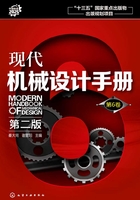
第5章 机械振动控制
振动的危害:影响机械设备的正常工作;降低机床的加工精度;加速机械设备的磨损,甚至导致机械结构破坏;同时振动产生噪声,污染工作和生活环境,危害人体健康。随着生产与工业技术的进步,新的高强度材料不断被采用,新的结构形式不断出现,对机械设备的运转速度、承载能力、工作精度、稳定性和工作环境等方面的要求越来越高,导致振动问题日益突出,对机械设备的振动控制越发迫切和重要。
5.1 振动控制的基本方法
5.1.1 常见的机械振动源
引起机械振动的原因很多,常见的典型机械振动源如下。
(1)运转机械的不平衡
一般机械可以分为旋转式机械和往复式机械两大类。旋转式机械,如泵、风机、电机等静、动平衡相对比较容易实现,但是由于加工、装配和安装精度等原因,不可避免地或多或少存在偏心,机器作旋转运动时产生不平衡离心惯性力是旋转式机械主要的振动源,不平衡引起转子的挠曲和内应力,使机器产生振动和噪声;而往复式机械,如柴油机、往复式空气压缩机的曲柄-滑块机构运动无法达到完全平衡,机器运转时总存在周期性的扰动力,特别是缸数少的柴油机常成为主要振动源。由运转机械的不平衡所引起的机械振动具有明显的规律性,其振动频率等于机械运转的转速或是其倍数。
(2)传动轴系振动
传动轴系的振动有:
①由原动机的转矩不均匀引起的扭转振动;
②由轴系不对中和过分的轴向间隙相结合、推进器非定常推力引起的轴系纵向振动;
③由轴系转子不平衡引起的横向振动。
(3)冲击运动引起的振动
如冲压设备、冲床、锻床引起的冲击力振动。
(4)管路振动
由原动机传递的管壁周期性振动和由流体脉动压力激发的管路振动。
(5)电磁振动
由电机定子、转子的各次谐波相互作用以及磁极气隙不均匀造成定子与转子间磁场引力不平衡等原因引起发电机、电动机的振动。
(6)其他
由外界激励,如风载、重型交通工具行驶诱发的机械设备的随机振动。
5.1.2 振动控制的基本方法
机械振动控制包含振动利用和振动抑制两个方面。前者指利用机械系统的振动以实现某种工程效用,例如各种振动机械,见第6章。后者则指抑制机械系统的振动以保证系统正常工作,本章所说的振动控制是指后者,是减小结构系统或各种设备的振动效应。振动控制的基本方法可分为主动控制和被动控制两个大类。减小和控制振动的方法可归纳为以下几种。
(1)减小或消除振动源激励
①选择噪声低、振动小的机械设备,或重新设计机械设备结构以减小振动,如重新设计凸轮轮廓线,减少曲柄行程,减少摆动质量等。
②改善机械设备内部平衡。采用静、动平衡改善机械设备的平衡性能。
③改进加工工艺,提高制造加工装配质量。严格质量检验,减小制造误差,提高平衡精度,保证安装质量。
④提高机械设备的结构阻尼,以减弱噪声振动激励。
(2)防止共振
①改变机械设备振动系统的固有频率。如采用局部加强结构,改变轴颈尺寸等。
②改变机械设备的扰动频率。如改变机器转速。
(3)隔振——隔离振动波的传递路径,减小或隔离机械设备的振动传递
①隔离振源,即隔离机械设备本身的振动通过其机脚、支座传至基础或基座,目的是隔离或减小动力的传递。
②隔离响应,即防止周围环境的振动通过支座、机脚传至需要保护的机械设备,目的是隔离或减小运动的传递。
(4)吸振——增设辅助性的质量弹簧系统,吸收振动能量
安装动力吸振器,扭振减振器。动力吸振器的作用是吸收振动能量。
(5)阻振——增加阻尼以增加振动能量耗散降低共振幅值
在机械设备结构表面粘贴黏弹性阻尼材料或敷设阻尼涂料以减小机械设备结构振动时共振响应的幅值。
5.1.3 刚性回转体的平衡
当回转体的工作转速远低于其一阶临界转速,此时不平衡离心力较小、回转体比较刚硬,不平衡力引起的转子挠曲变形很小(与转子偏心量相比),可以加以忽略,这种回转体称为刚体回转体。由于制造和装配误差产生的偏心;安装间隙不均匀,转动部件间的相对移动;材质不均匀;回转体存在初始弯曲等原因,实际回转体的中心惯性主轴或多或少地偏离其旋转轴线,因此当回转体转动时,回转体的各微元质量的离心惯性力所组成的力系不是一个平衡力系,这时回转体不平衡或失衡。由刚体回转不平衡产生振动的特点是振动的频率和回转体转动频率相同。
回转体不平衡的类型可分为四类:静不平衡;准静不平衡;偶不平衡;动不平衡。静不平衡和准静不平衡可合称为静不平衡。
刚性回转体的平衡是在回转体选定适当的校正平面,在其上加上适当的校正质量(或质量组),使得回转体(或轴承)的振动(或力)减小至某个允许值,方法有:单面平衡法和二平面平衡法。表27-5-1给出了一般刚性回转体的静平衡和动平衡的要求,它主要取决于刚性回转体的长度对其直径之比和工作转速。
表27-5-1 刚性回转体的平衡方式

5.1.4 挠性回转体的动平衡
挠性回转体的转速大于其第一阶临界转速,在高转速下会因偏心离心力的作用产生较大的弯曲变形,平衡时必须考虑自身变形的影响。挠性回转体应在高速平衡机上,使用特有的方法,例如振型平衡法、影响系数法进行平衡。
高速动平衡是一个多平面多转速的动平衡过程,回转体主要是在工作转速上的动平衡,把力与力偶的不平衡量以及所出现的各阶固有振型不平衡量依次降低到许可范围。挠性回转体的动平衡的方法基本上可归纳为两大类,第一类是模态平衡法,第二类是影响系数法。目前是趋于将以上两种方法结合起来对转子进行平衡,并应用计算机进行计算与数据处理以提高平衡自动化和精度水平。
5.1.5 往复机械惯性力的平衡
往复机械运转时所产生的往复惯性力和惯性力矩;旋转离心力及离心力矩;以及颠覆力矩的不平衡的简谐分量,将传递到往复机械的机体支承,这些力和力矩都是曲轴转角的周期函数,是一种周期性的激励。往复机械的平衡,就是采取措施抵消这三种激励力和力矩,或使它们减小到容许的程度。
为使往复机械有较好的静力平衡和动力平衡,在设计和制造过程中应使各缸活塞组的重量、连杆重量以及连杆组重量在其大端和小端的分配时控制在一定的公差带内。曲轴在装入往复机械以前,也应将其不平衡的质量(包括静平衡和动平衡)控制在规定的公差范围内。具体平衡方法,可查阅有关手册。
5.2 定性减少振动的一些方法和手段
振动控制方法很多,可根据不同情况、不同要求,而采用不同的措施。除上述振动控制基本方法外,还可以通过下述方法和手段定性减少机械设备的振动和振动传递。几种主要的振动控制措施是结构元件的刚化、谐振系统的解调或去耦、普通振动隔离、大阻尼隔振、动态振动吸振和加缓冲器。
(1)改变振源机械结构的固有频率
当机械设备发生局部振动时,采用刚化方法,提高结构元件的刚性,从而提高其谐振频率,使其具有较高的强度,以改善对振动环境的防护能力。
(2)加大机械设备和受振对象之间的距离
在动力设备布置时综合考虑,可将设备分别置于楼层中不同的结构单元,如设置在伸缩缝、抗震缝的两侧,起到增加传递路径作用;又如采用隔振沟可减少机械设备冲击或频率大于30Hz以上高频振动的传递。
(3)机械设备和管路系统的连接
在动力机械设备与管道之间采用柔性连接,如在水泵进出口处加装橡胶软接头,柴油机排气口与管道之间加装金属波纹管。在管道穿墙壁时,在管道与墙体之间应垫弹性材料,减少管道振动通过墙体传递给建筑结构。
(4)精密设备隔振
精密设备的工作台宜采用刚度大的钢筋混凝土水磨石工作台和混凝土地坪,必要时混凝土地坪大于500mm。
(5)采用黏弹性高阻尼材料
对于具有薄壳机体的机械设备,宜采用黏弹性高阻尼材料增加设备结构阻尼,增加振动能量消耗,减小振动。
5.3 隔振原理及隔振设计
机械设备的隔振通常是采用一级隔振系统,有时也采用二级隔振系统。对于一般机械设备的一级隔振系统设计计算,仅考虑一个方向,通常是垂直方向,即为单自由度隔振系统;对于大型、重型机械设备和精密设备隔振系统,需考虑空间6个运动方向,即6个自由度系统,需采用计算机设计计算。
5.3.1 隔振原理及一级隔振动力参数设计
表27-5-2 一级隔振系统动力参数


5.3.2 一级隔振动力参数设计示例
图27-5-1所示某柴油发电机组总质量m1=10000kg,转子的质量m0=2940kg,转子回转转速1500r/min,偏心质量激振圆频率ω=157rad/s。多缸柴油发电机组(包括风机在内)的平衡品质等级为G250,回转轴心与m1的质心基本重合,试设计一次隔振系统动力参数。

图27-5-1 某柴油发电机组隔振系统力学模型
(1)确定频率比ω/ωn和系统固有频率
选取绝对传递率TA为0.05,不计阻尼,隔振系统频率比为:
,设计时取为4.5,则
系统固有频率
(2)隔振器总刚度K1
采用8个橡胶隔振器、对称布置,每个隔振器刚度K1为
(3)激振力幅值F0
式中,转子质量偏心半径
(4)稳态响应振幅幅值A
(5)传给基础的动载荷幅值
5.3.3 二级隔振动力参数设计
一级隔振系统的振级落差一般为10~20dB,若要提高振级落差,可考虑采用二级隔振系统,即在被隔离的机械设备和基础之间再插入一个弹性支承的中间基座(二次隔振架),二级隔振系统的振级落差,在低频区一般可达到30~40dB,高频区可达50dB以上。二级隔振系统包括机械设备和中间质量两个部分,具有12自由度,即机械设备6自由度,中间质量6自由度,用计算机由专用程序实现设计计算。工程中通常关心的是垂直方向振动,这样可把二级隔振系统简化为两自由度振动系统。
表27-5-3 二级隔振系统动力参数


5.3.4 二级隔振动力参数设计示例
某直线振动机二次隔振力学模型如图27-5-2所示,其质量m1=7360kg,在与水平方向成α角的方向上施加激振力F(t)=F0sinωt,激振力幅值F0=258.3kN,激振频率ω=83.78rad/s。一次隔振器动力参数设计确定隔振器垂向(x)总刚度K1x=1.972×106N/m,水平向(y)总刚度K1y=1.399×106N/m,采用8只刚度为K'1x=2.465×105N/m,K1y=1.749×105N/m的隔振器,传给基础的动载荷幅值分别为FTx=6508N,FTy=5500N,该振动机安装在上层楼板后,由于激振频率ω和楼板的固有频率接近,楼板产生强烈的拍振。为减轻楼板振动,试进行二次隔振系统动力参数设计。
(1)质量比
首先选取Ks=1.05,Kp=1/7,则
式中

图27-5-2 直线振动机二次隔振力学模型
(2)中间基座质量
(3)二次隔振器刚度
为方便起见,选用14只一次隔振器,并对称振动机质心对称布置,所以最后确定的二次隔振器的刚度为
(4)系统的固有频率
x向固有频率:
式中 Sx=K2x/K1x=3.451×106/1.972×106=1.75
y向固有频率:
式中
(5)稳态响应幅值
(6)传给基础的动载荷幅值
垂直向动载荷:
水平向动载荷:
5.3.5 非刚性基座隔振设计
传统振动隔离理论是假设被隔振的机械设备是没有任何弹性的理想质量块;隔振器由无质量的理想弹簧和阻尼器组成;基础是绝对刚性、质量无限大。由此得到只要激励频率比隔振系统固有频率大倍就有隔振效果,且随激励频率增加,隔振效果越好。但是实际上隔振系统隔振效果达不到理论预估的结果,传递率曲线在高频时上翘,而且出现很多共振峰值。其原因是上述的三个假设与实际工程隔振系统有出入,其中基础的非刚性是最主要的影响因素。如安装在楼层上的机械设备,安装在钢质框架上的大型机械设备,基础都是非刚性的。
图27-5-3表示一个非刚性基础的隔振装置简图。这里假定被隔振的机械设备仍是一个理想质量块,而基础有一定的弹性,其阻抗为Z。

图27-5-3 具有任意阻抗Z的非刚性基础的隔振装置
一般采用响应比R作为衡量非刚性基础隔振效果的技术指标,其定义有三个含义:①安装隔振器后基础上方的振动速度与不安装隔振器时基础上方的振动速度之比;②安装隔振器后传给基础的传递力与不安装隔振器时传给基础的传递力之比;③安装隔振器后基础的输出力与不安装隔振器时基础的输出力之比。响应比由下式计算
式中,Mm为机械设备的导纳;MI为隔振器的导纳;M为基础的导纳。
由上式,考虑具有非刚性基础的机械设备隔振系统,为了提高和改善隔振性能,必须增大隔振器的导纳,或减小机械设备和基础的导纳。
5.3.6 隔振设计的几个问题
5.3.6.1 隔振设计步骤
一般机械设备的隔振设计,通常只考虑垂向振动,可按单自由度隔振系统计算,而不必像设计重型机械或精密设备那样按六自由度计算。隔振设计步骤大体相同。
(1)隔振设计前的资料准备
①机械设备的类型、规格及转速范围;
②机械设备的质量、质心位置、安装位置及外形尺寸;
③安装基础的结构特性和环境条件。
(2)激励力分析
首先判断是积极(动力)隔振还是消极(运动)隔振。若是消极隔振,则要分析所在环境的振动优势频率幅值及方向。对于机械设备来讲,绝大多数是属于积极隔振,则要计算分析机械设备最主要的激励力或激励力矩的频率、幅值和方向。
对于往复机械扰动力的估算,可查阅有关手册,旋转机械激励频率一般取旋转机械的最低转速,即
式中 n——旋转机械的最低转速,r/min。
扰动力幅值F0,一般由制造厂提供,或按下式计算
式中 F0——旋转机械扰动力幅值,N;
m0——设备主要旋转部件的质量,kg;
r——旋转部件的偏心距,m。
(3)隔振系统固有频率确定
隔振系统的固有频率应根据设计要求,由所需的振动传递率TA或隔振效率I来确定。各类机械设备的振动传递率推荐值可参考表27-5-4。
(4)隔振基座设计
为了减小被隔离物体的振幅和调整系统质心,通常是将机器安装在一个有足够刚度和质量的钢制或钢筋混凝土制成的隔振基座上,然后再弹性地支承在船舶基础上。对于各种机械设备隔振系统的隔振基座与机械设备质量之比,可采用表27-5-5内的推荐值,安装在楼层上的机械设备,采用推荐值的下限,安装在地面上的机械设备,尽可能取上限。
隔振基座的作用是:
①使隔振元件受力均匀,设备振幅得到控制;
②降低隔振系统质心,提高系统稳定性;
③减少因设备质心位置计算误差引起的耦合振动,使系统尽可能接近只有垂直方向振动;
④抑制机器通过共振转速时的振幅;
⑤作为局部能量吸收器减少噪声对基础直接传递。
表27-5-4 机械设备隔振系统振动传递率的推荐值

表27-5-5 隔振基座与机械设备质量比的推荐值

(5)机器和隔振基座的质量和质心位置确定
对于仅考虑垂向振动的隔振系统,只需要求出机器和隔振基座的全部质量并确定公共质心位置。若要求同时考虑垂向(x向)、纵向(y向)和横向(z向)3个方向直线振动和绕3个方向的回转振动,则需要求出3根主惯性轴位置以及绕该3根轴的惯性矩。通过调整隔振基座的质量分布,尽可能使主惯性轴落在水平面和垂直面内。
(6)机械设备的允许振动和机械设备隔振系统振幅的计算
精密设备和机械设备的允许振动的指标在出厂说明书或技术要求中给出。一般机械设备隔振后允许振动,推荐用10mm/s的振动速度为控制值;对于小型机械设备可用6.3mm/s的振动速度为控制值。振动速度与振动幅值,对于单一频率按下式换算
式中 v0——振动速度幅值,mm/s;
A——振动幅值,mm;
f——激励力频率,Hz。
机械设备隔振系统的振幅A由下式计算
式中 F0——激励力幅值,N;
m——机器和隔振基座总质量,kg。
如果计算的振幅A超过机器设备允许值时,通常采取加大隔振基座的质量,即增加m以减小A值。
(7)隔振器选择和布置
隔振器选择主要考虑刚度和阻尼,耐环境条件的性能。为了安装维护方便,尽可能采用同一种类同一型号的隔振器。
隔振器布置应遵循下列原则:
①在隔振装置中,尽可能选用相同型号的隔振器,并使每个隔振器受力相等,变形一致;
②隔振器尽可能按机械设备的主惯性轴作对称布置,避免产生耦合振动;
③当机械设备的形状和质量分布特殊而不得不采用不同型号的隔振器时,应使隔振器的各个支承点的变形一致,以保证隔振系统在振动时保持垂直方向振动独立;
④为了克服计算误差引起隔振器静态压缩量不一致,可把隔振器安装位置部分设计成为活动的,安装时可以调整,以保证各隔振器静态压缩量一致。
(8)其他部件的柔性连接
隔振系统的所有管道、动力线及仪表导线在隔振基座上、下连接必须是柔性的,以减少振动传递。
5.3.6.2 隔振设计要点
1)隔振系统的固有频率确定应该同时考虑隔振效果和机组的稳定性。在满足隔振效率的前提下,固有频率宜设计得高一些,以增加隔振系统的稳定性。
2)隔振系统的固有频率fn与激励频率f两者比值,原则上应在以下范围: f/fn=2.5~5,当因为激励频率过低无法满足时,可将隔振系统的固有频率fn设计成使频率比为0.4~0.6,这时在该激励频率下的振动放大了20%~50%,主要是隔离高频激励振动。
3)考虑被隔离机械设备质量计算误差和设备运行时动载荷,隔振系统设计时隔振器所承受的载荷一般为其额定载荷的70%~80%。
4)为防止隔振系统摇摆或在启动过程中通过共振区时振幅过大,可考虑安装阻尼器或振幅限位器。
5)高压水泵、空压机、风机等机械设备运行时在出口处由高压头产生的反作用力将作用在设备的基座上,所以在隔振系统设计时,隔振器除承受设备的静载外,需考虑附加的作用力,同时隔振器布置位置按运行状态设定。
6)检验和方案比较,在完成隔振设计后,要检查机械设备隔振系统是否符合设计指标,有时需要作几个不同的方案进行比较以满足经济性要求。
5.3.6.3 隔振系统的阻尼
从振动隔离的绝对传递系数分析阻尼对隔离高频振动是不利的,但在生产实际中,常遇见外界冲击和扰动。为避免弹性支承物体产生大幅度自由振动,人为增加阻尼,抑制振幅,特别是当隔振机械设备在启动和停机过程中需经过共振区时,阻尼作用就更为重要。隔振系统阻尼大,启动和停机时间就短,越过共振区的时间短,共振振幅就小,否则相反。综合考虑,从隔振效果来看,实用最佳阻尼比ζ在0.05~0.2,在此范围内,共振振幅不会很大,隔振效果也不会降低很多。通常采用橡胶隔振器可保证隔振系统的阻尼比大于0.05,当采用金属螺旋弹簧时需要附加阻尼器。
5.3.7 隔振元件材料、类型与选择
5.3.7.1 隔振元件材料、类型
隔振元件是指起支承作用、具有一定刚度和阻尼的弹性件,通常分成隔振垫和隔振器两大类。前者为橡胶隔振垫、海绵橡胶、毛毡、玻璃纤维及矿棉等;后者为金属螺旋弹簧、橡胶隔振器、钢丝绳隔振器、空气弹簧等。
描述隔振元件的静、动态力学性能的主要指标有静刚度、动刚度、阻尼系数以及额定载荷等。隔振元件的静刚度是指在静载荷条件下使隔振元件产生单位变形所需的力;如果载荷是动态的,即频率不等于零,这时的刚度称为动刚度。动刚度一般大于静刚度,而且频率越高,动刚度越大。通过测试隔振元件支承的隔振系统固有频率,按照单自由度系统固有频率ωn计算式,计算得到隔振器的动刚度,即
式中,Kd为隔振器的动刚度;m为系统质量;ωn为系统固有频率。
表27-5-6 隔振元件材料和主要特性

注:▲—优;○—良;△—中;×—差。
由于橡胶材料具有蠕变特性,即在额定负荷下,橡胶隔振元件变形在一段时间内仍不断增加。通常48h的滞后变形可达蠕变的90%,所以对于有对中和外接件要求的机械设备,在设备加载到隔振器上后,必须48h以后再进行对中及外接件的安装,一般机械设备采用橡胶隔振元件,要求24h后再进行外接件的安装。
5.3.7.2 隔振元件选择
隔振元件一般按隔振系统固有频率进行选择。
当固有频率f0≥20~30Hz,可选用毛毡、橡胶隔振垫及刚度大的橡胶隔振器、金属丝网隔振器。
当固有频率f0=2~10Hz,可选用金属弹簧、钢丝绳隔振器、橡胶隔振器、海绵橡胶及泡沫塑料等。
当固有频率f0=0.5~2Hz,可选用空气弹簧隔振器。
隔振元件选择另一个要点是载荷,一般应该使隔振元件所受到的静载荷为允许载荷的80%~90%,动载荷与静载荷之和不超过其最大允许载荷,对于隔振垫,允许载荷或推荐载荷是指单位面积的载荷,并力求各个隔振元件载荷均匀。
表27-5-7 常用隔振器特性和应用场合

5.3.8 橡胶隔振器
橡胶隔振器是机械设备隔振最常用的隔振器,其结构形式可以分为压缩型、剪切型、压缩-剪切混合型和组合型。压缩型橡胶隔振器承载能力大,固有频率高(15~30Hz);剪切型橡胶隔振器承载能力较压缩型小,固有频率低(5~10Hz);混合型兼有两者特点;组合型具有体积小、三向刚度相同的优点。橡胶隔振器的主要特点如下。
1)橡胶隔振器不仅在轴向,而且在横向和回转方向均具有隔离振动的性能,同一个橡胶隔振器,在三向刚度上,有很宽的选择余地。
2)作为机械设备的隔振器,具有重量轻、体积小的特点,橡胶容易与金属粘接,强度高,容易实现多个组合,每单位体积的橡胶,其能量吸收是弹性钢的两倍。
3)具有振动阻尼性能,橡胶内部阻尼比金属大。
4)可以隔离高频振动,隔声效果好。
5)设计合理时,可把载荷-变形曲线设计成非线性,如渐软特性和渐硬特性。
6)橡胶隔振器的缺点是,刚度不可能设计得很小,其固有频率下限约为4~6Hz,大于金属弹簧和空气弹簧;耐高温,耐低温性能差;有蠕变;在空气中容易老化等。
5.3.9 橡胶隔振器设计
5.3.9.1 橡胶材料的主要性能参数
橡胶可以分为天然胶和合成胶两大类。天然胶综合的物理力学性能好,缺点是耐油性及耐热性差。合成胶能满足某些特殊的要求,价格较便宜。通常用作隔振材料的合成胶料有丁腈胶、氯丁胶和丁基胶。丁腈胶主要优点是耐油性好,常作为一般动力机械设备的隔振器材料;氯丁胶主要优点是耐候性好,常用于对耐老化、抗臭氧要求高的环境,缺点是易发热;丁基胶主要优点是阻尼大、耐候性好,缺点是与金属粘接较困难。
表27-5-8 橡胶材料的主要性能参数



图27-5-4 橡胶弹性模量和硬度间的关系曲线
5.3.9.2 橡胶隔振器刚度计算
表27-5-9 橡胶隔振器的刚度计算



注:1.表中的E、G为橡胶材料的静态弹性模量,计算所得刚度为静刚度,乘上动态系数d为动刚度。 2.表中计算的刚度为20℃下的刚度,当环境温度偏差大时,应用温度影响系数修正。 3.静刚度设计时,有三个独立尺寸,可先假设两个尺寸,求出第三个尺寸,然后计算刚度,若不满足设计要求,应重新假定尺寸,再进行计算,直至满足设计要求。
5.3.9.3 橡胶隔振器设计要点
1)应根据使用环境和条件,选用合适的橡胶。
2)注意橡胶与金属的粘接强度,避免有可能造成应力集中的结构,如采用圆角代替锐角。
3)通常橡胶隔振器的最大应力发生在橡胶与金属的粘接面上,因此在强度校核时,除了橡胶本身的许用应力外,必须考虑橡胶与金属间的粘接强度,取两者中的较小值作为设计的依据。
4)隔振器应避免长期在受拉状态下工作,橡胶的变形应按厚度控制在许可的百分比范围内。
5)对于圆筒形或剪切变形隔振器,为了消除橡胶的收缩应力,提高其耐久性,制造时在垂直剪切方向给予适当预压缩,这样压缩方向刚度变硬,剪切方向刚度变软,因此刚度的正确数值,要按产品实测为准。
6)由于有阻尼就要消耗能量,这部分损失的能量转换成热能,而橡胶是热的不良导体,为防止温升过高影响橡胶隔振器性能,第一,橡胶隔振器不宜做得过大,其次,从结构上应采取易于散热的措施,或选用生热较少的天然橡胶材料。
5.3.10 钢丝绳隔振器
5.3.10.1 主要特点

图27-5-5 典型钢丝绳隔振器结构
钢丝绳隔振器是用钢丝绳绕制而成的,将钢丝绳绕成弹簧状,固定在沿弹簧母线布置的两块金属板之间,典型结构见图27-5-5。钢丝绳隔振器的特性由钢丝绳的直径、每匝中钢丝的数目、钢丝绳的长度和扭绞角度以及隔振器中的钢丝绳匝数而定。它广泛用于宇航、飞机、车辆、导弹、卫星、运载工具、舰船电器、舰用照明灯具及仪表仪器、海洋平台、高层建筑、核工业装置以及工业各类动力机械的隔振防冲。其主要特点如下。
1)金属材料制成,抗疲劳、耐辐射、耐高低温、耐油、抗臭氧、抗盐雾和水分的腐蚀,能长时间在振动状态下工作,寿命长、耐老化,可与被隔振设备同寿命。
2)承载范围宽(覆盖从1~50000N的静载荷),具有非线性软刚度特性,波动效应不明显,具有较好的隔离高频振动效果。
3)变阻尼特性当外界激励频率变化时减振器的阻尼也随之发生变化。共振点阻尼比达0.15以上,有效地抑制共振峰,越过共振点后,阻尼迅速减小,从而具有良好的隔振效果。
4)钢丝之间有相当大的自由行程,相互之间的干摩擦使其具有较大的非线性阻尼,动力学性能尤其是冲击隔离性能较其他金属隔振器好,具有较好的隔冲效果。
5.3.10.2 选型原则与方法
1)在保证机械设备隔振系统稳定性前提下,尽量降低隔振系统动刚度,增大动变形空间。
2)机械设备隔振系统各个钢丝绳隔振器的安装位置尽可能使隔振系统的刚度中心与质量中心重合,有利于消除振动耦合。
3)隔振系统的技术条件,如在什么样的环境中使用以及它的振动频率、冲击频率,保证系统最大冲击输入能量和冲击力不大于钢丝绳隔振器许可值,并在设计隔振系统时使钢丝绳隔振器承受载荷为额定值的70%~80%,增加安全系数,使其既抗冲击又能隔离振动。
4)当隔振设备高宽(或深)之比大于1时,应考虑增设稳定用隔振器。
5.4 阻尼减振
现实的工程结构多为复杂的多自由度系统,且常处于宽频带随机激励的振动环境,其振动响应往往是很复杂的,单一的隔振技术难以满足振动控制的要求,还必须采用各种形式的阻尼,耗散振动体的能量,达到减小振动的目的。阻尼是指任何振动系统在振动中,由于外界作用和/或系统本身固有的原因引起的振动幅度逐渐下降的特性,以及此特性的量化表征。常用的人工阻尼技术包括阻尼结构、阻尼减振器,后者包括黏弹性阻尼、干摩擦(库仑)、流体阻尼及其他形式几种。阻尼的作用主要有以下几点。
1)阻尼有助于降低机械结构的共振振幅,从而避免结构因动应力达到极限所造成的破坏,增大阻尼是抑制结构共振响应的重要途径。
2)阻尼有助于机械系统受到瞬态冲击后,很快恢复到稳定状态。结构受瞬态激励后产生自由振动时,要使振动水平迅速下降,必须提高结构的阻尼比。
3)阻尼有助于减少因机械振动所产生的声辐射,降低机械噪声。
4)可以提高各类机床、仪器等的加工精度、测量精度和工作精度。
5)阻尼有助于降低结构传递振动的能力。
5.4.1 阻尼减振原理
阻尼是指系统损耗能量的能力。从减振的角度看,就是将机械振动的能量转变成热能或其他可以损耗的能量,从而达到减振的目的。对于振动阻尼产生的机理按物理现象的不同通常可分为五类。
1)材料的内摩擦,由材料内部分子或金属晶格间在运动中相互摩擦而损耗能量所产生的阻尼作用,又称之为材料阻尼。
2)摩擦,摩擦耗损振动能分为两个接合面间相对运动的摩擦和利用介质的摩擦耗能。
3)能量的传输,当机械振动能量从结构向外传输与能量耗损转变为热能有同样的减振作用。
4)电能与机械能的转换效应,通过把机械振动能转换为电能,再由电磁效应的磁滞损失耗散能量或由涡流的能量损失产生阻尼作用。
5)频率变换,当从原频率转换为另一种频率时,那么对机械产生的振动危害有可能被减弱,而且这种振动能量不再对原有频率有效,并且在频率转换之后能更易转变为热能。
5.4.2 阻尼类型
(1)材料阻尼
工程材料种类繁多,衡量其内阻尼的指标通常用损耗因子。通常金属材料的损耗因子很小,阻尼值低,阻尼合金的阻尼值比金属材料高出二至三个数量级,阻尼材料阻尼值高。
表27-5-10 常用阻尼材料分类表

(2)黏性阻尼
黏性阻尼的阻尼力与振动速度成正比,常用在机械振动系统的建模和计算。
(3)结构阻尼
结构阻尼是系统振动时材料内摩擦产生的阻尼,在一个周期中它耗散的能量与频率无关,而与振幅的平方成正比,亦称为迟滞阻尼。结构阻尼力的大小与位移成正比,其方向与速度方向相反。
(4)流体阻尼
物体在流体中运动受到的阻力与运动速度的平方成正比,又称速度平方阻尼。
(5)接合面阻尼与库仑摩擦阻尼
机械结构的两个零件表面接触并承受动态载荷时,能够产生接合面阻尼或库仑摩擦阻尼。接合面阻尼是由微观的变形产生,而库仑摩擦阻尼则由接合面之间相对宏观运动的干摩擦耗能所产生,通常库仑摩擦阻尼比接合面阻尼大一到两个数量级。
(6)冲击阻尼
冲击阻尼是一种结构耗能,工程中可通过设置冲击阻尼器来获得冲击阻尼,例如,砂、细石、铅丸或其他金属块,以致硬质合金都可以用作冲击块,以获得冲击阻尼。
(7)磁电效应阻尼
机械能转变为电能的过程中,由磁电效应产生涡流阻尼,涡流阻尼的能量损耗由电磁的磁滞损失和涡流通过电阻的能量损失组成。
5.4.3 材料的损耗因子与阻尼结构
5.4.3.1 材料的损耗因子
材料的损耗因子β是衡量其吸收振动能量的特征量,当材料受到振动激励时,损耗能量与振动能量之比为损耗因子
式中 Wd——一个周期中阻尼所消耗的功;
U——系统的最大弹性势能,;
K——系统刚度;
A——振幅。
常用工程材料的损耗因子见表27-5-11。
5.4.3.2 阻尼结构
为了增加结构阻尼,常常采用黏弹阻尼材料与金属或非金属结构构成复合阻尼结构,其结构损耗因子可以达到0.1~0.5,可以有效地抑制结构的谐振响应。
表27-5-11 常用工程材料的损耗因子β

典型的阻尼结构一般有两种形式。
(1)自由阻尼层结构
自由阻尼层结构是直接将黏弹性阻尼材料粘贴或者喷涂在需要减振的结构元件的表面上,见图27-5-6。当原结构件振动发生弯曲变形时,阻尼层以拉压变形的方式与构件的变形相协调,从而将机械振动能转变为热能耗散掉,达到阻尼减振的目的。自由阻尼层的阻尼效果,在附加质量为20%~30%的情况下,结构损耗因子可达到0.05~0. 2。自由阻尼层结构的优点是工艺简单、设计方便、费用低、容易实施等,但是在低频时阻尼减振效果较差。

图27-5-6 自由阻尼层结构
自由阻尼层结构组合梁的损耗因子与结构参数的关系式
式中,h为阻尼层厚度H2与结构层厚度H1之比,h=H2/H1;e为阻尼层杨氏模量与结构层杨氏模量之比值,e=E2/E1;β为阻尼材料的损耗因子;η为组合梁结构的损耗因子。
(2)约束阻尼层结构
约束阻尼层结构由原结构件、阻尼材料层和弹性材料层(称约束层)构成,见图27-5-7。当原结构件产生弯曲振动时,阻尼层上下表面各自产生压缩和拉伸变形,使阻尼层受剪切应力和应变,从而耗散结构的振动能量。弯曲变形时,由于约束层的作用使阻尼层产生较大的剪切变形可耗散较多的机械能,其减振效果比自由阻尼层结构大。约束阻尼层结构可分为对称型、非对称型和多层结构。用两种以上的阻尼材料构成多层结构,可提高阻尼性能。由于多层结构同时使用不同的玻璃态转变温度和模量的阻尼材料,这样可加宽温度带宽和频率带宽。

图27-5-7 约束阻尼层结构
约束阻尼结构梁的损耗因子
式中,β为阻尼材料的损耗因子;η为约束阻尼结构的损耗因子;X为剪切参数;Y为刚度参数。X的表达式为
式中,G2为阻尼层材料模量的实部;b为约束阻尼梁的宽度;k为约束阻尼梁弯曲振动的波数,;D为组合梁的弯曲刚度,
;H1,H2和 H3分别为原结构层、阻尼层和约束层的厚度;K1和K3分别为原结构层和约束层的刚度;E1和E3分别为原结构层和约束层梁的杨氏弹性模量。
刚度参数Y的表达式为
式中,H31是原结构层中性面至约束层中性面的距离,。
图27-5-8给出典型的约束阻尼结构横截面。图27-5-9为典型的外体-嵌入体-黏弹性材料组成的梁的横截面。
阻尼处理位置对于减振性能影响显著,有时在结构的全面积上进行阻尼处理可能会造成浪费,而实际工程结构通常也只能进行局部阻尼处理。如何使局部阻尼处理达到最佳的阻尼效果是阻尼处理位置的优化问题,可以根据不同阻尼结构的阻尼机理,相应地进行优化处理,以达到最佳的性能价格比。

图27-5-8 典型的约束阻尼层结构横截面

图27-5-9 外体-嵌入体-黏弹性材料组成的梁的横截面
5.4.4 干摩擦阻尼
5.4.4.1 刚性连接的干摩擦阻尼
表27-5-12 刚性连接的干摩擦阻尼


5.4.4.2 弹性连接的干摩擦阻尼
表27-5-13 弹性连接的干摩擦阻尼


图27-5-10 非线性干摩擦阻尼减振器
1—底座;2—外壳;3—减振弹簧;4—干摩擦阻尼器;5—摩擦顶盖;6—摩擦棒;7—摩擦板;8—顶紧弹簧;9—螺杆;10—摩擦棒孔;11—摩擦棒通孔;12—散热翅片
5.4.5 干摩擦阻尼减振器
摩擦阻尼器结构特征,一是选用合适的摩擦材料做摩擦片,二是对摩擦片施加足够的摩擦力,通常施加正压力方法有预压弹簧、气缸或油缸三种加压形式。图27-5-10为非线性干摩擦阻尼减振器(专利),该阻尼减振器结构概述如下:摩擦顶盖5内开有摩擦棒孔10,外壳2的上部壳壁上开有摩擦棒通孔口,摩擦顶盖5的下端设置在减振弹簧3的上端,顶紧弹簧8设置在摩擦棒孔10的里端,摩擦棒6的杆端设在摩擦棒孔10内顶紧弹簧8的外端,摩擦棒6的摩擦端设在外壳2上的摩擦棒通孔11内,外壳2上摩擦棒通孔11的外壁上由螺杆9固定有摩擦板7,摩擦棒6摩擦端的外端面与摩擦板7的内壁之间摩擦接触。减振原理是将振动能量转化为摩擦功,据称比常规阻尼减振器增大吸振能量二倍以上。摩擦棒及摩擦板可方便更换,大大提高了应用效果。据称寿命比常规橡胶阻尼减振器长三倍,比金属网阻尼减振器长二倍。
5.5 动力吸振器
利用附加的弹性元件、阻尼元件和辅助质量连接在主振动系统所产生的动力作用来减小主系统振动的方法称为动力吸振。该弹性元件、阻尼元件和辅助质量所构成的附加系统称为动力吸振器。
5.5.1 动力吸振器设计
5.5.1.1 动力吸振器工作原理
表27-5-14 动力吸振器工作原理


5.5.1.2 动力吸振器设计
表27-5-15 动力吸振器设计步骤

5.5.1.3 动力吸振器设计示例
表27-5-16 动力吸振器设计示例

5.5.2 有阻尼动力吸振器
5.5.2.1 有阻尼动力吸振器的动态特性
表27-5-17 有阻尼动力吸振器的动态特性


5.5.2.2 有阻尼动力吸振器的最佳参数
表27-5-18 采用优化准则1,有阻尼动力吸振器最佳参数


表27-5-19 采用优化准则2,有阻尼动力吸振器最佳参数


表27-5-20 采用优化准则3,有阻尼动力吸振器最佳参数

表27-5-21 采用优化准则4,有阻尼动力吸振器最佳参数


表27-5-22 采用优化准则5,有阻尼动力吸振器最佳参数

续表

表27-5-23 采用优化准则6,有阻尼动力吸振器最佳参数


表27-5-24 采用优化准则7,有阻尼动力吸振器最佳参数

表27-5-25 采用优化准则8,有阻尼动力吸振器最佳参数

表27-5-26 采用优化准则9,有阻尼动力吸振器最佳参数


表27-5-27 采用优化准则10,有阻尼动力吸振器最佳参数

5.5.2.3 有阻尼动力吸振器设计示例
表27-5-28 有阻尼动力吸振器设计示例

5.6 缓冲器设计
5.6.1 设计思想
隔振系统所受的激励是振动,缓冲系统所受的激励是冲击,所以缓冲问题与隔振减振问题有所不同。隔振主要处理的是稳态的振动,振幅较小;缓冲则主要处理瞬态振动,振幅较大。由于振幅大,有时就必须考虑非线性问题。隔振器的设计,主要是寻求激振圆频率和系统固有圆频率间的关系,使传递系数控制在允许范围内。缓冲的主要问题是要求所设计的缓冲器能够储存冲击作用的能量,冲击结束后将此能量以系统作自由衰减振动的形式释放出来,使冲击波以较缓和的形式作用于基础和设备。隔振器与缓冲器都是要阻止或减少振动能量的危害,其基本理论是相同的,甚至有些设备都是相似的,例如车辆的缓冲器往往就被通俗地称作隔振器。
5.6.1.1 冲击现象及冲击传递系数
冲击是指一个系统在相当短的时间内(通常以毫秒计),受到瞬态激励,其位移、速度或加速度发生突然变化的物理现象。冲击特点:①冲击作用的持续时间非常短暂,因此剧烈的能量释放、转换和传递的时间很短,是骤然完成的。②冲击激励函数不呈现周期性。在冲击作用下,系统所产生的运动为瞬态运动,而振动激励函数一般都是周期性的,系统运动响应为稳态振动。③在冲击作用下,系统的运动响应与冲击作用的持续时间及系统的固有频率或周期有关。④冲击作用下系统的响应(位移、速度或加速度)在冲击持续时间内与冲击作用结束后是不同的。前者称作初始响应,后者称作残余响应。
图27-5-11是5种常见的冲击运动的加速度、速度和位移曲线。其中加速度脉冲和阶跃加速度是冲击运动的极限情况,是一种较为特殊的冲击脉冲或持续载荷。载荷持续的量级可以瞬时达到或经过有限时间达到。持续载荷之所以归入冲击环境,是由于激励力或加速度从参考幅值变到最大持续力幅值或加速度幅值是以突然加载的方式进行的。半正弦脉冲加速度、衰减正弦加速度和复杂振荡型运动是工程中常遇到的冲击输入。半正弦冲击输入和矩形脉冲输入等都可以由二个符号相反、时间延迟为脉冲宽度的阶跃信号叠加而成。

图27-5-11 常见的冲击运动的加速度、速度和位移曲线
缓冲问题是冲击隔离问题,因此,同隔振一样,可将缓冲分为积极缓冲和消极缓冲两类,缓冲系统的力学模型见图27-5-12,在忽略阻尼和非线性影响以及冲击作用时间的条件下,可以得到两个数学意义相同的运动方程。

图27-5-12 缓冲系统的力学模型
积极缓冲时
式中 Fm——冲击力最大值。
消极缓冲时
式中 ——基础加速度冲击最大值。
评价缓冲器品质的重要指标是冲击传递系数。被缓冲器保护的基础或机械设备所受的最大冲击力为Nm,无缓冲器时基础或机械设备所受的最大冲击力为Nm∞,则冲击传递系数Ts:
积极缓冲时
消极缓冲时
从力学模型、运动微分方程和传递系数上看,缓冲和隔振非常相似。因此,缓冲问题也同隔振问题一样,从消极缓冲模型动力分析中所得出的结论会完全适用于积极缓冲。
5.6.1.2 速度阶跃激励
当冲击力作用的时间τ远小于缓冲系统固有周期T(一般τ<0.3T)时,根据冲量定理,该力的冲击与此力的冲量所产生速度阶跃相同。同理,当加速度脉冲的持续时间τ远小于缓冲系统固有周期T时,也可将加速度脉冲近似地作为速度阶跃冲击。于是系统的运动方程和初始条件为:
式中 ——缓冲器的恢复力和阻尼力函数。
由于缓冲器的固有圆频率一般都比较低,即固有周期T比较长,所以冲击作用时间一般要比T小得多,采用速度阶跃模型所得到的结果可满足工程计算要求。
5.6.1.3 缓冲弹簧的储能特性
表27-5-29 缓冲弹簧的储能特性



图27-5-13 硬特性弹簧、
与
的关系曲线

图27-5-14 软特性弹簧的关系曲线
5.6.1.4 阻尼参数选择
理论分析结果表明:
1)当时,
, 从表27-5-29 查得线性弹簧无阻尼时的最大加速度
,
,说明阻尼的存在使最大加速减小,改善了缓冲效果,ξ>0.5则相反;
2)当确定时,
在ζ=0.265时取最小值,
,所以,
为弹簧刚度固定时的最佳阻尼比;
3)当、δm确定时,
在
时取最小值,
,所以,
为弹簧的最大变形量固定时的最佳阻尼。
5.6.2 一级缓冲器设计
5.6.2.1 缓冲器设计原则
1)由冲击激励性质分析,确定计算模型。冲击激励一般可以表达为力脉冲、加速度脉冲或速度阶跃。由于缓冲系统的固有振动周期比较长,而冲击的作用时间比较短,所以各种冲击作用一般可以简化为速度阶跃这一较理想的冲击模型,而不致有大的误差。这一模型可使设计计算简化,且偏保守。当需要用力脉冲或加速度脉冲作为冲击输入时,常见的各种形状的脉冲可以简化为等效的矩形脉冲,所得结果能满足工程的精度要求。
2)根据缓冲要求,确定缓冲器设计控制量,即缓冲器的最大压缩量δm,所保护的对象受到的最大力Fm或最大加速度。
3)分析缓冲器的工作环境,看是否有隔振要求。若要求隔振,则设计就变得复杂。隔振器和缓冲器的设计侧重点不尽相同,应采用前述相应章节分析,进行综合设计。
4)阻尼的处理是缓冲器设计中的一个重要问题。阻尼的作用是耗散部分冲击能,从而减小冲击力。设计时,一般取相对黏性阻尼系数为0.3,如果阻尼太大(如>0.5),反而使受保护设备所受的冲击增大。
5)根据缓冲对象及缓冲器工作空间环境要求,确定在所设计的缓冲器中是否需加限位器。
6)无论哪种缓冲器或减振器设计说明中都应标明其缓冲特性,并要求作特性的实测及调整记录。
5.6.2.2 设计要求
积极缓冲:在已知机械设备质量m、最大冲击力Fm和作用时间τ (已知)的条件下,要求通过缓冲器传给基础的最大冲击力Nm、作用基础的最大冲量和缓冲器的最大变形量δm小于许用值。
被动缓冲:在已知机械设备质量m、最大冲击加速度和持续时间τ (已知
)的条件下,要求通过缓冲器传递到机械设备最大冲击加速度
,最大冲量和缓冲器的最大变形量δm小于许用值。
5.6.2.3 一次缓冲器动力参数设计
如果再已知最大允许加速度和最大允许变形δm,可求缓冲弹簧的参数(线性弹簧K;硬特性弹簧K、d;软特性弹簧K、d1)。
线性弹簧:由,求出
的最大允许值,再由
,求出
的最小允许值,然后再在ωn的最大允许值和最小允许值之间找到合适的值。由ωn值求K值。
硬特性弹簧:值在图27-5-13(a)的曲线上查得
值,再在图27-5-13(b)中查得ωn值,由ωn值求K值。
软特性弹簧:根据值在图27-5-14(a)的曲线上查得
值,再在图27-5-14(b)中查得ωn值,由ωn值求K值。
线性弹簧黏性阻尼可依照5.6.1.4节的方法,在弹簧刚度固定时,选取,在最大变形固定条件下选
。阻尼比ζ若稍有变化对冲击传递系数影响不是很显著,但对限制最大变形量δm是很有益的。
5.6.2.4 加速度脉冲激励波形影响提示
当加速度脉冲的持续时间(或冲击力作用时间)
时,再用速度阶跃激励则过于保守。甚至会得出完全错误的结果,需参考有关文献,考虑加速度脉冲形状对缓冲的影响。
5.6.3 二级缓冲器设计
表27-5-30 二级缓冲器设计

5.7 机械振动的主动控制
5.7.1 主动控制系统的原理
主动控制是指通过作动器对被控对象施加作用力来实现振动抑制的一类控制方法。主动控制系统构成如图27-5-15所示,对于开环控制,控制器根据预先设计的控制律向作动器发出控制指令,作动器将接收到的指令转化为控制力或力矩,施加于被控对象,达到抑制振动的目的;对于闭环控制,控制器接收由测量系统传来的被控对象的振动信息,按照预设的或在线调整的控制律将其转化为控制信号,并输出至作动器,作动器将接收到的指令转化为控制力或者力矩后,施加于被控对象,实现期望的振动控制性能。

图27-5-15 主动控制系统构成
5.7.2 主动控制的类型
按照控制原理分类,主动控制可分为开环控制和闭环控制两类。

图27-5-16 闭环控制原理
(1)开环控制
开环控制原理如图27-5-15(a)所示,控制器根据预先设计好的控制律实施控制。这种方法不考虑被控对象的实时运动状态,当外界干扰不可忽略或者被控对象参数可变时,具有明显的局限性。虽然开环控制具有简单经济的优点,它只适用于被控对象具有确定的输入输出关系的情况。
(2)闭环控制
①反馈控制 反馈控制原理如图27-5-16(a)所示,反馈控制适用于被控对象存在外扰、参数不确定或可变的情况。反馈常以两种方式应用于结构的振动控制:主动阻尼和基于模型的反馈。前者用于抑制共振峰,后者使给定控制变量趋于期望值,主要包括LQG、极点配置法(特征结构配置法)、H∞ 控制方法等。
②前馈控制 前馈控制原理如图27-5-16(b)所示,需要使用与干扰信号相关的参考信号。如果能够获得强相关参考信号,前馈控制就能够取得较反馈控制更好的控制性能。与主动阻尼相比,前馈控制可以控制任意选定的频带内的振动。关于前馈和反馈控制的比较见表27-5-31。
5.7.3 控制系统的组成
除被控对象外,主动控制系统还包括以下环节。
1) 作动器 根据控制信号产生控制力或力矩,并将控制力/力矩作用于被控对象的装置,是联系控制器与被控对象的纽带。作动器按其工作原理主要分为两类,一类是基于机械原理实现致动的作动器,例如气动、液压、电磁作动器等;另一类是基于材料机敏性实现致动的作动器,例如压电材料、磁致伸缩材料、磁流变体作动器等。
2) 测量系统 由传感器、适调器、放大器以及滤波器等组成,目的是拾取被控对象的运动状态,并将其转化为适于传送和处理的信号。
3) 控制器 通过模拟电路/模拟计算机或者数字计算机实现控制律的硬件或者软件,将测量系统传送过来的振动信息(对于闭环)或将预先设定好的程序(对于开环)转变为控制信号,该信号作为作动器的动作指令,驱动作动器。
4) 能源 包括电源、气源、液压油源等能够维持系统工作的外界能量。
表27-5-31 前馈控制和反馈控制的对比

5.7.4 作动器类型
(1)气动/液压作动器
气动和液压作动器的工作原理相似,也分别称为工作介质受伺服控制的空气弹簧和液压缸,利用气/液体传动进行工作。这两种作动器适用于低频、控制力较大、对时滞和控制精度要求不高的场合,都需要较复杂的辅助系统。气动作动器质量轻,但是工作介质易压缩,控制带宽较低(小于10Hz),主要应用于低频主动悬置。液压作动器的工作介质是液压油,工作介质可压缩性对动态性能的影响较小,常用于重型设备振动的主动控制。
(2)电磁作动器
电磁作动器通常包含线圈和恒定磁场,当位于磁场中的线圈通过交变电流时,形成的交变电磁力将驱动线圈运动,输出控制力。电磁作动器具有频率范围宽、响应快、控制力大等优点。电磁作动器在宽频带内的输入输出特性呈线性关系,结构紧凑,易于安装,输出力与体积、质量的比值较大。
根据运动部件的不同,电磁作动器可分为动圈式和动铁式两种类型。
动圈式:动线圈通交变电流后,在永久磁场中受到周期变化的电磁激励力作用,带动与之相连接的机械部件作往复运动,如图27-5-17所示,实现振动控制。

图27-5-17 电磁作动器
动铁式:由带有线圈的电磁铁铁芯和衔铁组成,衔铁直接固定于需要控制的机械部件上。在励磁电流(直流电流)作用下,铁芯和衔铁间建立了恒定磁场;当控制电流(交流电流)通过交流线圈,衔铁受到交变磁场的作用,产生交变的控制力。
(3)压电材料作动器
压电材料作动器利用逆压电效应,即在压电晶体上施加交变电场,使压电晶体产生交变的机械应变。压电材料作动器分为薄膜型和叠堆型,在主动隔振中主要应用叠堆型作动器,如图27-5-18所示,以保证控制力。压电材料作动器除位移较小外,突出优点是重量轻、机电转换效率高、响应速度快。

图27-5-18 压电叠堆型作动器
(4)磁致伸缩作动器
磁致伸缩材料也属于机敏材料,利用这种材料制成的磁致伸缩作动器具有伸缩应变大、机电耦合系数高、响应快、输出力大、工作频带宽、驱动电压低等特点,因而适于多种场合的主动隔振。磁致伸缩材料抗压能力较强,但是抗剪切和抗拉伸能力较差,所以在设计作动器时需要保证其始终处于受压状态。同时,作动器存在迟滞现象,其输入和输出之间有较强的非线性,因而对控制方法要求较高。
(5)磁流变流体作动器
磁流变流体作动器使用磁流变液,磁流变液是由磁化的微米粒子悬浮在合适的母液当中形成的,在正常状态下可以流动。加入磁场后,液体中的可磁化粒子排列成链状结构,排列方向与磁力线方向一致,如图27-5-19所示。这种能固化的磁浮粒子限制流体流动,从而使流体产生一定的屈服强度。磁流变液的响应速度快,状态可逆、连续可变。

图27-5-19 磁流变液与磁流变流体作动器
5.7.5 主动控制系统的设计过程
振动主动控制系统的设计过程大体分为以下几个步骤(图27-5-20):
①分析被控对象,确定动态特性、干扰和响应的类型;
②采用理论分析、实验建模等方法获得被控对象的数学模型;
③如有必要,进行模型缩减,以便于控制器设计和分析;
④量化传感器和作动器要求,确定传感器和作动器的类型及安装位置;
⑤分析传感器和作动器对控制系统动态特性的影响;
⑥在性能指标和稳定性之间作出平衡;
⑦确定控制策略,并据此设计控制器;
⑧用模型进行仿真,评估控制方法满足控制要求的潜力;
⑨如果控制器不能满足指标要求,调整控制器参数或者更换其他类型的控制器;
⑩选用硬件和软件,并将它们集成为一个实验系统;
设计实验进行系统辨识和模型更新;
进行控制和系统测试,评估整体性能;
如有必要重复以上过程。

图27-5-20 主动控制系统设计流程图
5.7.6 常用的控制律设计方法
为达到控制效果,需要综合根据被控对象、控制环境、控制目标等因素来选择和设计控制律。控制律的设计方法包括时域设计法、频域设计法和时频域联合设计法。时域设计法主要包括最优控制、极点配置(特征结构配置)、独立模态控制、自适应控制、智能控制等;频域设计法主要是基于频响函数的设计法;时域频率联合设计法,如基于H2、H∞范数优化的鲁棒控制,兼顾时域和频域设计的优点。
(1)最优控制
最优控制方法是一种利用极值原理、最优滤波或动态规划等最优方法来求解结构振动最优控制的设计方法。通常采用被控对象的状态响应和控制输入的二次型
作为性能指标,用于同时保证被控对象的动态特性和控制经济性,导出使泛函J取极值并满足状态方程的控制向量U。在工程实际中,大多采用LQG(linear quadratic gaussian)控制。
(2)极点配置(特征结构配置)
极点配置法包括特征值和特征向量配置,它根据对被控对象的动态品质要求,确定系统的特征值与特征向量,通过状态反馈或输出反馈来改变极点位置,保证闭环系统的极点比开环系统的极点更加靠近需要的极点位置。但是,极点配置在工程实际中很难调整到合适的位置。
(3)独立模态控制
基本思想是将振动方程从物理坐标系通过线性变换转到模态坐标系,在模态空间进行解耦与控制,通过模态控制实现结构的振动控制。这种方法需要进行模态截断,从而产生没有控制的剩余模态。基于模态缩减的控制器可能破坏剩余模态的稳定性,为避免剩余模态的溢出现象,需要尽量将传感器、作动器布置在剩余模态振型的节点上。
(4)自适应控制
自适应控制常用来控制参数未知、不确定或缓变的系统,主要分为三类:①使被控对象与参考模型之间的误差最小的模型参考自适应控制;②以参数辨识为基础,利用特征结构配置或最优控制策略实现控制器设计的自校正控制;③基于跟踪滤波的前馈控制。
基于跟踪滤波的前馈控制实质是振动的主动对消,即与被控振动量有强相关性的参考信号通过自适应控制器,输出能够抵消被控振动量的控制信号。自适应控制器一般采用FxLMS原理,根据系统和环境的变化调整自身参数,以期始终保持系统的性能指标为最优。
(5)智能控制
智能控制主要包括神经网络控制和模糊控制。神经网络具有强大的非线性映射能力和并行处理能力,BP算法、遗传算法常用于神经网络的结构设计、学习和分析。模糊控制理论作为一种处理不精确或者模糊语言信息的方法发展起来,要求在预先选择模糊集数目和模糊逻辑的基础上进行控制,模糊集数目和模糊逻辑的确定性限制了模糊理论在可变外界激励下柔性结构的主动控制方面的应用。
(6)鲁棒控制
鲁棒控制致力于在被控对象模型和外部干扰不确定的情况下寻求控制性能和稳定性之间的折中和平衡,这些不确定性包括参数误差、模型阶数误差以及被忽略的扰动和非线性。鲁棒控制的价值在于设计出不依赖于这些不确定性控制器,使得闭环系统的稳定性和控制性能具有一定的抗干扰能力。H∞控制理论和μ控制理论是目前比较成熟的鲁棒控制理论。H∞控制通常只能在稳定鲁棒性与性能鲁棒性之间达成妥协,μ方法可以保证系统在模型摄动下具有稳定鲁棒性与性能鲁棒性。
5.7.7 主动抑振
主动抑振是在被控对象上布置作动装置,作动器根据被控对象的振动施加主动控制力或力矩,作用于被控对象,以抑制被控对象振动的控制方法。主动抑振按被控对象的振动响应特征可分为随机振动控制和谐波振动控制。
5.7.7.1 随机振动控制
若系统受随机干扰或处于扰动因素较多且不可检测的情况,宜采用反馈控制方式抑制振动。随机振动控制多采用速度反馈(主动阻尼),根据被控对象的振动速度计算控制力,即为控制增益,
为振动速度。这种控制方法主要用于抑制被控对象的固有振动响应,如图27-5-21(a)所示。

图27-5-21 随机振动与谐波振动的控制
5.7.7.2 谐波振动控制
若被控对象的振动表现为周期振动,从被控对象的振动信号提取主要的谐波分量,通过自适应控制等方法生成谐波控制力,抵消被控对象的谐波振动,实现振动控制。图27-5-21 (b)中的PZT作动层可产生与旋转激励相关的作用力,增大黏弹性层的耗散作用,抑制弹性板的周期振动。
5.7.8 主动吸振
主动吸振通过控制力改变吸振器的等效质量、刚度或阻尼参数,或按照一定规律直接驱动吸振器运动,使被控对象的振动转移到吸振器上,实现被控对象自身振动的消减。根据所改变的吸振器动力参数,主动吸振可分为惯性可调动力吸振和刚度可调动力吸振;根据吸振器固有频率是否随外界激励频率变化,主动吸振可分为频率可调式吸振和频率不可调式吸振。
5.7.8.1 惯性可调动力吸振
惯性可调动力吸振包括质量可调式和转动惯量可调式吸振。在图27-5-22(a)所示的质量可调式动力吸振中,控制力使作动器附加质量2m处于水平和垂直两个位置,附加质量在水平位置和垂直位置之间转动,系统频率也随着等效质量的变化而变化,变化范围是

图27-5-22 主动吸振
5.7.8.2 刚度可调式动力吸振
振动频率、振幅与刚度有直接关系,所以刚度可调动力吸振在主动吸振中应用较广。在图27-5-22(b)中,步进电机在控制信号驱动下,带动丝杠转动,使螺母间距发生变化,改变复合片弹簧的分开程度,进而改变两端对中心点的刚度,调整吸振频率。这种吸振器常用于控制旋转机械启动和停止时的振动控制。
5.7.9 主动隔振
隔振是在振源与被控对象之间安置适当的隔振器以隔离振源振动的直接传递,其实质是在振源与被控对象之间附加一个子系统,降低振动传递率。根据隔振过程是否需要外加能量,隔振可分为无源隔振(被动隔振)和有源隔振(主动隔振)。被动隔振是在振源与被控对象之间加入弹性元件、阻尼元件甚至惯性元件以及它们的组合所构成的子系统。主动隔振则是用作动器代替被动隔振装置的部分或全部元件,或是在被动隔振的基础上,并联或串联满足一定要求的作动器。
5.7.9.1 主动隔振原理
主动隔振的原理如图27-5-23所示,在干扰源与被控对象之间安装一个作动器,作动器的输出力可以根据控制指令任意变化,改变被控对象的振动状态。与被动隔振相比,主动隔振在低频段具有优越的控制效果,不足之处在于隔振系统较复杂,需要较多的能量输入,因而通常与被动隔振联合使用,以兼顾宽频带隔振性能。

图27-5-23 主动隔振
1—振动传感器;2—控制系统;3—作动器
5.7.9.2 半主动隔振原理
在保证控制性能相近的情况下,采用半主动隔振可降低隔振系统复杂性,降低能耗。采用可调阻尼器的半主动隔振原理如图27-5-24所示,作动器的控制力通过改变阻尼器节流孔径或流体特性实现。因此,为了保证振动控制效果,半主动控制需要实时调节作动器的控制力,其值为,其中
vr为被控对象与基础之间的相对速度,

图27-5-24 半主动隔振
1—振动传感器;2—控制器