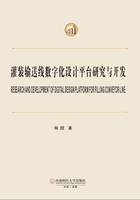
1.2 研究现状
1.2.1 数字化设计现状
数字化、精密化、智能化、微型化、生命化和生态化是21世纪的机械制造工程的六大发展方向。在构成制造系统的三大要素物质、能量和信息中,信息正成为制约现代制造系统的主导因素,数字化被列为机械制造工程六大发展趋势之首。
数字化是指以数字计算机为工具,科学地处理机械制造信息的一种行业应用状态。数字化技术是指以计算机硬件、计算机软件、信息存储、通信协议、周边设备和互联网等为技术手段,以信息科学理论为基础,包括信息的数字表达、收集、处理、存贮、传递、传感、仿真、控制、物化、集成和联网等领域的科学技术集合。
产品数字化设计与制造主要包括用于企业的计算机辅助设计(CAD)、制造(CAM)、工艺设计(CAPP)、工程分析(CAE)、产品数据管理(PDM)等内容。其数字化设计的内涵是支持企业的产品开发全过程、支持产品相关数据管理、支持企业产品开发流程的控制与优化等。归纳起来就是产品建模是基础,优化设计是主体,数控技术是工具,数据管理是核心。
(1)数字化设计国内研究现状
国内学术界当前对于产品数字化设计与制造的研究,主要集中在产品的模块化设计方法[5,6]、集成化产品建模[7]、基于产品平台的数字化设计制造技术及其应用[8]、基于事物特性表的产品设计/制造/测量集成技术[9]等方面,并已有虚拟仿真技术在灌装生产线设计中的应用研究[10,11]。
数字化设计与制造主要包括用于企业的计算机辅助设计(CAD)数字化仿真及其相应文档的建立技术内涵,随着经济全球化和市场化的推进,数字化设计在制造业中的重要性逐步被企业认可,数字化设计经历了“2维CAD→3维实体造型→参数化3维建模系统→变量化3维建模系统→虚拟现实技术”[12]的发展历程。数字化设计与制造技术在大型飞机的设计制造过程中贯穿于产品研发制造的全过程,且与精益生产、并行工程等先进技术相融合,实现了良好的应用[13]。数字化设计制造CAX技术及PDM等技术在摩托车研发制造过程中提高了产品创新能力,缩短了产品开发周期[14]。数字化制造技术在模具设计中得到良好的应用[15]。数字化制造是先进制造技术的核心技术[16],其作用体现在数字化智能设计、数控加工、数值仿真技术、设计优化技术和信息管理技术、三坐标测量(CMM)及计算机辅助检测(CAI)等技术[17,18]对产品设计制造的支撑。
(2)数字化设计国外研究现状
国外学术界对于数字化设计与制造的研究,主要体现在多参数集成产品模型[19],产品全生命周期条件下设计与制造的集成[20],以降低制造成本为目的的大规模定制技术、以成组技术和工业机器人为依托的柔性制造技术、以CAD与CAM集成为手段的计算机集成制造技术、以质量控制为目的的精益生产技术、以及时交货为导向的JIT(Just-in-Time)技术、以CAX和PDM集成的并行工程技术、以流程再造(BPR)和制造业信息化为主体的敏捷制造技术[21]。
1.2.2 产品建模的研究现状
产品建模是将产品的信息存储于计算机并得以表达的过程。常见的建模方法主要有参数化建模、面向对象的建模方法、知识重用等。主要模型有:语言模型、几何模型、特征模型、图树模型、对象模型、知识模型、图像模型[22]。
除了产品模型的建立以外,产品建模方法也是近年来学术界研究的热点。如智能产品建模的方法[23],基于产品族的参数化建模方法[24],面向产品全生命周期的零件族建模方法[25],基于本体技术的产品建模方法[26],基于国际标准ISO 13584的建模方法[27],顾新建等[28]提出了面向大批量定制的模块化建模技术,谭建荣等[29]提出了面向协同装配的产品建模方法,祁国宁等[30]提出的面向多学科优化的建模设计方法等。
1.2.3 变型设计研究现状
变型设计是指在原有零部件的基础上,通过改变零部件的参数,从而达到外形相似的零部件,其本身零部件的基本功能和主结构不会发生变化。变型设计是根据客户的设计要求,在已有的零部件模型或是在已有的变型零部件实例中通过改变零部件的特征参数,从而能快速设计出满足客户要求的产品。变型设计有效地利用了企业已有的资源,大大减少了设计人员的工作量,提高了设计制造企业的竞争力。
对于变型设计应用的范围,学术界有着不同的说法。Stutz J等[31]指出在机械产品设计中有30%的设计是属于变型设计范畴,Prebil I等[32]则指出在产品设计中大概有70%左右的产品设计可以归入变型设计范畴。但其都有一个普遍的认识,那就是,产品设计是完全可以进行变型设计的。
严晓光等[33]对PDM和CAD的集成进行了研究,将事物特性表(SML)技术与参数化CAX技术相结合,实现了产品造型的变型和工艺的变型。余军合等[34]利用事物特性表对零件族进行描述,减少零部件种类,实现了产品的快速设计。
鲁玉军等[35]以CAD系统Solid Edge为具体应用对象,研究了基于事物特性表进行产品变型设计的原理,并借助Excel的表处理功能建立了事物特性表,对Solid Edge的变量表功能进行了二次开发,实现产品变型设计的方法和过程。
武守飞等[36]提出了一种基于元件基础框架的结构变型设计方法。史俊友[37]等基于PDM平台开发了支持产品快速组合设计的变型设计系统,其变型设计系统支持平台及运行流程如图1.1所示。

图1.1 系统的支持平台及运行流程
1.2.4 灌装输送线数字化设计的研究现状
灌装输送线在整条食品饮料生产线中起到链接各个工作站的作用,这些工作站典型的包括灌装机、热饮冷却机、贴标机(套标机和封标机)、装箱机等自动化工作站设备,所以灌装输送线是整条食品饮料生产线的重要部分。灌装输送线设计是否合理直接影响到整条饮料生产线的运作和效率。
当前国外灌装输送线设计与制造水平较高的有美国、日本、德国、英国、意大利。这些国家的灌装输送线设计通常为了适合客户的要求,使用了大量的设计、制造、仿真先进技术。灌装输送线的设计与制造正向以下几个趋势发展:①工艺流程自动化程度越来越高;②适应产品变化能力越来越强;③成套供应能力强;④普通采用仿真设计技术。
国内灌装机械行业起步于20世纪70年代,在80年代末和90年代中得到了迅速发展。在食品饮料机械产品设计领域,绝大多数设计人员仍沿用以前的设计方法:①根据设计任务书寻找同类机型作为样机;②参考样机制定各项技术性能指标及使用范围;③设计关键零部件、设计总装图方案和动作循环图;④设计部件图、总装图和零件图;⑤对主要部件中的关键零件进行强度、刚度校核;⑥设计控制原理图、施工图等。目前,我国基本上可以进行自主设计中低速运行的灌装输送线,但高速运行的输送线机械,特别是一些先进机械,大多仍是测绘、仿制国外的同类机型,进行国产化设计和系列化设计。
王书亭等[2]采用面向对象的方法对灌装输送线三维仿真系统进行了设计,邹湘军等[38]采用多Agent方法对灌装生产线建模进行了研究,提出了灌装生产线虚拟环境Multi-Agent新的建模方法。熊焕云等[10、39]将虚拟制造技术运用于虚拟灌装生产线,建立了制造环境中的资源类库和相应的模型库,实现了灌装生产线工艺流程仿真系统。
曹菲等[40]通过将生产物流系统分析方法用于啤酒灌装生产线设施布局,对布局进行了优化设计,高原等[1]对灌装输送线上的分列装置进行了研究,通过对输送线上前后物流的分析,研究了分列装置的设计。
从灌装输送线数字化设计与制造国内外研究现状来看,对于灌装输送线的研究大部分是在三维仿真建模及建模优化上,对于灌装输送线建模,灌装输送线组成单元、支持灌装输送线设计的零部件库及零部件建模等理论方法的研究和应用实例还不是很多。因此,研究如何能快速设计出满足客户要求的灌装输送线的理论方法对于企业来说是具有非常重要的现实意义的。