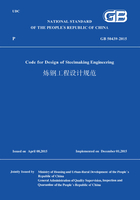
7.3 Process Equipment
7.3.1 For inner profile of ladle for refining,the diameter-height ratio of section below liquid steel level shall be 0.9-1.1 and the free clearance above liquid steel level shall be determined in accordance with the following provisions depending on different refining processes:
1 400mm-600mm for RH;
2 500mm-600mm for LF;
3 800mm-1000mm for VD;
4 ≥1200mm for VOD.
7.3.2 The design of LF refining process should be in accordance with the following provisions:
1 The specific power of transformer shall be 150-200kV·A/t and the liquid steel heating rate shall be 4℃/min-5℃/min.
2 The water cooled steel-copper composite(or aluminum alloy)electrode arm shall be adopted.The diameter of electrode pitch circle and the length of busbar at secondary side should be minimized.The three phases of electrodes shall be arranged in isosceles or equilateral triangle at any cross section and the unbalance of impedance among the three phases shall be less than 5%.
3 The lifting/lowering stroke of electrode shall meet the requirement for the minimum liquid steel volume and the minimum liquid steel volume should be 50%-80% of nominal volume.
4 The ladle lid shall be made of fully water cooled tube-type structure.The structure pattern of ladle lid and the fitness between the lid and ladle opening shall ensure a good reducing atmosphere above liquid steel level.
5 LF shall be equipped with mechanical feeding system.In addition,6-20 elevated bins shall be provided and the volume of bin shall meet the demand for LF operation in more than 8 hours.
7.3.3 The design of RH refining process should be in accordance with the following provisions
1 The main parameters of vacuum vessel shall be defined in the design based on the steel grade to be produced and the dimension of ladle.Multiple vacuum vessels moved with car may be adopted,in which the vacuum vessels can be respectively moved to the treating position and waiting position alternately.In addition,movable hot bend pipe may be adopted.
2 The vacuum vessel shall be provided with online quick heating-up device and also the surface temperature of inner wall of vacuum vessel shall be up to≥1400℃before treatment.
3 The ladle(car)for RH refining should be lifted with hydraulic mechanism.The normal lifting speed shall not be lower than 2000mm/min and the lifting stroke shall meet the requirement for minimum liquid steel volume.
4 If RH unit is built in an area at high altitude,the liquid steel lifting height shall be calculated based on local atmospheric pressure in order to determine a rational snorkel length of vacuum vessel.
5 The RH vacuum vessel with nominal volume of≤200t should be provided with split structure.
7.3.4 In the design,the selection on type of VD and VOD should be in accordance with the following provisions:
1 For the vacuum vessel of VD and VOD,the diameter shall be determined in such a way to meet the requirement for hook accessibility and the height shall be determined based on the height of ladle and also meet the requirement for space of liquid steel leakage.An emergency breakout pit may be arranged outside the vacuum vessel.
2 The flange seal ring between vacuum vessel proper and vessel cover shall be provided with protection device.
3 The vacuum vessel cover may be lifted in hydraulic or electric mode.The vessel cover shall be freely set down when it is put onto vessel proper.
4 The equipment and piping on vacuum vessel cover shall be rationally arranged.For VOD,the oxygen lance shall be located on the centerline of ladle,the discharging pipe of vacuum bucket shall be close to the bottom porous plug of ladle for argon blowing,the temperature measuring and sampling lance shall be located at a position of smoother liquid steel level and the position and angle of air-sealed pinhole camera and sight hole shall ensure clear observation to distance of liquid steel level from ladle opening.
5 If the melting furnace is provided with shorter tap-to-tap time,the operation with twin vacuum vessels may be adopted.
7.3.5 The design of AOD should be in accordance with the following provisions:
1 For AOD,the volume ratio of furnace should be 0.5m3/t-0.7m3/t and the furnace profile and titling mechanism may be designed based on oxygen converter.
2 AOD furnace should be equipped with removable furnace bottom and each furnace bottom shall be provided with 2-3 vessels.
3 The oxygen intensity shall not be less than 1.5Nm3/t·min and the argon intensity shall not be less than 1Nm3/t·min.If refining cycle time of<60min is required for AOD,the initial carbon content shall not be higher than 2.5% and also top oxygen lance shall be provided.
4 AOD furnace shall be equipped with bulk material feeding system,dedusting system and special gas distribution valve station.
7.3.6 Vacuum refining furnace shall be equipped with steam jet vacuum pump or mechanical vacuum pump for vacuumizing and also water-ring vacuum pump may be used as an advance stage of pumps in combination with the steam jet vacuum pump.
1 The capacity of vacuum pump shall be determined based on fume volume of different refining units and total capacity of system.Moreover,it shall be ensured that the operating vacuum degree of vacuum vessel can reach 66.7Pa and also the time for changing atmospheric pressure at cold state to 66.7Pa shall not be more than 6min.
2 The vacuum refining unit with mechanical vacuum pump shall be provided with a fume cooling and filtering system.The dust filtered from the system should be recycled.
3 In the design,specific technical specification shall be provided for manufacture,installation,leakage test and commissioning of all the equipment in vacuum system.
7.3.7 The top lance lifting system for RH,VOD or AOD shall be provided with emergency lifting device.