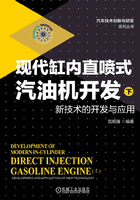
1.5 镶铸复合气缸套
随着现代缸内直喷式汽油机小型化的发展,对气缸体曲轴箱轻量化的要求越来越高,因而在批量生产中压铸铝合金的轻型结构气缸体曲轴箱应用得越来越多。由于铸铁具有众所周知的优良的摩擦性能,绝大多数压铸铝合金气缸体曲轴箱都镶铸灰铸铁(GG)气缸套,因而为了改善气缸套的导热性,灰铸铁气缸套与铝气缸体曲轴箱的结合成为其中关注的焦点。因为在镶铸灰铸铁气缸套时,由于两种材料的熔点不同而没有形成金属间的紧密融合,在不利的情况下可能形成缝隙(外表面有沟纹的灰铸铁气缸套)和孔隙(外表面铸造粗糙的灰铸铁气缸套)。由于这两种材料的热膨胀差异较大,特别是在单位面积负荷较大的情况下,可能使缝隙扩大,结果使得缸孔变形增大,结合处传热不良,热量在缝隙中聚集,并由此导致机油耗增加。此外,如果灰铸铁气缸套与铝气缸体曲轴箱结合不良的话,在预应力的作用下可能导致气缸套产生塑性变形。由于现代缸内直喷式汽油机小型化后缸心距很紧凑,气缸间的“鼻梁”宽度越来越窄,因此需要有一种设计解决方案,能够在气缸套壁厚较薄的情况下提供高的动态承载能力,并具有良好的热传导和较小的缸孔变形,同时摩擦性能也得到改善。为了达到这样的要求,Federal-Mogul公司开发了一种新型的镶铸复合气缸套,并已成功地投入了批量生产。
(1)镶铸复合气缸套的设计特点
镶铸复合气缸套采用一个灰铸铁气缸套,在其外表面预先经过机加工并对结合面进行活化处理后热喷镀AlSi合金(图1-37),这样就能够在AlSi结合层与灰铸铁之间获得无缝隙和孔隙的结合,特别是这是由两种材料相互之间紧密的机械黏合和显微焊接而形成的,而且在AlSi结合层表面形成了有利的显微孔隙度以及所要求的带有咬边的粗糙表面形状,因此在铝气缸体曲轴箱压铸过程中铸入气缸套时与渗入的铝熔液产生了非常好的黏合(图1-38)。此外,扩散过程引起了铝气缸体曲轴箱与AlSi结合层之间的材料置换,由于AlSi结合层的熔化形成了等同于焊接原理的材料复合。通过这种良好的机械复合材料的灰铸铁工作表面,发动机气缸体曲轴箱在气缸套范围内获得了高的动态强度。在脉冲压力试验中,容许的峰值压力可增加一倍而不会产生裂纹。与没有热喷镀的灰铸铁气缸套相比,这种采用镶铸复合缸套的发动机的脉冲压力试验循环数增加到3倍。这种镶铸复合缸套的另一个优点是,与外表面有沟纹和铸造粗糙的灰铸铁气缸套不同,其制作完成后的壁厚仅1.2~2 mm。由于取消了气缸套外表面诸如沟槽和凸峰之类所要求的几何形状,获得了较高的设计自由度。

图1-37 外部圆周表面经活化处理后热喷镀AlSi合金的镶铸复合灰铸铁气缸套

图1-38 铸态复合气缸套的金相图(放大50倍)
(2)气缸套镶铸状态下的性能
作用在气缸套上的预应力会使其产生静态变形,并且在发动机运转时还会增大,在正常情况下这种变形的大小应处于弹性变形极限范围之内,因而预应力消失后仍会恢复原状。但是,在非复合气缸套情况下,由于不良的力的合成,也可能产生塑性变形。无论是在85℃温度下的热态静态变形测量,还是在真实的发动机模型上进行的模拟计算都已证实,两种材料结合良好的复合气缸套在相同的负荷情况下的变形仍保持在弹性范围内(图1-39,见彩插),特别是有效减少了会明显妨碍活塞环贴合的高阶次(5阶和5阶以上)变形,因而获得了改善活塞环密封和刮油性能的潜力。

图1-39 非灰铸铁非复合气缸套(右)会产生塑性变形,而复合气缸套(左)的变形仍保持在弹性范围内
镶铸复合气缸套与铝气缸体曲轴箱之间的紧密贴合使得热导率明显提高,这有助于减少随发动机运转工况而变化的气缸变形。热盘法(Hot-Disk-Method)试验结果证实,传热增加了20%。而模拟计算表明,这种镶铸复合气缸套的温度降低了10~30℃(图1-40,见彩插)。同时,由于镶铸复合气缸套圆周上的温度稳定,降低了局部的变形峰值。

图1-40 与传统批产灰铸铁(右)相比,因结合层的热导率提高复合缸套(左)温度降低
(3)在气缸间铝鼻梁较薄场合的应用
尽管镶铸复合气缸套的壁厚较薄,但由于其确保了较高的动态结合强度,并且传热得到了改善,因此提供了减小气缸间铝鼻梁宽度的潜力。采用这种镶铸复合气缸套的发动机已批量生产,其气缸间铝鼻梁宽度为3~4mm,而采用传统的灰铸铁气缸套是无法实现如此小的鼻梁宽度的,因为在气缸间铝鼻梁中还必须同时设置冷却液缝隙或冷却液钻孔。与此相反,气缸间铝鼻梁宽度小至2mm的镶铸复合气缸套已成功地在发动机上经受了考验。
综上所述,镶铸复合气缸套在发动机运转中呈现出高的动态强度,并减小了缸孔的变形,同时即使是很薄的气缸套也能够在压铸过程中与铝气缸体曲轴箱很好地冶金结合,因此镶铸复合气缸套具有减小缸心距和气缸间铝鼻梁宽度的潜力,同时由于复合层的导热率提高,降低了镶铸复合气缸套的温度,这对减少摩擦和降低机油耗起到有利的作用。但是,在重力铸造中,这些性能尚未达到完全满意的程度,进一步优化的目标是调整铸造工艺和镶铸复合气缸套。