用压入式气缸套的气缸鼻梁负荷

就摩擦学而言,Sprayfit气缸套与缸孔内壁铁(Fe)涂层一样优于镶铸式灰铸铁气缸套,有关这方面的文献资料表明,在一定条件下其摩擦和磨损的数值有所改善。当然,对于燃烧室内的运动件的最佳配合间隙而言,重要的是始终要考虑到所有的部件,而所选择的珩磨工艺、活塞环涂层、活塞环设计和活塞设计对此具有重大的影响。
在腐蚀方面,这种Sprayfit气缸套与灰铸铁气缸套或直接在铁(Fe)基上的缸孔内壁涂层并无明显的差异。根据要求也可以用热喷涂工艺制成高耐腐蚀的FeCr涂层(Cr质量分数>13%)。
(3)使用状况
在摩托车赛的使用中,Sprayfit气缸套早已显示出比迄今为止摩托车上通常使用的典型NiSi碳化物(NiSi-Karbid=Nikasil)涂层,具有长得多的耐久性(使用寿命超过10次比赛)。把这两种目前所应用的涂层类型在比赛运行(0.5 L单缸风冷发动机,52kW和8500r/min)中进行比较,经过不多几次比赛就显示出明显的差异(图1-44),NiSi碳化物涂层已呈现出明显的磨损,即在垂直方向上拉出了沟槽;硬的SiC颗粒(深灰色)并没有承受住活塞环的机械负荷,而是被压在较软的Ni点阵中;珩磨组织也被完全毁坏。而Sprayfit气缸套均匀的硬的铁(Fe)基工作表面经过可对比的比赛运行持续时间后并无磨损,珩磨组织也仍然存在。

图1-44 在摩托车赛中使用后气缸工作表面状况的比较(左:Sprayfit,右:Nikasil)
即使在普通使用的摩托车上,与直接在缸孔内壁上的涂层相比,Sprayfit气缸套也具有优势,必要时可很方便地更换,成本也较低,而且无须重新进行缸孔内壁涂层。
Sprayfit技术成功地在摩托车上使用后,也推广应用于轿车发动机,并在发动机试验台架上与传统技术进行了对比试验。Sprayfit气缸套曾在一台升功率超过63 kW/L和爆发压力大于180 bar的现代直喷式柴油机上进行过试验,发动机在4000r/min全负荷下运行。这种批产机型原装备压入式灰铸铁气缸套,在上述试验条件下批产机型的机油耗为9~11g/h,而装用Sprayfit气缸套的发动机对比试验结果其机油耗为6~9g/h,处于较低的水平。发动机所有其他性能数据表明两种气缸套并无差异。Sprayfit气缸套与气缸工作表面直接涂层的另一种对比试验证实,前者在机油的铁(Fe)残留物中份额要少得多,这表明Sprayfit气缸套具有特别高的涂层品质。
此外,还进一步在缸内直喷式汽油机上进行了试验。Sprayfit气缸套在一台1.8 L排量和175 kW功率的缸内直喷式汽油机上的试验也证实并未出现任何异常情况。
(4)与气缸内壁直接喷涂的比较
在轿车发动机铝气缸套工作表面内部直接喷涂的情况下,同样采用了热喷涂的方法,但是因边界条件的不同,气缸内壁直接喷涂是一种较复杂和较昂贵的制造工艺:
1)铝气缸体曲轴箱必须铸造得无微孔,这对铸造工艺提出了最高的要求。
2)铸造表面必须活化,即表面粗糙化,并紧接着要洗净和干燥。
3)为了避免废品率过高,在表面活化后气缸工作表面的品质必须经过单独的步骤进行检验。
4)气缸内壁喷涂时缸孔底端必须封闭,以防止无法控制的物质进入曲轴箱中。
5)在进行气缸内壁喷涂时,喷涂器具必须伸入到缸孔中,并要在其中旋转,当气缸直径小于70 mm时,实际上就不太可能了,这就限制了这种场合的应用,特别是小排量发动机。
6)当气缸内壁喷涂过程中发生差错时,整个气缸体曲轴箱将会报废,而Sprayfit气缸套的品质是按制造工艺过程进行检验的,发现废品可立即挑选出来,然后可将这些气缸体曲轴箱重新再次压入气缸套,仍可用于批量生产,节省成本。
由于Sprayfit气缸套的生产方法是从外面喷涂在一个回转的圆柱形载体上的,因而存在为形成最佳涂层结合所有期望的自由度——获得高的过程动力学和抽走飞溅微粒的可能性,这也在与常用的气缸内壁涂层进行直接比较中显示出来。由于前者具有高的过程动力学,能够获得非常紧密的涂层,因此Sprayfit气缸套涂层甚至在如图1-45所示的极端负荷下都不会发生分离,而在窄小缸孔中的内壁热喷涂涂层却表现得差得多,当然其结合牢度用于当今发动机仍然还是足够的。
除了缸孔外面形成的喷涂层的这些一般品质差异之外,Sprayfit气缸套制造方法还为优化工作表面提供了许多其他的自由度,因此未来这种性能还能通过掺入硬质材料进一步优化,也能通过使用高Cr含量材料形成抗腐蚀的气缸工作表面。

图1-45 工作表面热喷涂工艺涂层内部粘结的比较(左:Sprayfit,右:内壁热喷涂层)
综上所述,气缸套能够采用热喷涂方法来制造,它能将气缸内壁涂层的技术优点与压入式气缸套的经济性和耐久可靠性结合起来,Sprayfit气缸套将缸孔涂层从气缸体曲轴箱中分离出来,并转变成一个完整的可压入的气缸套,它在气缸体的设计参数、涂层工艺和材料选择等方面具有很大的自由度。总之,Sprayfit技术为发动机铝机体中的铁基气缸套提供了一种创新的经济和可靠的解决方案,满足了对缸内直喷式汽油机对轻型结构和热管理方面的重要要求。