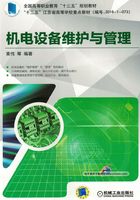
3.3 拆卸零件的检验
3.3.1 拆卸零件检验分类及检验原则
零件可能产生缺陷,如龟裂、裂纹等对其使用性能的影响,应掌握检测方法与标准、易损零件的极限磨损及允许标准、配合件的极限间隙及允许配合间隙标准等。还要掌握零件的特殊报废条件,如电镀层性能、镀层轴承与机体的结合强度、平衡和密封的破坏及弹性件的弹力消失等。
拆卸的零件通过分析、检验和测量,可分为可用、不可用和经过修理后可用三类。可用零件指其所处技术状态仍能达到各级修理技术标准,不经过修理便能够直接进入装配使用。如果零件所处技术状态已经劣化至低于各级修理技术标准或使用规范等,则均属于续修零件。有些零件通过修理不仅能够达到修理技术标准,而且还经济核算,此时应当尽量给予修理并重新使用;有些零件通过修理尽管能够达到修理技术标准,但修理成本很高,通常不予修理而更换新件;当零件所处技术状态如材料变质、强度不够等,已经无法采用修理方法达到规定的技术要求时,应当作报废处理。
1.节约原则
在保证质量前提下,缩短维修时间,节约原材料、配件、工时,提高利用率,降低成本。
2.技术规范原则
严格掌握技术规范、修理规范,正确区分能用、需修、报废的技术条件,从技术和经济效果综合考虑,不合格的零件不能继续使用,也不让不必维修或不应报废的零件进行修理或报废。
3.检验原则
提高检验水平,尽可能消除或减少误差,建立健全合理的规章制度。按照检验对象的要求,特别是精度要求选用检验工具或设备,采用正确的检验方法。
3.3.2 检验的内容
1.检验分类
(1)修前检验
在机械设备拆卸后进行。对已确定需要修复的零部件,可根据损坏情况及生产条件选择适当的修复工艺;对报废的零部件,要提出需补充的备件型号、规格和数量;不属备件的需要提出零件蓝图或测绘草图。
(2)修后检验
零件加工或修理后检验其质量是否达到规定的技术标准,确定是成品、废品还是要返修。
(3)装配检验
指检验待装零部件质量是否合格,能否满足要求;装配中对每道工序或工步都要进行检验,以免产生中间工序不合格,影响装配质量;组装后,检验累积误差是否超过技术要求;总装后要调整,包括工件精度、几何精度及其他性能检验、试运转等,确保维修质量。
2.检验的主要内容
1)零件的几何精度。包括尺寸、形状和表面相互位置精度,经常检验的是尺寸、圆柱度、圆度、平面度、直线度、同轴度、平行度、垂直度、跳动等项目。根据维修特点,有时不是追求单个零件的几何尺寸精度,而是要求配合精度。
2)零件的表面质量。包括表面粗糙度,表面有无擦伤、腐蚀、裂纹、剥落、烧损、拉毛等缺陷。
3)零件的物理力学性能。包括硬度、硬化层深度,还有对零件制造和修复过程中形成的性能,如应力状态、平衡状况、弹性、刚度、振动等也需根据情况适当进行检测。
4)零件的隐蔽缺陷。包括制造过程中的内部夹渣气孔、疏松、空洞、焊缝等缺陷,还有使用过程中产生的微观裂纹。
5)零部件的质量和静动平衡。包括活塞、连杆组之间的质量;曲轴、风扇、传动轴、车轮等高速转动的零部件进行静动平衡检验。
6)零件的材料性质。包括零件合金成分、渗碳层含碳量、各部分材料的均匀性、铸铁中石墨的析出、橡胶材料的老化变质程度等。
7)零件表层材料与基体的结合强度。包括电镀层、喷涂层、堆焊层和基体金属的结合强度,机械固定连接件的连接强度,轴承合金和轴承座的结合强度等。
8)组件的配合情况。包括组件的同轴度、平行度、啮合情况与配合的严密性等。
9)零件的磨损程度。正确识别摩擦磨损零件的可行性,由磨损极限确定是否能继续使用。
10)密封性。如内燃机缸体、缸盖需进行密封试验,检查有无泄漏。
3.检验的方法
(1)感觉检验法
不用量具、仪器,仅凭检验人员的直观感觉和经验,鉴别零件的技术状况。精度不高,适于分辨缺陷明显的或精度要求不高的零件,要求检验人员经验丰富。
1)目测。用眼睛或借助放大镜对零件进行观察和宏观检验,如倒角、圆角、裂纹、断裂、疲劳剥落、磨损、刮伤、蚀损、变形、老化等,做出可靠的判断。
2)耳听。根据机械设备运转时发出的声音,或敲击零件时的响声判断其技术状态;零件无缺陷时声响清脆,内部有缩孔时声音相对低沉,若内部出现裂纹,则声音嘶哑。
3)触觉。用手与被检验的零件接触,可判断工作时温度的高低和表面状况;将配合件进行相对运动,可判断配合间隙的大小。
(2)测量工具和仪器检验法
1)用各种测量工具和仪器检验零件的尺寸、几何形状和相互位置精度;测量工具有卡钳、钢直尺、游标卡尺、百分尺、千分尺或百分表、千分表、塞规、量块、齿轮规等。
2)用专用仪器和设备对零件的应力、强度、硬度、冲击性、伸长率等力学性能检验。
3)用静动平衡试验机对高速运转的零件做静动平衡检验。
4)用弹簧检验仪或弹簧秤对各种弹簧的弹力和刚度进行检验。
5)对承受内部介质压力并须防止泄漏的零部件,需在专用设备上进行密封性能检验。
6)用金相显微镜检验金属组织、晶粒形状及尺寸、显微缺陷,分析化学成分。
此方法由于能达到检验精度要求,测量工具较多,应用最广。
(3)无损检测
利用电、磁、光、声、热等物理量,通过零部件引起的变化来测定技术状况,发现内部缺陷。采用专门的仪器、工具检测,不会使零部件受伤、分离或损坏。无损检测是专业检测,出具检验报告的检验人员需要通过资质考试。
对维修而言,这种检测主要是对零部件定期检查、维修检查、运转中检查,发现缺陷,根据缺陷的种类、形状、大小、产生部位、应力水平、应力方向等,预测缺陷发展程度,确定采取修补或报废。广泛应用的有磁力法、渗透法、超声波法、射线法等。确定零件隐蔽缺陷的性质、大小、部位及取向等,因此,在选择无损检测法和操作时,必须结合零件的工作条件,考虑受力状况,生产工艺,检测要求,经济因素。
上面提到的几种无损检测法各有特点,并不是适用于所有隐蔽缺陷检测。渗透检测法在零件表面上涂渗透剂,显示缺陷,简单的裂纹可以检测出1mm;磁粉探伤检测法利用铁磁材料在电磁场作用下能够产生磁化的原理,即被检测零件在磁场作用下,表面缺陷的磁力线泄漏或聚集形成局部磁化吸附磁粉,显示出缺陷的位置、形状和取向,可检测出在表面内部的缺陷,但需要操作者有经验,如图3-4所示。超声波检测法是利用某些物质的压电效应产生的超声波在介质传播遇到不同介质间的介面如内部裂纹、夹渣和小孔等缺陷,产生反射、折射等特性,可以检测内部较深的缺陷,但检测人员必须经验丰富,如图3-5所示。射线检测法是利用射线照射,使其穿透零件,当遇到缺陷如内部裂纹、夹渣、疏松和小孔等,射线则容易穿透,这样从被检测零件缺陷处透过射线的能量比其他位置多,即能够检测到材料的内部缺陷,但成本高,需防护措施,一般超声波检测无法判断的重要零件,采用射线检测法,如图3-6所示。
图3-4 磁粉探伤检测
1—零件 2—内部缺陷 3—局部缺陷 4—泄漏磁通 5—磁力线
图3-5 超声波检测法
1—显示器 2—零件 3—耦合器 4—检测头
图3-6 射线检测法
1—射线管 2—隔离保护箱 3—射线 4—工件 5—感光片
需注意,无损检测法的操作人员,必须持有权威部门颁发的资质证书才能签发探伤
报告。
课堂练习
(1)零件检验的原则有哪些?检验的方法有哪些?
(2)请叙述无损检测的含义和种类,每种检测的特点有何不同?