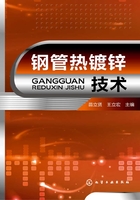
第二节 热镀锌镀前预处理
钢铁材料及其制件的表面,由于加工、储运过程中容易生成或附着异物,如氧化皮、油污、加工碎屑及尘土等,因而不能对其直接进行热镀锌,需要做适当的表面预处理。钢铁制件的热镀锌前处理的质量的好坏,对热镀锌层质量有极大的影响,因此应给予高度重视。镀锌前预处理的工艺步骤一般为:脱脂→水洗→酸洗除锈→水洗→浸粘溶剂助镀→烘干。
一、脱脂除油
此工序主要用来去除钢铁制件表面上黏附的油脂等与水不相溶的物质,以避免影响除锈、溶剂助镀和热镀锌效果。该工序往往被忽略不进行或不太注意其质量。实际上脱脂质量的好坏将直接影响后续工艺及热镀锌质量。对于多数热浸镀锌钢铁制件,表面油污通常不会特别严重,其脱脂方法相对来说可较为简单,常用的脱脂方法由几种碱性物质所组成。下面介绍几种脱脂除油的方法。
1.化学脱脂法
碳酸钠: 40~50g/L;
硅酸钠: 25~30g/L;
磷酸钠: 40~50g/L;
时间: 30~35min;
温度: 80~85℃。
2.电解脱脂法
关于电解脱脂配方工艺参数见表3-1。
表3-1 电解脱脂配方工艺参数

3.酸性脱脂法
酸性脱脂是由有机或无机酸添加表面活性剂混合配制而成的。是一种除油除锈一步法工艺。钢制件在这种除油剂溶液中,表面上的锈蚀氧化层溶于浸蚀剂中,而油污则借助表面活性剂的乳化作用而被除去。这种方法简化了预处理工艺,减少了设备用量和投资,节省了占地面积和水及有关的化工原料。生产中一般只用于对油污和锈蚀不太严重的金属零件进行热镀锌前的预处理,至于选用何种浸蚀剂、乳化剂的工艺,则取决于零件材料及其表面状态。常用的工艺见表3-2。
表3-2 酸性脱脂法配方

4.超声波脱脂法
超声波脱脂除油的特点是:可以使黑色金属表面的洁净度大幅度提高,脱脂除油速度快,效率高;选用时可采用PLC控制系统,可以实现大批量钢制件的自动化脱脂除油,降低工人劳动强度,同时,防止钢制件由于人为因素造成钢制件之间的机械损伤。选用超声波对钢工件进行脱脂除油时,要对超声波清洗的功率进行计算,计算步骤如下。
(1)超声波的声强 经测试,在质量分数15%~20%、温度50~60℃的酸洗液中,能够有效地清洗钢材表面氧化物的超声波声强为1.1~1.3W/cm2。
(2)功率的计算
P=S(I+K) (3-1)
式中 I——超声波的声强,W/cm2;
S——被清洗物体的表面积,cm2;
P——加载到振板上的电功率,W;
K——超声波的声强有所损失超声波校正系数。
在超声波清洗设备中振子黏结不锈钢板,使超声波的声强有所损失,超声波校正系数K约为0.01W/cm2。
钢制件在超声波清洗介质中被清洗的表面积:
S=10LWt (3-2)
式中 L——钢制件的长度,mm;
W——钢制件的宽度,mm;
t——在磷酸超声波中洗净钢制件所需的时间,min。
例如对钢制件表面进行超声波清洗时,面积越大,在池子里时间越长,表面氧化率越高,则洗净钢制件所需的时间越长;反之,时间越短。
超声波声强在1.1W/cm2时,表面氧化物的质量分数≤0.3%的钢制件,t=0.7min;表面氧化物的质量分数≤1.5%的钢制件,t=1min。
振子产生的超声波在酸洗液中传播时,离振子越远声强损失越大,再加上振子在工作中的发热造成的能量损失,在实际选型计算中可适当增加功率配置。
5.生物脱脂除油法
生物除油技术是利用生物化学原理,对油污化合物通过催化作用,激化和提高微生物细菌能级,加速氧化分解油污的烃类,使油污逐步转化为低分子化合物或分解为二氧化碳,是新一代碱性生物除油技术。其特点是钢丝表面的油污溶解在水体中后,在辅氧及催化剂的作用下,经微生物细菌分解,使有害的油污转化为无害污泥。生物除油后所排出的废水和污泥对海洋中的动植物均无害。
在脱脂过程中,传统的化学除油剂都有固定的使用寿命。由于钢制件表面所带入的皂化油脂在脱脂槽液中不断积累和皂化油脂不断地带入,除油效果随之下降,通常2~3周的时间,便需要沉淀清理脱脂液,并重新配制脱脂液。此外,脱脂后的废液和漂洗水进入循环水系统后,致使循环水水质恶化,水处理难度加大,使水体平衡受到破坏,水处理药剂对水处理设备的缓蚀阻垢性能降低,同时使原有浮在水中的微生物黏泥、灰尘、污垢等在管束内集起,形成沉积物,进而形成沉积物下腐蚀。如果循环水中漏入含有化学脱脂后的废水,循环水的水质处理成了循环水处理的棘手问题,而生物除油清洗剂是解决这一问题的有效措施。新一代碱性生物除油技术是通过生物除油剂及其配套的辅助设备解决以上问题。生物除油剂可以大大延长槽液的使用寿命,在许多使用厂家中,这些生物除油液都可以连续使用许多年而无需更换。传统除油工艺与生化除油工艺的槽液稳定对比如图3-2。

图3-2 传统除油工艺与生物除油工艺的槽液稳定性对比
(1)传统除油法 从图3-2(a)可以看出,传统除油是经过一段时间后,除油效果降低,添加碱性除油剂后,效果再次提高,呈高低峰值波浪形。
(2)生物除油法 从图3-2(b)可以看出其与传统工艺相比,生化除油工艺的槽液稳定性大大提高,不随时间延长除油效果下降,从而减少了换槽次数,提高了生产效率。
在生物除油系统里,细小的微生物能将复杂的有机分子分解成简单而无毒害的物质,如二氧化碳和水,故无需油水分离,也不用将油污排放到污水处理中心,从而大大减轻了废水处理的压力。与传统工艺相比,工作温度从原来70~90℃降低到40~55℃,节约能耗近60%,延长了更新时间,提高了生产效率。
二、脱脂清洗效果的检验
钢制件脱脂除油清洗后,清洁度的要求是根据钢制件的性质或加工工艺的要求来确定的。清洁度的检查方法一般采用3种方法,且比较简便可行。
1.目测法
用肉眼或借助放大镜观察清洗表面残存的污物程度及清净状态的方法称目测法。根据所用的清净方法及下一道进行的工艺处理项目,用棋盘测定板(棋盘格板为100个分度)评定清洁度,以格子的百分数表示之,或者用标准样件进行对比。
2.擦拭法
用清洁的绸布或滤纸在清洁后的表面擦拭,然后检查绸布或滤纸上的附着物。
3.水膜破裂法
水膜破裂法又叫水膜连续法。将清洗后的表面用水润湿,以表面水膜完整(连续)附着情况来确定清洁程度。水膜破裂法虽然较方便,而且有一定的高灵敏性,但在这样的情况下,可能出现较大的偏差。
4.不能发现表面存在的能被水润湿的污物
清洗介质中含有表面活性物质时,它能被金属表面或油脂表面吸附,因而有油污处也可被润湿。当使用化学脱脂剂去除工件表面的油脂时,应检查脱脂剂的总碱度和游离碱度。若使用强碱性脱脂液脱脂时日常应检验游离碱度,不定期检验总碱度。总碱度与游离碱度之比应小于2.5。脱脂液的含油量应控制在5g/L以下;对于弱碱性脱脂液,日常检测的总碱度一般控制在14~20点之间。
三、钢制件表面旧漆的去除
钢铁制件表面的漆膜,因涂装不良,或因周转运输造成破坏,或在使用过程中老化破坏,需要重新热镀锌时,应将旧漆去除。除旧漆常用的方法有机械法、火焰法和化学法。
1.机械法
机械法包括用手动和动力工具打磨、高压水冲刷及喷丸(砂)等方法,可以有效地清除旧漆。
2.火焰法
用煤油喷灯或氧乙炔火焰的灼烧漆膜,使其焦软、起泡,同时用刮刀铲清除。脱漆需要的时间短,但要注意防止钢铁工件的受热变形。
3.化学法
化学法是用化学试剂配成脱漆剂进行退漆的方法。常用的方法如下。
(1)碱液法 利用碱液强腐蚀作用,对漆膜渗透,溶胀及降解,破坏漆膜与钢铁材料间的附着力,使漆膜膨胀松软,并用铲刀进行清除,再用温水洗净。使用碱液脱除旧漆,一般使用的碱液为:NaOH 77%,NaCO3 10%,表面活性剂3%,其余为水,温度80℃以上。
(2)脱漆剂去除法 脱漆剂是能够溶解或胀漆膜的溶剂;主要由溶解力强的溶剂组成。现在市场上有很多较好地脱除旧漆的产品。使用脱漆剂,施工方便,可在常温下进行。一般情况下可把工件放在脱漆剂的水溶液中,浸泡1~2h,用刮刀刮除就可以了。一般的脱漆剂由苯8份、杂醇油3份、乙醇6份(质量份)组成。
四、钢制件表面酸洗除锈
在钢铁制件热浸镀锌中,常用的酸主要是盐酸和硫酸两种。
盐酸的分子式为HCl,纯HCl为无色、有强烈刺激气味的气体,其水溶液即为盐酸。工业盐酸中因含有少量的铁、氯等杂质,外观为微黄色透明溶液。按照GB 320—93规定,合格品含酸量应在≥31%,相当于358g/L,相对密度1.158浓盐酸在空气中发烟,在空气中浓度达到0.004%时即影响呼吸。盐酸能与许多金属反应,如铁、锌等放出氢气形成金属氧化物(与金属氧化物形成金属氯化物和水)。盐酸浓度与密度的对照见表4-3。钢铁表面因大气腐蚀产生的铁锈,一般是氢氧化铁与氢氧化亚铁,因高温而产生的氧化皮,则主要是四氧化三铁、三氧化二铁。铁的氧化物很容易与酸作用而被溶解。热浸镀锌酸洗工序中最常用的酸为硫酸和盐酸,其机理与反应方程如下。
①当采用盐酸溶液清除氧化铁皮时,其反应原理为:
(3-3)
(3-4)
(3-5)
②当采用硫酸溶液清除氧化铁皮时,其反应原理为:
(3-6)
(3-7)
(3-8)
硫酸与铁的反应式: (3-9)
盐酸与铁的反应式: (3-10)
通过酸洗靠以下几个作用来达到除锈的目的。
a.因酸溶液与铁的氧化物作用后生成了溶于水中的铁及亚铁盐酸盐(用硫酸时硫酸盐)或氧化物,从而使铁的氧化物除去这种过程为直接溶解作用。
b.当酸溶液与铁的氧化物作用时,酸溶液同时透过氧化铁皮的裂缝与钢基体起作用而生成了氢。由于氢的自由压力,会把氧化铁皮从钢基体上剥离下来,这种过程称为机械剥离作用,其化学反应式如下:
(3-11)
(3-12)
盐酸酸洗时,大约有33%的氧化铁皮是机械剥离作用去除的。用硫酸酸洗时,高达78%的氧化铁皮是由机械剥离作用去除的。
c.由于酸溶液与铁的氧化物作用后生成了氢气,经反过来会使氧化铁中的三氧化铁及四氧化铁还原成易溶于酸溶液中的一氧化铁,从而加速了酸洗的速度,这种过程称为还原过程。
在用盐酸酸洗时,盐酸溶液中:
(3-13)
(3-14)
(3-15)
在硫酸酸洗时,硫酸洗溶液中:
(3-16)
(3-17)
(3-18)
酸洗溶液的浓度及温度将直接影响着酸洗的速度与效果。一般情况下推荐使用浓度:盐酸为15%~20%,温度控制在25~35℃之间。硫酸最适宜浓度为25%(质量),温度一般加热到45~50℃,不宜超过70℃。而且还要加入适当的缓蚀剂若丁或硫脲。为了方便操作,利用波美计可以很方便地查找出盐酸的浓度,见表3-3。
表3-3 盐酸浓度与密度对照

在酸洗过程中,钢件基体不可避免地要与酸反应,反应过程中累积的铁盐能明显降低酸洗液的酸洗能力,减缓酸洗速度并使酸洗后的钢制件表面残渣增加,降低酸洗质量。所以在用硫酸作为酸洗剂时,硫酸溶液中的铁含量一般不大于60g/L,当铁含量超过80g/L、硫酸亚铁超过215g/L时,应更换酸洗液。当使用盐酸酸洗时,反应后生成了氯化铁及氯化亚铁,氯化铁是一种腐蚀剂,能促进酸洗过程,所以要获得较高的酸洗速度,可以在新盐酸溶液内加入一定量的旧盐酸。平常操作时,可向盐酸溶液槽中添加新盐酸。同时要控制酸洗溶液中铁盐的含量,当铁盐超过限度时,也会减慢酸洗速度。所不同的是氧化亚铁极易溶于水,一般铁盐含量在16g/L时可获得最高的酸洗速度。但当溶液中的铁含量超过允许值溶解度时,它会结晶出来而黏附在钢件表面上(一般情况下为2.3g/m2左右),因此一般把盐酸溶液中的铁盐含量限制在220~260g/L的范围内。
③采用盐酸酸洗的工艺一般为:盐酸溶液的初始浓度180~200g/L;盐酸溶液的最终浓度30g/L;氯化铁(铁盐)的最高含量120g/L;盐酸溶液的温度20~40℃;酸洗时间20~30min;缓蚀剂0.2%~0.4%;温度为室温。
④采用硫酸酸洗的工艺一般为:
硫酸溶液的初始浓度(d=1.84) 180~250g/L;
若丁 0.3~0.5g/L;
温度 35~50℃
⑤采用常温快速去除钢铁表面氧化皮复合酸酸洗工艺为(100ml溶液计算):盐酸(d=1.19)42ml;十二烷基硫酸钠0.1g;草酸0.5g;OP-10 0.1g;磷酸6.0ml;添加剂1.0ml(含氟无机物,可与Fe2+、Fe3+配合);温度室温。
在热浸镀锌酸洗工序中使用盐酸酸洗时,要注意和掌握以下几点。
a.盐酸使用浓度。通常控制在8%~20%之间为宜,在室温情况下,铁盐含量在控制在20g/L一下,当铁盐达到150~200g/L时,虽然酸槽里含有一定量的游离酸还可以使用一段时间,但除非升高温度,否则酸洗速度将大大减缓,此时,不能再添加新酸了,只能将其全部处理掉。
b.酸洗液的温度与酸洗时间的关系。在室温下的盐酸溶液中,酸洗时间与质量分数之间的关系如图3-3,由图3-3可见随着酸洗液质量分数的提高,酸洗时间缩短。

图3-3 室温下盐酸质量分数与酸洗时间的关系曲线
实际上酸洗液温度对酸洗时间有显著影响。如图3-4所示,20℃、40℃以及60℃下,酸洗液平均酸洗时间的比例大约为12:3:1。

图3-4 酸洗液温度与酸洗时间的关系曲线
实际上,盐酸在低于15℃时的酸洗速度是很慢的。合适的酸洗温度是18~21℃。氧化铁皮和酸之间的化学反应能产生足够的热量来保持酸液温度。但是,在天气冷时经过一晚上之后酸液就会冷却到15℃以下,假如不供热,则需要很长时间才能达到合适的酸洗操作温度。因此,为了保持足够的酸洗速度,建议对酸洗液预先加热。最简单的方法是直接通蒸汽进行加热,电加热器也可用来加热盐酸,但由于是用于酸性条件下,需要用塑料王或石英套管保护起来。
提高酸液温度可以提高酸洗速度,但不能为提高酸洗速度而随意提高酸液温度。因为在较低的温度时盐酸丁蒸汽压已经相当大,并且随温度升高还要继续迅速增加,产生大量的酸蒸气而影响环境,同时增加酸的消耗量,所以盐酸洗一般应该是在室温下进行。可以延长酸洗时间来达到酸洗效果。
实践证明:酸洗速度快慢不仅取决于酸洗液的浓度,而重要的是决定于FeCl2在该盐酸浓度下的饱和程度。一定的盐酸浓度在相同温度下具有一定的FeCl2饱和度。当盐酸浓度达到10%时,FeCl2饱和度为48%;当浓度达到31%时,FeCl2饱和度只有5.5%,同时FeCl2饱和度随着温度上升而增大。在生产中对盐酸的浓度范围控制得过宽、过窄对生产都带来一定的难度。推荐使用盐酸浓度在8%~13%、酸液相对密度1.20~1.35。FeCl2含量高(可用盐酸相对密度表示),则盐酸浓度可相应取低值;FeCl2含量低,盐酸浓度可取高值。
酸洗的目的在于除锈,而不能腐蚀钢铁基体。过量的酸洗会使钢制件表面变得粗糙,从而影响热镀锌质量。故酸洗时通常加入酸液抑制缓蚀剂。酸液抑制缓蚀剂是一种当它以适当的含量和形式存在于介质中时,可以防止或减缓钢铁制件在介质中腐蚀的化学物质或复合物质。在腐蚀环境中,添加少量的这种物质,便可以有效地抑制钢制件的腐蚀。
酸洗溶液中的抑制缓蚀剂,一般要求具备下列条件:在高温高浓度溶液中是稳定的,抑制酸雾挥发、缓蚀效果好;不影响钢制件表面的酸洗速度;配方简便,含量易于控制,废液易于处理;价格便宜。几种常用的酸洗缓蚀剂见表3-4。
表3-4 几种常用的酸洗缓蚀剂

缓蚀剂的用量取决于钢制件的材质、酸洗液的组成及操作浓度和温度,以及去除物的性质。在一定范围内,缓蚀效率随含量增加而提高,但达到一定数值后,含量增加,效率不再提高,各种缓蚀剂在各种酸洗液中都有一个含量极限,一般使用的质量分数以0.5%~1.0%为宜。酸洗液温度提高,缓蚀剂的缓蚀效率下降,甚至失效。酸洗液的使用时间增长,缓蚀剂的缓蚀效果也会下降,因此,需要定期向酸洗液中补加缓蚀剂,使其缓蚀效率维持在工艺要求的水平上。
在钢制件热镀锌生产中,在配置新盐酸溶液时,最好加入一些旧盐酸溶液,使其氧化铁的含量在10g/L左右,这样可以加快酸洗速度;同时为提高酸洗速度和防止酸雾逸出可添加酸雾抑制剂。最常用的酸雾抑制缓蚀剂的含量一般为:葡萄糖酸钠0.42g/L,十二烷基硫酸钠0.034g/L,草酸0.5%(质量)、磷酸6%(质量),乌洛托品0.5g/L,OP-10 0.035g/L,1,4-丁炔二醇0.30g/L。
⑥酸洗液的检验与控制。
为了充分的利用酸洗溶液,需要严格控制其成分。酸含量和铁盐含量的测定是简单的,只需要少量的仪器:小玻璃斗、25mL量筒、250mL量筒、50mL滴管、250mL的锥形瓶、甲基橙试剂、0.5mol/L碳酸钠标准液、测量范围在1.0~1.3g/mL的密度计和滤纸。
在待测量酸洗池中用烧杯取酸液样,过滤到一个25mL的量筒中满刻度。然后倒入一个250mL的量筒里,加清水至250mL满刻度并充分搅匀。再用另一个25mL量筒取此稀释液25mL,倒入250mL的锥形瓶里,加入数滴甲基橙试剂,再用滴管逐步滴加入0.5ml/L碳酸钠标准液,随时搅拌。测定需要多少毫升碳酸钠标准液能使试剂的颜色从红变到黄。假如需要xmL的0.5mol/L碳酸钠,则溶液中含有x×7.3g/L HCl。
测出了酸洗液的质量浓度后,再用密度计测出溶液的质量浓度后,再用密度计测出溶液密度,则可根据图3-5求得酸液中铁的含量。具体方法是,在图3-5中用一把尺子将左边表示密度的线和右边表示酸含量的线相连,就可以在中间线上读出铁的含量。

图3-5 室温下盐酸溶液中的盐酸质量浓度、密度与铁含量对应关系
在酸洗液配制时应根据生产工艺条件,计算出酸洗液的浓度,根据盐酸或硫酸的浓度计算出添加水量。配酸时,应将酸倒入水中,以防止酸液飞溅情况的发生。
酸洗液中铁盐的含量应控制在一定范围内,当使用盐酸作为除锈剂时,铁盐含量限200~250g/L范围。当使用硫酸时,铁盐含量应限制在180~250g/L之间为宜。除去废盐酸中的铁盐,较为经济的方法就是采用资源化治理法——硫酸置换法,使废盐酸经过再生处理得到回收利用。
在实际生产中,在没有化验设备的情况下,需要随时掌握盐酸的浓度,可以利用盐酸的密度与浓度的关系,通过查表的方法便可以查到盐酸的浓度,可以适时调整在线酸洗池的浓度,以适应生产。
五、酸洗操作注意事项
1.控制酸洗液浓度
在酸洗过程中水分会逐渐挥发,因此,应随时加水调节浓度,使酸洗液浓度控制在工艺范围之内,以免酸液浓度过高造成钢制件的过酸洗引起的腐蚀。
2.保持酸洗液清洁
酸洗过程中,如带入碱及其他污物,酸洗液成分将逐渐改变,影响酸洗效率。因此,为获得满意的酸洗效果,应定期检查、分析、更换酸液,并保持酸液适当的清洁。
3.控制温度
温度应按工艺规范要求控制。温度过低会造成酸洗速度大大降低,影响生产效率。提高温度可以加快酸洗速度,但对钢制件和设备的腐蚀也相应地增加。
4.酸洗方法及酸液的维护
酸洗一般都需要搅拌。酸洗过程中使钢管上下移动2~3次,变换一下钢管和酸液的接触面可加快酸洗速度。酸池内用压缩空气进行强力搅拌并不合适,这样会造成过多的酸雾、气的产生。
(1)定期清除酸洗池中污泥 随着除锈过程的进行,酸洗池将逐步沉积污泥,淤塞加热管和其他控制装置,应定期清除。
(2)适当控制时间 在完全出去锈迹的前提下,酸洗时间应尽可能短,以减少金属的腐蚀和氢脆的倾向。
(3)注意操作安全 除锈酸洗液,一般都具有很强的腐蚀性,操作中应避免酸液飞溅到皮肤或衣物上,以免烧伤皮肤或破坏衣物。
(4)酸洗场地应有排风装置 酸洗时常产生含酸气体,为减少含酸气体对设备的腐蚀和对人体的危害,酸洗场地应布置良好的通风或排气设备。
六、酸洗液常用的缓蚀剂
酸洗的目的在于除锈,而不能腐蚀钢的基体。过量的酸洗会使钢铁表面变得粗糙,从而影响热镀锌的质量。故酸洗时通常需要加入缓蚀剂。缓蚀剂是一种当它以适当的含量和形式存在于介质中时,可以防止或减缓钢铁在介质中腐蚀的化学物质或复合物质。在腐蚀环境中,添加这种少量的物质,便可以有效地抑制钢铁材料的腐蚀。
1.酸洗液中的缓蚀剂
酸洗液中的缓蚀剂一般要求具有下列的条件:在高温、高浓度溶液中是稳定的,缓蚀效果好;不影响钢铁制件的酸洗速度;缓蚀剂配制方便,含量易于控制,废液易于处理,价格便宜。一般常用的配剂为:若丁0.2%~0.3%,硫脲0.1%~0.3%,乌洛托品0.3%~0.5%。这几种原料缓蚀效率达到70%以上。
2.缓蚀剂抑制腐蚀的作用
缓蚀剂抑制腐蚀的作用是有选择的,它与腐蚀介质的性质、温度、流动状态、被保护金属的性质以及缓蚀剂的种类、含量等都有密切的关系。某些条件的改变,都可能引起缓蚀效果的改变。因此,需要了解缓蚀剂的作用及缓蚀效果的测试方法,以便正确地选择和运用缓蚀剂。缓蚀剂的缓蚀效率可用失重法简便的测定。此法是通过比较在同一介质中相同的条件下,酸洗液中添加和不添加缓蚀剂时试样的失重,从而求出缓蚀效率,即:
缓蚀效率(%)=(W1-W2)/W1×100% (3-19)
式中 W1——未加缓蚀剂时试样的失重量,g/(m2·h);
W2——加缓蚀剂时试样的失重量,g/(m2·h)。
缓蚀剂的用量取决于被酸洗制件的材质、酸洗液的组成及操作的浓度和温度以及被除物的性质。在一定范围内,缓蚀效率随缓蚀剂的含量增加而提高,但达到一定数值后,含量增加,效率不再提高,在各种酸溶液中都有一个含量的极限,一般使用的质量分数以0.5%~1.0%为宜。酸洗温度提高,缓蚀剂的缓蚀效率下降,甚至失效。每种缓蚀剂都有一个使用温度范围。酸洗液使用时间增长,缓蚀剂的缓蚀效率也会下降,因此,因此需要定期向酸洗液中补加缓蚀剂,使其缓蚀效率维持在工艺要求的水平上。
七、水漂洗的方法
碱洗、酸洗之后的水洗工序主要是用来清洗掉工件经碱洗、酸洗后黏附在工件上的杂质,以防止交叉污染。带进下一道工序助镀剂当中。因此,水洗可以说是成功前处理的一个重要步骤。实际中水洗工艺常常被忽视,可以看到酸洗后不水洗,或者碱洗、酸洗后共用一个水洗槽;或者水洗槽设计不合理,清水从水洗槽一端上面注入,又从另一端上面溢出,降低了清洗效果,并造成了一定浪费。清洗水的温度一般控制在25℃左右为好。并应该控制pH值。一般进水管水口安装在水槽的中下部,便于净化水质。
水漂洗过程主要有以下几方面的积极意义:一是防止碱、酸、助镀剂反应液交叉污染;二是钢铁制品自身品质的要求;三是水洗技术的好坏也影响到表面处理用药品的消耗量。如脱脂液没有漂洗净,就进入酸洗槽,这样最终导致盐酸槽内的盐酸有效浓度的降低;酸洗液没有漂洗干净,就带入助镀溶剂,将使助镀溶剂酸度升高,加大铁离子的溶解度,由钢制品进锌液后,将使锌液变为黏稠,增大锌渣的生成量。此外,可以实现节约用水。如何提高水洗效率、改善水洗效果,是热镀锌前处理的一个重要课题。
漂洗用的水洗槽及附带装置,目前通用的材质使用玻璃钢或PVC等有机材料的居多。而热水槽需使用耐热PVC材质。水洗槽直接给水或喷淋给水时通过配备水泵确保给水量和压力。也有用空气强化搅拌水,增强漂洗能力。水洗方式有以下两种方式。
1.浸渍水洗
钢制品直接在清洗水中通过,使钢制品表面上附带的残留的碱、酸性液体浓度得到稀释。
2.喷淋水洗
基本上是流水洗的方式,喷淋水洗能够冲洗掉钢制品上的碱、酸液同时也能够稀释掉钢制件上的碱、酸液。与浸渍洗净相比,用少量的水可以得到较好的洗净效果。强化水洗的措施,采取用泵循环水,通过循环泵实现槽内液体的循环,促进水洗水的流动,也促进了水漂洗效果。
为了节约用水,减少碱、酸废水排放,按照酸和碱中和的原理,可以把酸洗后的漂洗水引到碱洗脱脂后的水漂洗,既可以减少循环水的用量,又可以中和碱洗脱脂后的漂洗水,减少钢制品表面的残留碱液。最后集中到一个中和池内自然中和,当酸、碱的pH达到平衡时,符合排放标准时进行排放。
碱、酸洗后采用热水洗,主要是考虑能很好地冲洗、溶解掉黏附在钢制品表面残留的碱液和酸洗后的铁盐,减少带入下道工序(助镀)中的铁盐。考虑到需要对清水加热到一定温度(>25℃),才能起到快速清除铁盐的效果。从节约能源角度考虑,可以将钢丝热镀锌后水冷却池中水引进到碱洗、酸洗后的漂洗池,起到温水清洗的作用。
在国内一部分相关企业中,采用了清洗水循环使用的做法,即把酸洗后的水槽安装导电测量仪,监视水的酸性程度,当酸度达到一定数值时,电磁阀会自动打开,把水抽到碱洗后的清洗槽里,同时注入清水到酸洗后的清洗槽内,这样水的耗量可减至最低,又能达到排污少、耗水低的效果。