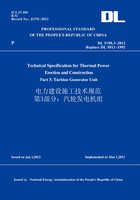
6.7 Lubricating Oil System
6.7.1 Works with lubricating oil system equipment and pipes shall comply with relevant provisions in 6.1 and in this section about work for oil pipes.
6.7.2 Lubricating oil tanks shall be inspected before installation and comply with the following provisions:
1 The outside shall be free of damage,the weld seams shall be free of cracking or missing;the diaphragm joints and the weld seams between section steel frame and tank body inside the oil tank shall be tight.
2 The diaphragms and strainers inside shall conform to drawings,and there shall be no shortcircuiting between oil chambers.
3 Oil tank openings shall conform to drawings,and any change shall be made before feeding oil into the tank.
4 The internal and external ports of flanges shall be tightly welded with oil tank,and threaded holes must not penetrate through oil tank wall.
5 The strainer shall be clean without break,strainer and frame shall join tightly and allow free dismantling,and the oil flow shall not be short-circuited.
6 Before water filling test after completion of oil tank,except temporary blind is permissible for flanges connected to pipes or equipment,other openings shall be fitted with accessories such as socket and formal blind,and applied with packing and coating,and they shall be free of leakage after 24h water filling test.After water filling test,the tank shall be dried up inside and enclosed after temporary anti-corrosion.
7 The inside of oil tank shall be thoroughly cleaned,the paint shall be free of scaling or peeling off.
6.7.3 When the oil tank is located and installed,the permissible deviation of longitudinal and transversal centerline and elevation is 10mm,and the plane of the vertical oil pump installed on the oil tank shall be kept horizontal.
6.7.4 Installation of oil tank oil level meter shall comply with the following provisions:
1 The float shall be checked by immersing in oil and be free of leakage.
2 The indicating rod shall not bend,and the float fit on it shall be secure and vertical.
3 The oil level meter be installed securely and vertically,and the float and marking bar shall be able to move steadily and flexibly up and down.
4 The diameter of connecting pipes and flange ports of oil level meter installed out the the oil tank must not be less than design dimensions,and should not be smaller than∅50mm,connecting pipes must not form an air bag.The top of small oil tank shall be flush with the oil tank cover.
5 The indication scale range of oil level meter and level indication of"normal","max"and"min"shall comply with manufacturer requirements.
6.7.5 The emergency oil drain pipe of oil tank shall be connected to the emergency oil drain pool,and it shall be installed in place and be confirmed through before oil filling into the system.
6.7.6 Inspection and installation of oil injector shall comply with the following provisions:
1 The nozzle and diffusing tube throat diameter and the distance from nozzle to diffusing tube throat shall comply with requirements on drawings and be recorded.
2 The nozzle and diffusing tube shall be securely mounted,the connecting bolts shall be locked,the suction port shall be located below the lowest oil level of the tank and the strainer at the suction port shall be clean in sound condition.
6.7.7 Installation of smoke extractors shall comply with the following provisions:
1 housing shall be free of defect such as damage or missed welding,the oil drain hole of horizontal smoke extractor housing shall be well through.
2 Blades shall be in a sound condition,their direction shall be correct,without touching the casing and can rotate steadily.
3 The inlet pipe shall be provided with an oil and smoke separator.
4 The outlet pipe of the smoke extractor shall be let out of the building separately,and be fitted with gas sampling plug and oil drain tube.
5 The smoke extractor support shall be stable and secure,and shall have a sloping of 5/1000 reverse to the flow direction.
6 Steel impeller must not be used for smoke extractors in sealing oil system.
6.7.8 Inspection and assembling of oil cooler shall also comply with the following provisions,in addition to relevant provisions in 6.1:
1 The water side,oil side,copper tubes and tube plate of the oil cooler shall be cleaned,and there must be no sundries such as casting sand,welding slag,paint film and rusty dirt,the clearance of tube bundle,diaphragm and casing shall comply with manufacturer requirements,and the flow directions of water and oil shall be correct.
2 The expansion compensation rings on tube plate shall be intact without folding trace and the size shall comply with specification.
3 The position of oil side diaphragm shall be correct,and it shall be securely fixed without loosing,and the clearance between the tube bundle diaphragm and housing diameter shall comply with the provisions in Table 6.7.8.
Table 6.7.8 Total radial clearance of oil cooler tube bundle diaphragm and housing(mm)

4 After assembling of oil cooler,openings of flanges and instruments shall be tightly enclosed.
6.7.9 Leakage test for plate oil cooler and tube bundle oil cooler shall comply with the following provisions:
1 Leakage test shall be performed on oil side at 1.25 times the design pressure,and there shall be no leakage when the pressure is maintained for 5min.
2 Reinforcing measures shall be taken for an oil cooler with expansion compensator before test.
3 An oil cooler with lower tube plate and lower water chamber enclosed in the oil chamber can be fitted into the oil chamber only after qualification of water side in hydrostatic test.
4 After pressure test on oil side,additional expanding shall be made for any expansion joint of copper tube with leakage,the joint shall be free of crack after additional expanding,and copper tubes failing in additional expanding and with leakage on wall shall be replaced.
6.7.10 Installation of oil cooler shall comply with the following provisions:
1 The oil cooler installation elevation and centerline shall comply with the requirements on design drawings,the deviation must not exceed 10mm,the housing shall be vertical and the top and bottom deviation shall not exceed 5mm.
2 In the installation of a plate oil cooler,the space for removing,replacing and checking the plate on guide bar shall be provided.
6.7.11 Inspection and installation of oil filter shall comply with the following provisions:
1 The inside of oil filter shall be free of short-circuit.
2 Protection plate of strainer shall be in a sound condition,and holes shall be free of burr and clogging.
3 In an oil filter with cleaning scrape,the filter core shall be able to rotate freely.
4 The disc of oil filter switchover valve shall be tight,without oil leakage from stem,and there shall be clear external marking for switchover positions.
5 The oil flow directions between filtering plates of laminated oil filters shall be correct,there shall be some tightening force between the sets of plates when the top cover is mounted,to prevent oil shortcircuit.
6 The top of oil filter shall be fitted with a vent pipe,and fitted with an inverted U bend.
6.7.12 Installation and inspection of horizontal motor-driven auxiliary oil pump shall comply with the relevant provisions in 9.1 to 9.3,and shall also ensure tightness of shaft seal.
6.7.13 Inspection and installation of vertical auxiliary oil pump shall comply with the following provisions:
1 Inspection shall be made according to relevant provisions in 6.1.4 of this part.
2 The pump shaft bending must not exceed 0.04mm.
3 The strainer shall be clean and free of rupture,and be securely fixed.
4 The load bearing part of oil tank cover shall have sufficient rigidity.
5 After installation of the oil pump,the main shaft shall be vertical and the inlet and outlet flange direction shall be correct.
6 Centering and connection of motor and oil pump shall comply with the relevant provisions in 9.2.
6.7.14 Inspection and installation of oil wheel pump shall also comply with the following provisions,in addition to relevant provisions in 6.7.13:
1 The rubber seal rings between nozzle ring and oil wheel pump shall be in a sound condition with out damage,be coated with grease required by manufacturer when assembled,and the baffle on nozzle ring and strainer shall be clean and be securely fixed.
2 The backing plate above the nozzle ring shall be flat and smooth,after being fitted on the nozzle ring,the plane on the backing plate shall not be above the pump body oil drain flange end.
3 The clearance of different parts of oil wheel pump shall comply with the following values when there is no requirement from manufacturer,as shown in Fig.6.7.14:

Fig.6.7.14 Schematic diagram of clearance of all parts of oil wheel pump
1-baffle;2-thrust bearing;3-adjusting disc;4-backing plate;5-sealing ring;6-nozzle ring;7-strainer;8-oil wheel;9-adjusting shim;10-bearing;11-pump body;12-impeller
Oil wheel:radial clearance on each side between oil wheel and nozzle ring shall be 0.65mm-0.85mm;
Axial clearance between oil wheel and pump body 3.9mm-4.0mm;
Radial clearance of adjusting shim and bearing end oil wheel shaft 3.0mm-4.0mm;
Oil pump:radial clearance between oil pump suction chamber and impeller suction on each side 0.08mm-0.12mm;
Radial clearance on each side of oil pump spiral casing and impeller pressure side 0.08mm-0.12mm;
Oil pump spiral casing and impeller axial clearance permissible deviation of s1 and s2 not greater than 0.07mm;
Thrust clearance 0.12mm-0.15mm;
Bearing pad:total radial clearance 0.08mm-0.15mm.
4 When the oil pump is assembled,all bolts shall be fitted with lock washer,and after completion of assembling,the connecting bolts between oil wheel pump body and cover shall be locked according to manufacturer requirements.
6.7.15 Installation of jacking oil pipe shall also comply with the following provisions in addition to the provisions in 6.1:
1 Oil pump inlet and outlet shall be correctly connected with oil pipes.
2 Before installation,pipes,connectors and bearing pad slots shall be purged clean.
3 Sleeve welding should be used for pipe connectors.
4 The jacking oil pipe connected to bearing housing shall have expansion compensation,and the valve shall be tight without leak.
5 The jacking oil pump installation position shall be such that the oil pump inlet is below the minimum oil level of main oil tank,and the inlet shall be provided with a strainer.
6 Oil pressure gauge shall be provided for jacking oil pipe of each bearing,a throttle valve and oneway valve shall be fitted upstream the meter,which shall be qualified after calibration.
7 The oil overflow port at the upper part of jacking oil pump shall be directly connected to the oil return vessel.
8 The jacking oil pipe shall be insulated when connected with the generator rear bearing pedestals,the insulation resistance shall be no less than 0.5MΩ when measured with a 1000V megohm meter,and the insulated connectors shall have sufficient strength.