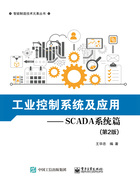
1.2.3 两类典型工业控制系统——SCADA系统与DCS的比较
1.SCADA系统与DCS的相同点
SCADA系统和DCS的相同点如下。
(1)两者具有相同的系统结构。从系统结构来看,两者都属于分布式计算机测控系统,普遍采用客户机/服务器模式。具有控制分散、管理集中的特点。承担现场测控的主要是现场控制站(或下位机),上位机侧重监控与管理。
(2)通信网络在两种类型的控制系统中都起着重要的作用,且通常情况下,至少具有两层网络结构。早期的SCADA系统和DCS都采用专有协议,目前更多的是采用国际标准或事实的标准协议。
(3)下位机编程软件逐步采用符合IEC61131-3和IEC61449等标准的编程语言,编程方式的差异逐步缩小。
(4)近年来,随着计算机软硬件技术、网络通信技术等的发展,SCADA系统和DCS的差异在缩小,两者在功能上越来越接近。
2.SCADA系统与DCS的不同点
作为两类典型的工业控制系统,SCADA系统与DCS虽然存在一些相同之处,但也有明显的不同,主要表现在以下几点。
(1)系统内涵有所不同。
DCS是产品的名称,也代表某种技术,而SCADA系统更侧重功能和集成,在市场上找不到一种广为各行业用户所接受的SCADA系统产品(虽然有很多厂家宣称自己有类似的产品)。SCADA系统的构建更加强调集成,根据生产过程监控要求从市场上采购各种自动化产品来构建满足客户要求的系统。正因为如此,SCADA系统的构建十分灵活,可选择的产品和解决方案也很多。有时候会把SCADA系统称为DCS,主要是因为这类系统也具有控制分散、管理集中的特点。但由于SCADA系统的软硬件控制设备来自多个不同的厂家,而DCS的软硬件来自同一个厂家。因此,虽然两者在技术上有相通之处,但是仍有明显的不同,把SCADA系统称为DCS并不恰当。
(2)系统集成度有所不同。
DCS具有更加成熟、完善、紧密的体系结构,系统的可靠性等性能更有保障,在控制层面,能实现更加复杂的控制功能。而SCADA系统是用户集成的,因此,其整体性能与用户的集成水平紧密相关,通常要低于DCS。正因为DCS是专用系统,所以DCS的开放性比SCADA系统差。
(3)系统结构不同。
目前,一般的SCADA系统都配置专门的SCADA服务器,只有该服务器与现场控制器通信,其他操作员站等站点只和SCADA服务器通信,即操作员站通过该服务器与现场控制站(下位机)进行数据交换,从而实现操作与监控。DCS存在两类模式。一类模式和SCADA系统一样,有专门的服务器,如西门子PCS7和霍尼韦尔的PKS,操作员站只和服务器通信,工程师站和现场控制站直接通信完成组态。另外一类模式没有这种专门的服务器,所有的操作员站都和现场控制站通信,如艾默生过程管理公司的DeltaV和横河电机的Centum等。这两类模式各有特点,但采用前者的DCS产品更多。
(4)通信网络不同。
由于DCS控制的设备比较集中,其测控网络范围局限在厂区,因此,DCS的通信网络通常是局域网,独立性强,企业可以自行维护,运行成本较低;而大型SCADA系统的通信网络一般是广域网,通常依赖电信服务供应商(如中国移动、中国电信等)才能工作,且要持续向供应商缴纳通信服务等费用,运行维护成本高。
(5)应用程序开发与调试有所不同,具体表现在以下几个方面。
①DCS中的变量不需要二次定义。由于DCS中上位机(服务器、操作员站等)、下位机(现场控制器)的软件集成度高,特别是有统一的实时数据库,因此,变量只要定义一次,就在控制器回路组态中可用,在上位机人机界面等其他地方也可用。而在SCADA系统中,一个I/O点,如现场的一个电机设备故障信号,在控制器中要定义一次,在组态软件中还要定义一次,同时要求对两者进行映射(上位机中定义的地址要与控制器中的存储器地址一致),如果地址映射不正确,那么上位机中的参数状态与控制器中就不一致。
这里以图1.10为例进行说明。这里下位机是施耐德Quantum PLC,上位机是组态王7.50,上位机和下位机通过以太网通信,协议是Modbus TCP,PLC的编程环境是Unity Pro V11.0。从图1.10中可以看出,现场的一个“允许远控”转换开关的数字量输入,将进入PLC第一个数字量输入模块的第一个输入通道,其PLC地址就确定了。在Unity Pro中定义该变量(见图1.10(a)),这样PLC中的编程就可使用(见图1.10(b))。上位机人机界面要使用该变量(如显示该开关的状态),就要添加这个PLC设备的驱动,然后定义属于这个设备(Quantum)的变量R1_AUTO(见图1.10(c))。这样在上位机中就可以使用R1_AUTO进行组态了。当然,为了统一上位机和下位机中的变量,一般PLC中的变量名称/标签与上位机组态软件中对应的变量用同样的名称。

图1.10 SCADA系统中上位机和下位机的变量定义与使用
显然,采用这种方式进行控制系统集成有明显不足。目前一些上位机软件支持变量导入与导出,即可以把变量从组态软件中导出,利用Excel等软件快速编辑变量,把该文件导入上位机中,从而简化上位机中的变量定义。有些组态软件支持从PLC导入变量。另外,对于触摸屏的编程,采用类似西门子博图(TIA Portal)这样的全集成自动化软件已能做到资源共享,在触摸屏中可以直接使用控制器中定义的数据类型、变量等。
②DCS控制器中的功能块与人机界面的面板(Faceplate)通常成对出现。例如,在控制器中组态一个PID回路后,在人机界面组态时可以直接根据该回路名称调用一个具有完整的PID功能的人机界面面板,面板中的参数自动与控制回路中的参数一一映射,如图1.11所示。而SCADA系统中的用户必须在人机界面组态软件中自行设计这样的面板,同时把面板中的数据与控制器中的功能块数据进行关联,整个设计过程较为烦琐和费时。
③DCS具有更多的面向模拟量控制的功能块。由于DCS主要面向模拟量较多的应用场合,各种类型的模拟量控制较多。为了便于组态,DCS开发环境中具有更多的面向过程控制的功能块。而不同的SCADA系统的I/O变量的类型分布不一致,通常情况下,数字量点数会更多一些,下位机处理顺序控制逻辑更方便。

图1.11 霍尼韦尔PKS中的PID功能块及其控制面板
④组态语言有所不同。DCS编程主要采用图形化的编程方式,如西门子PCS7使用CFC,罗克韦尔使用功能块图等。而在SCADA系统中,主要使用梯形图和ST等编程语言。当然,在编写顺序控制程序时,DCS中也用SFC编程语言,这点与SCADA系统中的下位机编程是一样的。
⑤调试环境不同。DCS应用软件组态和调试时有一个相对统一的环境,在该环境中,可以方便地进行硬件组态、网络组态、控制器应用软件组态、人机界面组态及相关的调试,而SCADA系统整个功能的实现相对分散。
(6)应用场合不同。
DCS主要用于对控制精度要求高、测控点集中的流程工业,如石油、化工、冶金、电站等。SCADA系统特指远程分布式计算机测控系统,主要用于对测控点十分分散、分布范围广泛的生产过程或设备的监控,通常情况下,测控现场是无人或少人值守的,如对移动通信基站的监控、对长距离石油输送管道的监控、对城市煤气管线的监控等。总体而言,因技术与历史等原因,导致不同类型的控制系统各自称霸相应的行业。
(7)市场规模不同。
由于DCS是成套系统,硬件设备及软件授权等费用高。若I/O点数少于100点,则DCS的单点成本会较高。而SCADA系统中采用的控制器的I/O点数的配置更加灵活,可以根据I/O点数选择相应的控制器,因此,对于I/O点数少的系统来说,SCADA系统的相对成本更低,更容易被用户选用。由于SCADA系统的控制器配置灵活,远程监控的市场需求更大,因此从市场规模来看,SCADA系统远远超过DCS。
3.SCADA系统、DCS与PLC的比较
(1)DCS和SCADA系统具有工程师站、操作员站、现场控制站和通信网络,而PLC只有现场控制站,其主要功能就是进行现场控制,常选用PLC作为SCADA系统的下位机设备,因此,可以把PLC看作SCADA系统的一部分。PLC也可以集成到DCS中,成为DCS的一部分。从这个角度来说,PLC与DCS和SCADA系统是没有可比性的。
(2)系统规模不同。PLC可以用在控制点数从几个到上万个的不同领域,因此,其应用范围极其广泛。而DCS主要用于规模较大的过程,否则其性价比较低。
然而,随着技术的不断发展,各种类型的控制系统相互吸收融合其他系统的特长,DCS与PLC在功能上不断增强,具体地说,DCS的逻辑控制功能在不断增强,PLC的连续控制功能也在不断增强,两者都广泛吸收了现场总线技术,因此它们的界限也在不断模糊。
随着技术的不断进步,各种控制方案层出不穷,一个具体的工业控制问题可以有不同的解决方案。但总体而言,还是遵循传统的思路,即在制造业的控制中,还是首选PLC或SCADA系统解决方案,而过程控制系统首选DCS。对于监控点十分分散的控制过程,多数还是会选SCADA系统,只是随着应用的不同,下位机的选择也会有所不同。
当然,由于控制技术的不断融合,在实际应用中,有些控制系统的选型还是具有一定的灵活性的。以大型污水处理工程为例,由于它通常包括污水管网、泵站、污水处理厂等,在地域上较为分散,检测与控制点绝大多数为数字量I/O,模拟量I/O的数量远远少于数字量I/O,控制要求也没有化工生产过程那么严格,因此,多数情况下,还是选用SCADA系统,而下位机多采用PLC,通信系统采用有线与无线相结合的解决方案。在国内,也有采用DCS作为污水处理厂主控系统的应用。但是,远程泵站与污水处理厂之间的距离通常比较远,且分布比较分散,还是会选用PLC进行现场控制,泵站PLC与厂区DCS之间采用有线通信或无线通信,而这种通信方式主要用在SCADA系统中,在DCS中是比较少见的。因此,污水处理过程控制具有很多SCADA系统的特性,这也是国内外污水处理厂的控制普遍采用SCADA系统而较少采用DCS的原因之一。对于大型油田自动化系统来说,通常同时采用SCADA系统和DCS。在油井侧使用SCADA系统是最为经济的方案,联合站测控点多且分布较为密集,采用DCS是最合适的选择。但如果从整个油田工业控制系统来看,其总体结构还是属于SCADA系统。