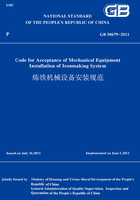
6.5 Fabrication of Shell
6.5.1 The construction drawing for manufacturing shell shall comprise lifting,strengthening,transportation and packaging of furnace shell,scaffold lug,fixed block of clamp and locator,etc.Their quantity and location shall be proposed by the ordering organization in cooperation with the installation organization and be listed in the appendix to the ordering contract.
6.5.2 The cutting edge of the shell steel plate shall be smooth.The welding amount of contraction shall be reserved in edge length.The cutting allowable deviation of the steel plate of the butt joint or T-shaped joint is±2.0mm.The difference between two diagonal lines shall be checked for the steel plate of the butt joint,with allowable deviation of 3.0mm.
6.5.3 The type and dimension of the joint of the steel plate shall be in accordance with those specified in the design document or Item 1 and Item 2 of Article 6.2.11 of this standard.The joint processing method shall be in accordance with the following requirements:
1 The carbon structural steel and low alloy structural steel with standard tensile strength of no larger than 540MPa may be subject to cold machining or hot machining.When adopting hot machining,the surface layer affecting the welding quality shall be removed by the cold machining method.
2 When adopting the flame cutting method to process the joint,the quality of the cutting surface shall be in accordance with those specified in Article 6.4.2 of this standard.
3 The surface of the joint shall be free of cracks,layers,slag inclusion and other defects.
6.5.4 During butt joint of the plates with different thicknesses,the inside surface of the blast furnace shell shall be flush and be in accordance with the following requirements:
1 When the butted plate thickness is no larger than 40mm and the thickness difference is no larger than 4mm,a gentle transition method for metal surface layer of welding seam may be used for treatment[Figure 6.5.4(a)].When the thickness difference is larger than 4mm,a thermal cutting or cold working method shall be adopted to make inclination of 1∶3 from one side of the thickness direction of the thicker plate[Figure 6.5.4(c)].
2 When the butted plate thickness is larger than 40mm and the thickness difference is less than 6mm,the gentle transition method for metal surface layer of welding seam may be used for treatment[Figure 6.5.4(b)].When the thickness difference is larger than 6mm,the thermal cutting or cold working method shall be adopted to make inclination of 1∶3 from one side of the thickness direction of the thicker plate[Figure 6.5.4(d)].

Figure 6.5.4 Butting of plates with different thicknesses
(a)When the thickness of the butted plate is no larger than 40mm,the thickness difference is less than 4mm.(b)When the thickness of the butted plate is larger than 40mm,the thickness difference is less than 6mm.(c)When the thickness of the butted plate is no larger than 40mm,the thickness difference is larger than or equal to 4mm.(d)When the thickness of the butted plate is larger than 40mm,the thickness difference is larger than or equal to 6mm.
6.5.5 The cylindrical and tapered shells of the elements,including shells of blast furnace and hot-blast stove may be subject to cold roll forming through a plate bending machine and the press machine.A transition circular arc section between the blast-furnace throat and gas closing plate and spherically-tapered top of the hot-blast stove should be subject to hot press molding by mould and shall meet the requirements of the design document.
6.5.6 After bending and molding the shell,the edge of the steel plate shall be free of cracks,layers,wrinkles and slag inclusion.The actual thickness of the steel plate with treated base course must not be less than the minimum allowable thickness.
6.5.7 A pressure head shall be reserved for the bent and molded shell steel plate and shall not be shorter than 150mm.The bent and molded shell steel plate shall be checked by arched sample plate.The chord length of the sample plate shall not be less than 1500mm.The gap between the camber line of the molding part and the sample plate shall not be larger than 2.0mm.
6.5.8 After molding,the single block of furnace shall be placed on the platform for check,and the allowable deviation of arc length of the blast furnace shell is±3mm.No gap exists between the lower opening and the platform.The local gap shall not be larger than 2mm.The allowable deviation of perpendicular height of the arc plate or the tapered sector plate is±3mm.The included angle between the shell steel plate of the furnace body and furnace bosh and the platform may be measured and calculated solidly,with the allowable deviation of±3'.The arc inspection of the upper opening and the lower moth shall be in accordance with those specified in Article 6.5.7 of this standard.
6.5.9 The preassembly of single ring shell shall be in accordance with the following requirements:
1 Before assembling,rust,burrs,oil stains or rust-resisting materials for protecting the joint within the range of 50mm to each side of the butt weld shall be cleared away.
2 The preassembly of the shell shall be conducted on a specialized preassembly platform,which shall be in accordance with those specified in Item 3 of Article 6.4.8 of this standard.
3 Before assembling each ring of furnace shell,the precision of the preassembly platform shall be detected and adjusted in accordance with those specified in Item 3 of Article 6.4.8 of this standard,and then the preassembly of the next ring of blast furnace shell shall be conducted.
4 The project line of the profile of the upper opening and the lower moth of the blast furnace shell shall be scribed on the preassembly platform.The central point of the blast furnace shell ring and 4-core point of 0°,90°,180° and 270° of the external ring of the blast furnace shell shall be marked obviously.
5 Padding plate and locking plate for locating blast furnace shell should be arranged for preassembly of the shell.The height difference of the upper surface of the padding plate shall be less than 2mm.
6 The allowable deviation of geometric shape and dimension for preassembly of shell shall meet the requirements of Table 6.5.9.
Table 6.5.9 Allowable deviation of geometric shape and dimension for preassembly of shell(mm)

Table 6.5.9(Continued)

Note:D is the diameter of the bottom plate of the furnace,H is the height of the single ring furnace shell,and D1 is the diameter of the blast furnace shell steel plate ring.
6.5.10 The preassembly of multi-ring(belt,loop)blast furnace shell section shall be in accordance with the following requirements:
1 The preassembly of the multi-ring(belt,loop)blast furnace shell shall be conducted on the basis that the preassembly of the single ring(belt,loop)blast furnace shell is qualified.If the preassembly is not qualified,the single ring(belt,loop)blast furnace shell must not take part in the assembly of the multi-ring(belt,loop)blast furnace shell section.Between the upper single ring and the lower ring(belt,loop)for preassembly of the multi-ring(belt,loop)furnace shell,a limiting baffle plate should be welded on the upper mouth of the lower ring.
2 The preassembly of the blast furnace shell shall be conducted from up to down.The quantity of the rings assembled(belt,loop)every time shall be determined according to the specific conditions in the plant.After assembling one unit of multi-ring(belt,loop)and disassembling single ring(belt,loop)product,the uppermost ring(belt,loop)shall be remained as the bottom ring(belt,loop)of the next assembling unit.
3 For the preassembly of the furnace shell,the lifting lug,scaffold lugs,the fixed block of clamp and the locator shall be welded on each block of blast furnace shell steel plate according to the provisions of the appendix to the contract.Each assembled ring(belt,loop)shall be equipped with scaffolds,springboards,tracks and ladders,etc.after disassembling,the welded scaffold lugs shall be remained.During the preassembly of the furnace shell,positioned welding shall not be adopted,but fixtures,clamps,fixed parts and the like shall be used.The fixed parts should be remained after disassembling.
4 After ring-by-ring(belt,loop)inspection is qualified,the 4-core point of 0°,90°,180° and 270°shall be obviously marked in the joint of the disassembled upper and lower rings(belt,loop)in the forms of paint and stamp.
5 The T-shaped butt weld shall be used for intersection of the vertical weld and the ring weld of the furnace shell.The vertical weld between two rings(belt,loop)shall be staggered with a distance of no less than 200mm.
6 The preassembly of the multi-ring(belt,loop)blast furnace shell section shall be in accordance with those specified in Table 6.5.9 of this standard.
6.5.11 The tapping of the blast furnace shell shall be in accordance with the following requirements:
1 Automatic cutting or mechanical cutting device shall be adopted for tapping on the furnace shell.Planar tapping may be performed before molding the steel plate or three-dimensional tapping may be performed after the preassembly is qualified.When the aperture is less than 50mm,mechanical tapping shall be adopted;and when the aperture is larger than or equal to 50mm,the automatic cutting machine should be adopted for tapping.The tapping dimension shall meet the requirements of the design document.The surrounding of the hole shall be smooth and be free of burrs or trenches.
2 If the distance from the hole edge to the ring weld welded in the installation site is less than or equal to 50mm or that from the hole edge to the vertical weld is less than 200mm,the holes shall be scribed and located in the plant and shall be tapped after grouping and welding on the installation site.
3 The pipes connected with the blast furnace shell should extend into the furnace with a size of no larger than the gap between the shell and the brick lining.
6.5.12 The assembly of the blast furnace shell and the tuyere flange shall be in accordance with the following requirements:
1 After assembling the blast furnace shell at the tuyere section,the tuyere shall be located.The central position of the tuyere shall be determined by an instrument from the specified points of the 4-core point of 0°,90°,180° and 270° along the circle of the blast furnace shell at an equal angle,with the allowable deviation of 4'.The central position of the tuyere should be positioned by a total station and an infrared laser.
2 The tapping of the tuyere and the installation and welding of the tuyere flange shall be in accordance with the following requirements:
1)Tooling shall be arranged for tapping of the tuyere.The NC cutting machine,semi-automatic cutting machine and automatic cutting machine may be adopted.
2)The allowable deviation of center elevation of tuyere flange is±3.0mm.The allowable deviation of center height difference between two adjacent tuyeres is 3.0mm.The centers of all tuyere centers shall be in the same horizontal plane,and its allowable deviation of height difference is 5.0mm.
3)The horizontal connecting line of each flange of each relative tuyere in the center shall be intersected with the center line of the furnace body,with the allowable deviation of 10mm.
4)The allowable deviation of perpendicularity between the horizontal connecting line of each flange of each relative tuyere in the center and the horizontal center line of the tuyere flange face and in perpendicularity of the flange face is 3/1000.
5)The allowable deviation of levelness of the horizontal center line of the flange face in the diameter of the flange is 2mm.
6)The allowable deviation of distance of the flange extending the surface of the blast furnace shell is 5mm.
3 The welded tuyere flange shall be subject to stress relieving treatment and meet the requirements of the design document.The provisions of Item 7 of Article 6.2.12 of this standard shall be complied with when there is no requirement in the design document.
4 After the stress relieving treatment of the tuyere section by blocking,the blast furnace shell of the tuyere section shall be subject to secondary assembly.The tuyere shall be precisely positioned by the total station and the infrared laser and be subject to machining.
5 For the final preassembly of the tuyere section and the installation of tuyere-cooler shell,the centrality of the tuyere shall be checked and in accordance with those specified in Item 2 of this article.
6 The installation of the tuyere and the inspection of the centrality of the tuyere may be detected by the total station and the infrared laser.
6.5.13 The internal quality of the weld of the tuyere shall be in accordance with those specified in Article 6.2.22 of this standard.
6.5.14 The tuyere-cooler shell shall be assembled in the manufacturer.The shell shall be matched with the tuyere flange tightly and the connection bolt shall be uniform and firm.The flange face and the boltnut pair shall be welded and sealed according to the provisions of the design document and be taken penetration test.
6.5.15 The direct assembly and welding between the tuyere-cooler shell and the blast furnace shell shall be in accordance with those specified in Article 6.5.12 and Article 6.5.13 of this standard.
6.5.16 Taphole sleeves and slag hole flange on the blast furnace shell shall be assembled and welded in the manufacturer and be in accordance with the following requirements:
1 The central points of the taphole sleeves and the slag hole flange shall be measured from the specified points of the 4-core point of 0°,90°,180° and 270° along the circle of the furnace shell,with the allowable deviation of 4'.The allowable deviation of the center elevation of the flange is±5.0mm and that in levelness of the center line of the flange in the horizontal diameter is 3.0mm.
2 The welding of the slag hole and the taphole sleeve flange shall be firm and reliable,be free of lack of welding,and meet the requirements of Section 6.2 of this standard.In addition,the weld metal shall be full.
6.5.17 The flange of the cooling equipments of furnace on the blast furnace shell shall be in accordance with the following requirements:
1 The central points of the cooling plate flange on the blast furnace shell shall be measured from the specified points of the 4-core point of 0°,90°,180° and 270° along the circle of the furnace shell,with the allowable deviation of 4'.The center distance may also be measured,with the allowable deviation of±5.0mm.The allowable deviation of the center distance of two adjacent layers of flanges is±5.0mm.The allowable deviation of distance from two ends of the center line of the horizontal plane of the flange face to the surface of the blast furnace shell respectively is 3mm.The allowable deviation of perpendicularity of the flange face within the full height of the flange is 3mm.
2 The allowable deviation of center distance of the holes at the same group of the cooling wall in horizontal direction and perpendicular direction is±2mm.The allowable deviation of center distance of the hole at the adjacent groups in horizontal direction and perpendicular direction is±3mm.The water pipe hole should not exceed 1.5 times of the outer diameter of the pipe and the bolt hole should not exceed 1.3 times of the diameter of the bolt.
6.5.18 The assembly of the flanges of gas sampling device of blast furnace,throat temperature measuring device,throat spray device and top ignition device on the blast furnace shell shall be in accordance with the following requirements:
1 The center position of the flange of the throat temperature measuring device on the blast furnace shell shall be measured from the specified starting point along the circle of the furnace shell,with the allowable deviation of 5'.The allowable deviation of center elevation is±5.0mm.The center height difference of the adjacent flanges shall not be larger than 5.0mm.
2 The center position of the flange of the throat spray device on the blast furnace shell shall be measured from the specified starting point along the circle of the furnace shell,with the allowable deviation of 4'.The allowable deviation of center elevation is±10mm.The center height difference of the adjacent flanges must not be larger than 10mm.
3 The center position of the flange of the gas sampling device on the blast furnace shell shall be measured from the specified starting point along the circle of the furnace shell,with the allowable deviation of 5'.The allowable deviation of center elevation is±10mm.For the perpendicularity of the flange face and the longitudinal center of the sampling device,the allowable deviation of the flange diameter of no larger than 500mm is 1.0mm;and that in the flange diameter of larger than 500mm is 2/1000.The distance of the flange extending the blast furnace shell is checked at the peak of the end face of the flange,with the allowable deviation of±5.0mm.
4 The center position of the flange of the top ignition device on the blast furnace shell shall be measured from the specified starting point along the circle of the furnace shell,with the allowable deviation of 5'.The allowable deviation of center elevation is±10mm.
6.5.19 When the blast furnace shell is installed by a hydraulic lifting device of bearing steel string through reversal set up,the furnace top shall be provided with a bearing(ring)beam and should be preassembled with the corresponding furnace shell.
6.5.20 After the preassembly is qualified,the blast furnace shell element shall be recorded and numbered Butting marks of 4-core point of 0°,90°,180° and 270° along the circle shall be marked with paint and sample punch.The assembly and numbering drawing shall be prepared.
6.5.21 After preassembly,the blast furnace shell shall be disassembled into 2-4 parts according to the installation and transportation conditions.Reinforcing measures for preventing deformation of the blast furnace shell shall be taken for each part.