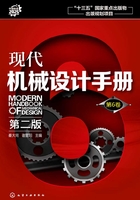
第6章 典型设备振动设计实例
6.1 旋转机械的振动设计实例
目前国内应用最广泛的机组有200MW国产汽轮发电机组以及300MW基于引进技术的汽轮发电机组,本研究以这两种类型机组为研究对象,了解这两种机组的动力学线性设计方法,将为大机组非线性动力学设计打下基础,同时研究成果可作为非线性动力学设计的对比参考依据。
6.1.1 汽轮发电机组轴系线性动力学设计
6.1.1.1 建模
在实际的转子系统中,转子是一个连续部件,因此在进行转子动力学计算和分析之前,需要把实际的转子系统抽象化、离散化,得到一个能反映原来转子系统的动力学特性,而且能适合于计算和分析的具有有限个自由度的离散化力学模型。力学模型的建立是否正确直接影响计算结果的正确性,必须予以充分重视。建立合理的计算模型要考虑以下几个方面:①反映实际转子系统的结构和工作状态;②明确所要计算和分析的力学问题;③要适应现有的计算方法和计算工具。离散化处理的方法一般分为两类:一类是对物理模型进行离散化,再对离散化的模型进行分析,这类方法主要包括集总参数法和有限元法等。如集总参数法是把一个实际的转子视作为有一根变截面轴和多个圆盘组成的系统,也就是将连续的转子简化为由许多无质量弹性轴段连接多个集总质量(节点)所构成的系统;另一类方法是维持原有模型物理和几何形态的连续性,只对其运动的数学描述进行截断而离散化,Rayleigh-Ritz法即是这类方法的典型代表。
汽轮发电机组轴系是由滑动轴承支承,滑动轴承产生动态油膜力支承轴系。油膜滑动轴承一般可线性化简化为一个具有四个刚度系数和四个阻尼系数的弹性阻尼支承,这八个系数称为油膜动力特性系数。在静平衡位置给轴颈以微小的位移或速度扰动,求解此时油膜的Reynolds方程得到油膜压力分布,然后加以积分,就可求得各油膜动力系数。轴承座一般可简化为一个有质量、阻尼和弹簧组成的单自由度系统。常把油膜的刚度、阻尼和轴承座的质量、刚度和阻尼综合成一个等效的弹性阻尼支承,并给出它的等效动力特性系数。
6.1.1.2 运动方程和求解方法
转子系统的运动微分方程式一般可写为:
式中,M为质量矩阵;C为阻尼矩阵,非对称阵;G为陀螺矩阵,反对称阵;K为刚度矩阵的对称部分;S为刚度矩阵的不对称部分;F为作用在系统上的广义外力。求解这样一个方程的特征值或响应等是很困难的,特别是当自由度较多时更为困难。在转子动力学近百年的历史,出现过许多计算方法,这都与当时的计算命题和计算工具相适应。发展到今天,现代的计算方法可以分为两大类:传递矩阵法和有限元法。传递矩阵法的特点是矩阵的阶数不随系统的自由度数增加而增加,因而编程简单,占内存少,运算速度快,适用于转子系统的动力学分析。传递矩阵法和与机械阻抗、直接积分等其他方法相结合,可以求解复杂转子系统的动力学求解问题。可以说传递矩阵法在转子动力学的计算中占据主导地位。有限元法在转子动力学的计算和分析中也有应用,这种方法的表达式简洁、规范,在求解复杂转子系统的问题时,具有很突出的优点,其缺点是往往计算时间很长。
6.1.1.3 临界转速的计算
临界转速的计算与设计是轴系线性动力学设计的传统内容,目前研究得较为成熟。其目的是使工作转速与临界转速有一定避开裕度。当临界转速与工作转速比较接近时,需要修改设计参数使轴系的临界转速偏离工作转速一定范围。
6.1.1.4 不平衡响应计算
研究不平衡响应的目的,主要用于研究转子在某些部位上的对不平衡量的敏感程度,为确定最终的设计参数提供依据。
6.1.1.5 稳定性设计
旋转机械的滑动轴承、汽封、叶尖不等蒸汽间隙等非线性因素在一定条件下可能导致转子失稳,而稳定性是制约机组能否安全运行的主要问题。动力学设计的首要任务就是通过一定的途径计算轴系的失稳转速,并使其偏离工作转速足够远。当机组的失稳转速不能精确确定,或者计算的失稳转速与工作转速比较接近,或者实际运行的机组发生了动力失稳现象,此时需要修改设计参数,提高失稳转速,以保证机组的安全。
临界转速、不平衡响应和稳定性三个内容是线性转子动力学设计的主要内容。
6.1.2 200MW汽轮发电机组轴系动力学线性分析
200MW汽轮发电机组是目前我国在役机组最多的一种类型,也是稳定性最差的一种,因此本研究首先以这一类型机组为研究对象。本节首先介绍200MW汽轮发电机组模型,然后介绍单跨转子及轴系临界转速,最后介绍轴系稳定性线性设计方法。
6.1.2.1 200MW汽轮发电机组轴系模型
200MW汽轮发电机组由高压缸、中压缸、低压缸、发电机及励磁机组成,相应的有5段转子,通过刚性联轴器连接,各段转子主要参数如表27-6-1所示。在本研究中,将200MW汽轮发电机组轴系分成151段,1~62段是高中压转子,63~89是低压转子,90~131是发电机转子,132~151是励磁机转子。
各缸体及支承情况如图27-6-1所示。转子由9个轴承支撑,高中压转子属三支承结构,低压转子、发电机转子及励磁机转子属双支承结构。
6.1.2.2 单跨轴段在刚性支承下的临界转速和模态
(1)高中压转子
高中压转子由三个轴承支承,用有限元方法将其划成62段,63个结点。表27-6-2是有限元和直接积分方法计算结果的对比,说明两种方法均可得到符合工程需要的结果。
(2)低压转子
低压转子共分为27段,28个结点,低压转子系统临界转速如表27-6-3所示。
(3)发电机转子
在转子轴承系统中,发电机转子长度最长,质量最大,油膜失稳通常发生在这段轴承上,所以研究发电机转子轴承系统的临界转速是非常重要的,其临界转速计算结果如表27-6-4所示。
(4)励磁机转子
励磁机转子轴承系统是轴系中长度最短、质量最轻的转子,临界转速如表27-6-5所示。
6.1.2.3 刚性支承轴系的临界转速及主模态
以上是轴系各个部分的临界转速,在此基础上,计算了转子轴系临界转速,如表27-6-6所示。轴系有151段,152个结点,9个刚性轴承支撑。
计算得到的轴系各阶模态如图27-6-2~图27-6-7所示。
表27-6-1 200MW汽轮发电机组转子系统基本参数


图27-6-1 200MW机组轴系的结构简图
表27-6-2 高中压转子临界转速 r/min

表27-6-3 低压转子系统临界转速 r/min

表27-6-4 发电机转子系统临界转速 r/min

表27-6-5 励磁机转子临界转速 r/min

表27-6-6 轴系临界转速 r/min


图27-6-2 轴系一阶振型

图27-6-3 轴系二阶振型

图27-6-4 轴系三阶振型

图27-6-5 轴系四阶振型

图27-6-6 轴系五阶振型

图27-6-7 轴系六阶振型
6.1.2.4 弹性支承轴系的临界转速
在油膜轴承支承下,各支座支承刚度、油膜刚度及参振质量如表27-6-7所示。弹性支承下轴系临界转速如表27-6-8所示。
根据轴系线性设计准则,要求计算转子的转速避开率如表27-6-8最后一行所示。线性设计准则要求避开率为±10%,因此该临界转速设计是合理的。
图27-6-8为基于线性动力学理论的转子-轴承系统动力学设计框图。
表27-6-7 轴承支承刚度、油膜刚度、参振质量

表27-6-8 轴系临界转速 r/min


图27-6-8 转子-轴承系统线性动力学设计框图
6.2 往复机械的振动设计实例——CA498柴油机隔振系统设计与试验研究
往复式内燃机本身存在着引发振动的激振力源,故其振动是不可避免的。内燃机的振动不仅使机器自身的可靠性和寿命下降,而且噪声污染也很严重。随着内燃机向高速、大功率、轻型化方向发展,其振动也进一步加剧。因此,加强对内燃机隔振系统的设计研究显得非常重要。
6.2.1 柴油机振动扰动力分析
柴油机运转时产生的激励主要有两种:一是运动部件的惯性力形成的不平衡力和力矩,属于低阶激励,其激励幅值取决于运动部件的质量、发火顺序、缸数、冲程数、活塞行程及转速,激励频率取决于发火顺序、缸数、冲程数、活塞行程和;二是气缸内油气燃烧后产生气体压力和往复惯性力合成后导致的倾覆力矩,属于高阶激励,其激励幅值取决于缸径、活塞行程、工作压力、缸数、冲程数和转速,其频率取决于缸数、冲程数和转速。
对于CA498柴油机来说(基本参数见表27-6-9),引发柴油机振动的主要扰动力包括往复惯性力及其力矩、倾覆力矩等不平衡量的简谐分量。由于其曲轴采用均匀镜像对称布置,其一阶往复惯性力和惯性力矩以及二阶往复惯性力矩都是平衡的,即:∑Pj1=0;∑Mj1=0;∑Mj2=0;只有二阶往复惯性力∑Pj2≠0,以及倾覆力矩的不平衡分量∑Mp≠0。
表27-6-9 CA498柴油机基本参数

二阶往复惯性力为:
在标定工况下,其最大值为3895.5N。倾覆力矩的不平衡分量为:
式中,Pnp为简谐分析中由气体力所引起的第n次切向力;Pnw为简谐分析中由往复惯性力所引起的第n次切向力;εn为第n次简谐扭矩的初始相位角;A为活塞面积;R为曲柄半径。
倾覆力矩的计算,取劳氏简谐系数,其2、4、6阶倾覆力矩的最大值分别为:491.9N·m、226.3N·m、84.3N·m。
6.2.2 柴油机隔振系统设计模型
在进行柴油机隔振系统分析计算时,必须先确定机器的重心,本例采用图27-6-9所示的柴油机安装简图,并以重心G为原点建立坐标系。X、Y、Z方向分别为柴油机的水平、垂直和曲轴轴线方向。

图27-6-9 柴油机计算模型简图
由于CA498柴油机自身条件的限制,其减振器的安装位置不能任意选取,根据原先的设计,置于图中所示的坐标系中的坐标如表27-6-10所示。
表27-6-10 减振器的安装位坐标 mm

6.2.3 隔振方案的选择
由CA498柴油机振动源的分析可知,其主要的振动是二阶往复惯性力所引起的Y向的垂直振动和倾覆力矩的不平衡分量所引起的Y方向的横摇振动,故因首先考虑将这两种振动分开,本例采用对称于柴油机轴线的斜支撑布置,这样可产生两组三联耦合振动:垂向-纵向-纵摇及平摇-横向-横摇。
因为各支撑点的载荷相差较大,本例采用两种不同型号的隔振器斜支承布置,为了达到良好的隔振效果,隔振装置的固有频率与相应的扰动频率之比,应小于。为达到η≥80%的隔振效率,频率比应为2.5左右。所以,隔振装置的固有频率Fn不应大于:
在不改变CA498柴油机原减振系统设计安装角度的基础上,对隔振器的特性进行分析试选,最终确定的四块减振垫的刚度如表27-6-11所示。
表27-6-11 减振器的三向刚度值 N/mm

根据以上刚度值对柴油机系统进行自由振动和强迫振动计算,可得到如表27-6-12所示结果。
表27-6-12 六个自由度自振频率及一次临界转速

通过进一步计算可以确定各转速下的减振效果,其垂向减振度如图27-6-10所示。

图27-6-10 垂向减振度随转速变化
从图27-6-10可以看出,在转速超过1600r/min时,其垂向隔振效率都可以达到80%。另外由于横摇方向的一次临界转速达到了1307r/min,故在转速较低时可能引起平摇-横向-横摇耦合共振,但由于其振动的激振力矩不大,不会引起严重的后果。
6.2.4 结论
①CA498柴油机在安装了上述减振系统后,其额定工况的振动烈度可以从原先的D级改善为C级,表明该减振系统的设计是成功的。
②考虑到橡胶减振垫具有一定的阻尼,故在转速较低时,振动会由于阻尼的原因而得到一定程度的抑制。
③由于CA498柴油机具有较大的转速范围,仅仅靠安装减振垫很难做到在所有转速下的振动都符合标准。
④从分析结果来看,二阶往复惯性力是直列四缸机的主要激振源,故应力求减小二阶往复惯性力,例如加装二次往复惯性力的平衡装置等。
6.3 锻压机械的振动设计实例
锻压机械是指在锻压加工中用于成形和分离的机械设备。锻压机械包括成形用的锻锤、机械压力机、液压机、螺旋压力机和平锻机,以及开卷机、矫正机、剪切机、锻造操作机等辅助机械。锻锤是最常见、历史最悠久的锻压机械,由重锤落下或强迫高速运动产生的动能,对坯料做功,使之塑性变形。它结构简单、工作灵活、使用面广,但振动较大。因此,本节以锻锤为研究对象论述其隔振设计。
6.3.1 锻锤隔振计算
6.3.1.1 锻锤隔振的基本计算
如图27-6-11所示,锻锤的隔振系统应该属于两自由度质量-弹簧系统,基础块和基础箱简化为质量,隔振器和地基简化为弹簧。但当锻锤采取了隔振措施后,隔振器的刚度远远小于基础箱下地基的刚度,二者耦合作用小,故基础块(即隔振台座)和隔振器之间、基础箱和地基之间可以分别按单自由度质量-弹簧系统进行计算。

图27-6-11 锻锤隔振计算简图
重锤(下落质量)m0以最大速度v0与锻锤基础块相碰撞,使基础块获得初速度v1,从而引起隔振系统的自由振动。按图27-6-11所示的动力学模型列出基础块的运动微分方程为
(27-6-1)
式中 m1——隔振器上面基础块、砧座、锤架等的总质量,kg;
Kz——隔振器总的垂向刚度,N/m;
v1——基础块的初速度。
初速度v1可由动量守恒定律得出
(27-6-2)
式中 m0——重锤(落下部分)质量,kg;
e——碰撞系数,亦称冲击回弹系数,取决于碰撞物体的材料:对于模锻锤,锻钢制品时e=0.5,锻有色金属时e=0.25;对于自由锻锤e=0.25。
由式(27-6-1)和式(27-6-2)求出基础块的振幅为
(27-6-3)
(27-6-4)
由于m0通常远小于m1,所以Az和ω0可按下面两式近似计算
(27-6-5)
(27-6-6)
锻锤的隔振效率β采用在隔振和不隔振情况下传递到基础的力进行评定,即
(27-6-7)
式中 ,
——不隔振情况下基础的振幅和地基刚度。
如果隔振基础与不隔振基础质量相等,则式(27-6-7)可写为
(27-6-8)
锻锤基础隔振后所引起的锤击能量损失是很小的,可以不考虑。
6.3.1.2 砧座下基础块的最小厚度要求
安装在隔振器上面的基础块,其砧座下部的厚度不应小于表27-6-13中的规定值。当有足够的根据时,才允许将最小厚度适当减小。
表27-6-13 砧座下基础块的最小厚度

6.3.1.3 三心合一问题
机架、砧座和基础块的质心、落体打击中心和隔振器的刚度中心应在同一垂线上,以避免因偏心打击而出现回转振动。当不能满足这一要求时,基础块的质心、隔振器刚度中心和落体打击中心三者的偏离均不应大于偏离方向基础边长的5%,此时可按中心冲击理论进行计算。对于偏心锤(吨位小于1.0t),则应外调基础来满足三心合一的要求。
6.3.1.4 阻尼问题
锻锤隔振系统的阻尼比至少应大于0.10,一般应在0.15以上,最好在0.25左右。阻尼比大(一般不要超过0.30),能起到以下作用。
①冲击过后,锻锤基础能迅速回到平衡位置。
②在锻锤隔振中,增大阻尼比能起到相当于增加基础质量的作用,从而抑制振幅的大小。这也是实测振幅值一般总小于不考虑阻尼时理论计算值的主要原因。从这个意义上讲,阻尼能使振幅计算加上保险系数。另一方面,这也是在砧座下直接实施隔振措施的重要原因之一。
6.3.1.5 隔振基础的结构设计
1)锻锤隔振基础和基础箱均应为钢筋混凝土结构。隔振器一般采用支承方式装在基础块和基础箱之间,见图27-6-12。设计时必须设置能自由通向各个隔振器的通道,基础块侧边与基础箱侧边之间的宽度不应小于60cm,隔振器应布置在凸出基础箱的钢筋混凝土带条上。为便于检查和拆摸每个隔振器,在基础块底面和基础箱之间应留出不小于70cm的空间。
2)设计隔振锻锤基础块,应采取下列措施。
①在基础块和基础箱之间铺设活动盖板,盖板下设置柔性衬垫。
②在槽衬留出积水坑,以便排出水和油等液体。
③锤的导管连接做成柔性接头。
④安装隔振器的上、下部位应平整地设置钢板埋设件。
⑤基础块和基础箱之间设置水平限位装置,以避免基础滑动。水平限位装置可由厚钢板加型钢物件连接而成,其横向刚度比隔振器刚度小很多,不会影响隔振基础的隔振效果,而它的纵向刚度较大,可以限制基础的侧向位移,见图27-6-12。
6.3.2 锻锤隔振基础的设计步骤
6.3.2.1 搜集设计资料
进行锻锤隔振基础设计时,应具备下列资料:
①锻锤的基本尺寸、类型、牌号和制造厂;
②落体的质量;
③落体的最大速度;
④砧座和机架的质量;
⑤每分钟的冲击数;
⑥锻锤质量和基础箱的允许振幅或允许振动速度。
6.3.2.2 初步确定基础块的质量和几何尺寸
(1)确定落体的下落速度(亦称锤击速度、冲击速度)v0
落体(锤头)的锤击速度v0一般可由说明书上查得。如果说明书上未说明,则可按式(27-6-9)或式(27-6-10)求得。
对自由落锤
(27-6-9)
对双动作用锤,其锤头下落时最大速度v0为
(27-6-10)
式中 h0——落体(锤头)最大行程,m;
W0——落体重量,kN;
p——气缸最大进气压力,kPa;
As——气缸活塞面积,m2;
g——重力加速度,m/s2。

图27-6-12 锻锤隔振基础结构
如果说明书中仅给出了打击能量E0,而未给出其他值,则v0可以按式(27-6-11)计算
(27-6-11)
式中 E0——打击能量,kN·m;
m0——总体质量,t。
(2)确定基础块的质量
基础块的质量可按式(27-6-12)计算
(27-6-12)
式中 mp——砧座质量,t;
m2——机架质量,t;
m0——落体质量,t;
ω0——基础的固有频率,rad/s;
e——碰撞系数,按式(27-6-2)下说明选取;
[Az]——砧座允许垂向振幅,可按表27-6-14选用(目前研究成果允许振幅放宽,这将在后面讨论)。
表27-6-14 砧座允许垂向振幅

(3)确定基础块的外形尺寸(略)
6.3.2.3 确定隔振器应具备的参数并选用或设计隔振器
①确定基础固有频率。一般来说,基础固有频率可在3~6Hz范围选取。近些年又有新的选择,将在后面讨论。
②由Kz=m1决定隔振器的垂向刚度。
③阻尼比至少应大于0.10,最好大于0.15,则可以不考虑冲击隔振。
根据Kz和阻尼比ζ选用或设计隔振器。一般来说,多采用钢弹簧和橡胶并用,或钢弹簧和油阻尼器,或钢弹簧与黏滞性阻尼器,或钢弹簧和钢丝绳隔振器并用,还有采取蝶簧和阻尼器并用。
6.3.2.4 基础块振动验算
由式(27-6-3)计算的振幅Az必须小于允许振幅[Az]。
6.3.2.5 砧座振幅验算
砧座振幅Az1可由式(27-6-13)计算得到,其应该小于表27-6-14中的规定值。
(27-6-13)
式中 Az1——砧座振幅,mm;
ψe——冲击回弹影响系数,对模锻钢制品可取0.5s/m1/2;对模锻有色金属制品可取0.35s/m1/2,对自由锻锤,可取0.4s/m1/2;
d0——砧座下垫层的总厚度,m;
E1——垫层的弹性模量,kPa;
Wp——对模锻应取砧座与锤架的总重力,对自由锻应取砧座的重力,kN。
6.3.2.6 基础箱的设计及振幅
根据基础块的外形尺寸,由静力计算和构造要求确定基础箱的外形尺寸及其质量。有关参数还要保证基础箱振幅A'z小于允许的振幅。
(27-6-14)
式中 K'z——地基抗压刚度;
S'——基础底面积,基础底面积可先由基础块外形确定,再验算;
αz——基础埋深作用对地基抗压刚度的提高系数;
δb——基础埋深比,当δb>0.6时,取δb=0.6;
ht——基础埋置深度。
6.3.3 设计举例5t模锻锤隔振基础设计
6.3.3.1 设计资料及设计值
(1)锻锤原始资料
锤头质量 m0=5.79t
砧座质量 mp=112.55t
机架质量 m2=43.7t
最大打击能量 E0=123kN·m
锤击次数 60次/min
(2)地质勘测资料
非湿陷性黄土状亚黏土 R=198kN/m2,
ρ=17.66kt/m3
地基抗压刚度系数 Cz=73550kN/m3
土壤内摩擦角 φ=20°,μ=0.49
地下水位于地面下14m处。
(3)设计要求
基础允许垂向振幅[Az]≤3mm
基础固有频率f0≤3.5Hz
砧座允许垂向振幅[Az1]≤4mm
基础箱允许垂向振幅[A'z]≤0.2mm
6.3.3.2 确定基础块的质量和几何尺寸
(1)确定落体的下落速度
由式(27-6-11)确定落体的下落速度可得
(2)确定基础块质量
取e=0.5,ω0=2πf0=6.28×3.5rad/s=22rad/s,[Az]=0.003m,则由式(27-6-12)可得基础块质量
(3)确定基础块外形尺寸
基础块为钢筋混凝土结构,故基础块所需体积V3为:
基础块几何尺寸(长L×宽B×厚H)取
实际质量
总质量
6.3.3.3 隔振器的选用与设计
由可得到
全部载荷可由40个隔振器承担,每个隔振器的承载为
每个隔振器的刚度
6.3.3.4 基础块振动验算
设实际加工的钢弹簧隔振器的刚度为103394N/cm,则
由式(27-6-3)可得
,允许
6.3.3.5 砧座振幅验算
砧座采用运输胶带,厚度为100mm,由《动力机器基础设计规范》GB 50040—1996中表8.1.21知,E1=38000kN/m2,按式(27-6-13)有
6.3.3.6 基础箱设计
由《隔振设计规范》GB 50463—2008查得地基调整系数αz=2.67。由式(27-6-14)可得
取S'=120m2允许,则基础箱底面尺寸应为12×10m2=120m2。
6.3.4 有关锻锤隔振新理论、新观念、新方法介绍
6.3.4.1 锻锤基础弹性隔振新技术
锻锤基础弹性隔振技术主要分为两大类:一类是砧座下直接隔振技术,将刚度较小的弹性元件及阻尼元件直接设在砧座下部以代替原有刚度很大的垫幕;另一类是大质量基础弹性隔振技术,即将锻锤安装在大质量块上,在质量块下面加弹性元件和阻尼元件,也有采用刚性浮筏结构的形式。
(1)砧座下直接隔振技术
在20世纪70年代,在国际上(以德国Gerb防振工程有限公司为代表)发展起砧座下直接隔振方式,即将刚度较小的弹性元件及阻尼元件直接设在砧座下部以代替原有刚度很大的垫幕。这种方式结构简单、施工方便、成本低、易于推广。由于在隔振器上部缺少了质量很大的基础块,故必然使砧座本身产生很大的振幅,影响打击效率、设备寿命和工作精度。国内外对此展开了一系列理论研究和工程实践,基本结论为:
①在通常情况下,隔振系统的固有频率可以在5~8Hz范围内选取;砧座振幅允许在10~20mm之内。
②无论是自由锻还是模锻锤,当砧座振动加大到10~20mm,也不会妨碍生产操作。手工操作时,操作者会很快适应砧座10~20mm幅度的低频晃动。
③由于锻锤砧座质量一般均在落下部分质量的15倍以上,砧座10~20mm的退让量不会影响打击效率。
④砧座10~20mm的振幅不会妨碍锻锤的正常运转,并且在某些情况下有助于改善应力,有助于保护设备和模具。
⑤阻尼在锻锤隔振中起着十分重要的作用。值得指出的是,合理的阻尼不仅能提高工作效率,而且还能抑制砧座振幅。一般情况应使阻尼比大于0.15,在0.15~0.30范围内选取为好。
(2)大质量基础弹性隔振技术
加大锻锤的基础质量, 可以减小振幅。足够的质量提供了惯性力来平衡扰力。通常是通过加大基础几何尺寸的办法来实现加大质量, 当然亦不可太大, 一般视锻锤吨位而定。为避免与厂房基础干涉, 对于小型锻锤可以加深基础, 也可以加钢架、钢板以增加惯性质量, 对于大中型锻锤设备则一般需要混凝土基础块, 以避免与底座本身产生共振。
当前两类隔振技术研究的重点和难点均集中在弹性与阻尼元件(或系统)的设计开发上,主要分为以下几类:大载荷弹簧阻尼液隔振器、橡胶隔振器和橡胶隔振垫、空气弹簧、液压阻尼减振器和多层弹性体阻尼模块隔振系统。
(1)大载荷弹簧阻尼液隔振器
这种类型隔振器是由钢螺旋压缩弹簧与黏滞性阻尼并联而成,组合在一个箱体内,近年来已广泛用于大/中型锻锤、压力机、空压机等设备的隔振。
这类大载荷弹簧阻尼液隔振具有以下几个特点。
①工作载荷范围大,工作载荷已可做到1000 kN。
②固有频率范围宽,在同样工作载荷下,因有不同的刚度,固有频率范围为2~8 Hz,为不同类型设备隔振提供了很大选择余地。
③阻尼比大,在同样工作载荷和刚度情况下,阻尼比可以做到0.30以上,这对冲击运动的隔离十分有利。如将阻尼比选择在0.30左右,则既能提高冲击隔振效果,又能减少工作台面的位移。在体积不大的情况下,做到阻尼比0.30以上,并且温度适用范围宽。
④隔振器和阻尼器可以分开安装,如果二者并在一起装在一个箱体之内,则阻尼器不必单独固定。箱体往往做成预压状态,这样在维修与更换隔振器时,可以做到设备不动,更换过后,一般情况下设备水平无需再调整。
⑤隔振器寿命长,其寿命至少为15年以上。
但采用大载荷弹簧阻尼液隔振器也存在如下缺点。
①弹簧阻尼液隔振系统价格高昂,隔振系统容易损坏,主要是阻尼液对环境影响非常敏感,怕水和油,容易泄漏,而锻造行业的恶劣环境却又是难以控制和想象的。
②弹簧容易被小颗粒和氧化皮等损坏,弹簧的疲劳及阻尼器的损坏又不断地需要修理和更换。
③安装弹簧隔振器需要大的水泥或钢铁配重来达到合格的锻锤垂直振幅,这是因为弹簧非常软或刚度过于小。
(2)橡胶隔振器和橡胶隔振垫
砧座下直接隔振常采用橡胶隔振器和橡胶隔振垫。其优点是投资少,但难以做到隔振效率很高,另外其阻尼比最多做到0.15。研究表明,采用有孔的橡胶垫,其阻尼性能比普通橡胶垫要好一些。此种隔振方法投资少,故也会得到一定程度应用。但是橡胶元件的弹性是通过元件的形状变化而得到的,因此其变形量是有限的,所支承的系统固有频率也很高,由于它是非线性的,在大载荷时会变硬。在橡胶作为阻尼元件时,其阻尼效应引起的热量也会降低橡胶的弹性阻尼特性。
(3)空气弹簧
该型减振器在锻锤弹性隔振上的应用主要以日本日野、三菱减振器为代表,其是一种帘线增强的橡胶囊,内充压缩空气,利用气体的可压缩性起弹簧作用的减振橡胶制品,有长枕式、葫芦式和隔膜式等类型。空气弹簧可以大致分为自由膜式、混合式、袖筒式和囊式空气弹簧,其橡胶囊结构与无内胎轮胎相似,由内胶层(气密层)、外胶层、帘布增强层及钢丝圈组成,其载荷主要由帘线承受。帘线的材质是空气弹簧的耐压性和耐久性的决定性因素,一般采用高强度的聚酯帘线或尼龙帘线,帘线层交叉并且和气囊的经线方向成一角度布置。与金属弹簧相比,气囊具有质量小、舒适性好、耐疲劳、使用寿命长等优点,它同时具有减振和消声作用,但其在使用时需要增设气站,增加了成本和空间。
(4)液压阻尼减振器
由于液体阻尼的稳定性、即时性、紧凑性及可控性,以德国Gerb防振工程有限公司为代表开发了一系列液压阻尼器。其基本形式是由缸筒、活塞、阻尼材料和导杆等部分组成,活塞在缸筒内作往复运动,活塞上开有适量小孔作为阻尼孔,缸筒内装满流体阻尼材料。当活塞与缸筒之间发生相对运动时,由于活塞前后的压力差使流体阻尼材料从阻尼孔中通过,从而产生阻尼力。黏滞流体阻尼器对锻锤振动控制的机理是将结构的部分振动能量通过阻尼器中黏滞流体的阻滞作用耗散掉,达到减小设备振动的目的。
(5)多层弹性体阻尼模块隔振系统(MRM)
由美国减振技术公司研发的多层弹性体阻尼模块隔振系统(MRM)是近年来锻锤弹性基础隔振的最新技术。MRM隔振系统耐油和水、耐热和防老化的物理特征佳。当弹性体模块构成MRM受压缩时,弹性体模块就开始以热能的形式散发热量,热量从弹性体阻尼模块传递到钢板中,然后又在环境的空气中散发掉。多层弹性体阻尼模块隔振系统(MRM)可提供约60%~85%的隔振效果,隔振系统固有的振动频率范围为8~15Hz。通常MRM的混凝土基础比弹簧隔振器的混凝土基础要小。
6.3.4.2 锻锤隔振系统的CAD二次开发与智能制造
锻锤隔振装置主要采用手工设计,设计效率低、直观性差、重复性工作多、往往要查阅手册、计算和校核许多数据、绘制大量图形。因此改变传统的设计方法,采用与CAD相结合的技术成为一种趋势。对于Pro/E这类通用软件,其自身标准与国内标准存在差异,而且缺乏锻锤隔振方面的专业模块,近年来不少学者提出了在Pro/E平台上对锻锤隔振CAD系统进行二次开发并以此开展智能制造的新思路。
随着计算机图形技术和三维CAD开发软件的成熟,基于AutoCAD和Pro/E软件作为二次开发平台,根据锻锤隔振的设计原理,利用VC++6.0的MFC和Pro/E自带的二次开发工具包Pro/TOOLKIT开发出一套界面友好、交互性强的锻锤隔振CAD系统,研究的重点方向如下。
①解决Pro/E软件、VC++6.0编译器以及ACCESS数据库之间的通信及有关接口技术。分析Pro/TOOLKIT内部的基本数据结构、功能函数及其使用方法,研究基于OLE DB、DataGrid的方式将ACCESS数据库与VC++6.0连接,实现外部数据库与Pro/E软件的结合。
②研究基于Pro/TOOLKIT的菜单设计技术以及Pro/TOOLKIT与MFC的混合编程技术,研究菜单资源文件、注册文件的建立方法,实现锻锤隔振CAD系统可视化界面设计。
③研究锻锤隔振CAD系统开发的关键技术,在基于特征的参数化、Pro/TOOLKIT应用程序设计的基础上,提出了基于三维模型的参数化自动建模技术。根据锻锤隔振的设计原理,设计板簧悬吊式隔振参数化系统、螺旋弹簧及橡胶阻尼器的承垫式、反压式、惯性块式隔振参数化系统。实现各类隔振系统零件、组件的三维模型及二维工程图的自动化生成。
④设计锻锤隔振系统标准件数据库,通过ACCESS创建的标准件库零件参数数据库来驱动模型参数,实现对所选标准件进行自动建模。
⑤对Pro/E进行合理配置并编写BOM格式文件,实现自动生成锻锤隔振CAD系统零部件的BOM清单功能。将零部件的信息(如质量、名称、图号、材料、备注等)通过清单形式进行出,实现智能制造。
6.3.4.3 锻锤基础隔振的参数优化设计方法
锻锤弹性基础的减振效果取决于弹簧刚度、阻尼器阻尼系数、基础块质量及外形尺寸等参数的选取,同时受约束于设计要求及其结构和工艺条件。由于影响因素多,且参数间关系复杂,传统设计方法无法满足设计要求,需要使用目标函数优化。参数优化设计方法通常遵循如下步骤。
(1)建立动力学微分方程
由于锻锤隔振所采用的隔振器的刚度远小于机架、砧座与惯性块之间的垫层刚度,因此无论是砧座下直接隔振还是质量块隔振,都可以简化为两自由度系统,如图27-6-13所示。

图27-6-13 锻锤动力学模型
系统的运动微分方程为
(27-6-15)
式中,K1、K2分别为隔振器弹簧刚度和土壤刚度;C1、C2分别为隔振器阻尼系数和土壤阻尼 系数; x1、x2分别为砧座和基础块的位移;m1为砧座质量(自由锻锤)或机身与砧座质量之和(模锻锤);m2为机架与基础块质量之和(自由锻锤)或基础块质量(模锻锤)。
(2)确定系统的初始条件
如锤击速度、土壤参数和设计要求等,具体确定方法已在6.3.3节给出。
(3)建立优化设计的数学模型
对锻锤弹性基础优化设计需要满足以下基本要求:基础和砧座的振幅在允许范围内;作用于地基上的动应力应在允许范围内。当锻锤参数及地基条件确定后可根据上述要求建立优化设计数学模型。
①确定目标函数。可以根据实际的优化要求确定目标函数,可以对单参数也可以是多参数的,通常以基础的力传递率作为目标函数。
②确定约束条件。一般为砧座的最大振幅约束、基础块的振幅和最大加速度约束、地基承受的最大动载约束、基础自振频率约束、振动衰减时间约束和设计变量的边界约束等。
③选取优化算法开展优化设计,常用的优化算法如序列二次规划法、时频域函数优化参数混合算法和遗传算法等。