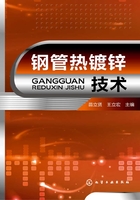
第六节 锌液温度和浸渍时间对镀锌层的影响
一、热镀锌温度的范围
(一)经典理论浸镀温度范围
在热镀锌过程中,锌液温度和浸锌时间是影响镀层的重要因素。通常是用热镀锌时的铁损作为铁-锌反应速度的参数。铁损是指铁与锌反应形成合金层中的铁和锌渣中铁的总量。
由于锌液温度的变化,钢基体和锌液之间的物理化学过程将发生较大的变化,因而也影响了合金层的结构。英国学者Hershman.A.A在1967年评述当时热镀锌研究成果时,主要根据工业纯铁和被铁饱和的锌液间的反应,并按铁损和镀锌时间的变化,划分成如下3个温度范围。
1.低温抛物线范围(430~480℃)
在这一温度范围时,铁损(ΔW)按抛物线规律随浸锌时间(t)变化,表示为ΔW=At1/2,式中,A为取决于温度的常数。在这一温度范围内,所生成的合金层连续而致密的,其中含有Γ、δ1、ζ、η相层,它们在这一温度范围内是稳定的。
2.直线范围(480~530℃)
当锌液温度提高到480℃以上时,铁和锌的反应式形式发生变化。在这一温度范围内,当浸镀时间较长时,铁损与时间是直线规律,其关系式表示如下:ΔW=Bt,式中B为常数,在温度超过480℃时,铁损和时间呈直线关系,如图2-17、图2-18。

图2-17 锌液温度对铁的损失量关系

图2-18 铁损与时间的关系
当温度超过480℃时,ζ相形成速度很快,即铁-锌反应速度加快导致合金层迅速增加。当达到500℃时,铁损增至最大值,超过500℃后,铁在锌液中的重量损失又开始下降。
20世纪80年代,在中国内地的热镀锌行业,如铁塔制造及钢管的热镀锌,曾经盛行采用490~510℃的浸镀温度,浸镀时间通常不超过1.5min,可得到较薄的镀锌层,并具有很高的生产效率。存在的问题主要是铁质锌锅使用寿命短。若浸镀时间稍微延长则镀锌层增厚。但是对使用陶瓷锌锅,浸镀时间较短时,此温度范围仍可以采用。
3.高温抛物线范围(530℃以上)
当锌液温度上升至530~560℃时,反应又恢复为抛物线形。但抛物线常数A的数值随温度的变化而变化。A值变化的原因,一般认为合金层中有的部分发生破裂。破裂程度不同,因而曲线的形状也不相同。通常把530~560℃温度范围内的镀锌称为高温热镀锌。从铁-锌合金二元合金状态图中可知,镀锌温度超过530℃时,ζ相消失而δ相是稳定的,δ相的形成和生长变得很慢。实际上从500℃开始,δ相的生成就受到影响,随着温度的升高,δ相往锌液中的溶解加快,在此温度下硅对铁锌合金反应不利影响大为降低,形成含极少量ζ相和较薄δ相的合金层;在离开锌液后δ相会继续生长,最终工件表面形成δ+ζ的双相结构。镀层表面呈浅灰色,若要获得光亮表面镀层,可将锌液中的铝含量增加到0.03%~0.05%之间。高温镀锌时,锌液对铁的腐蚀加快,生产中必须采用陶瓷或其他耐火材料锌锅,最好采用内加热、顶部加热或感应加热。高温镀锌流动性好,对去除余锌极为有利,所以在螺纹件及玛钢件的热镀锌生产中得到广泛的应用。
以上3种反应类型主要是根据工业纯铁与锌液的反应划分的,在多数情况下,当铁与锌液中含有合金元素时,会影响反应的程度,但对反应的基本类型没有影响。
(二)实际生产浸镀温度范围
1.常规热镀锌温度(440~465℃)
经验表明,大多数情况下在445~465℃的温度范围内镀锌能够获得满意的效果,在此范围内提高温度可增加锌液的流动性,改善锌液的回流,提高镀层质量;此外,可缩短镀锌时间,提高生产效率。如果由于钢材硅含量的影响,镀层质量不理想时,可采用下限温度。
2.低温热镀锌(435~445℃)
对于含硅镇静钢,为了克服“灰色镀层”的形成,除了采用添加锌-镍或多元锌-铝-锡-镍中间合金的方法外,采用低温镀锌工艺也是有效的方法,镀锌的最低温度应以工件提出锌液后,锌液能顺利地从工件上下来为准。低温镀锌可以抑制铁-锌合金的形成,并减少锌灰或锌渣量,并能保证锌锅的安全和节约能源。生产实践证明:锌液温度降低20℃(比如从470℃降到450℃),浸镀所产生的锌渣量将减少为一半。目前低温镀锌已经得到较多的应用。低温镀锌的生产效率低于常规温度镀锌。
3.超低温热浸镀锌(425~435℃)
生产实际证明,对解决高硅、锰碳素结构钢(如Q345、16Mn等)浸镀出现的灰色镀层或色差,可以进一步降低镀锌温度。在这个温度范围内,一般较适合电缆桥架和太阳能设备的支架等薄件的镀锌工艺。除此之外的其他镀件采用超低温镀锌,会产生以下问题。
①镀锌温度偏低锌液流动性变差,当环境温度较低时,(如车间内温度低于5℃以下,锌液面此时温度在190~200℃之间),工件提出锌液面后,锌液几乎就不能流淌,镀锌后的纯锌层厚度明显增加。
②当工件一次进入量较大(或工件吨位很大),锌液温度会有所降低,要适当延长浸镀时间,这样势必降低生产效率。为避免这种情况,必须保证锌锅有足够的熔锌量,一般应为生产量(t/h)或最大件质量(t)的60倍以上。此外,为了改善锌液在低温状态下的流动性,加入少量的五元锌-铝-锡-铋-混合稀土合金可以取得较为满意的效果。
二、热镀锌温度对镀层的影响
对于热镀锌温度,国内外专家均认为保持在430~460℃的范围内最好,当温度升高超过475℃时,会使不良的铁-锌中间金属化合物的形成速度增加。科学试验及生产实践证明,由于升高锌液温度会促使合金相ζ相厚度的增加,使镀锌层的塑性变差,所以当锌液温度变动时,各相层厚度比例也相应地发生变化,一般来说,低碳钢件在450℃的锌液中浸4min后,所得的镀锌层组织中ζ相和δ1相厚度基本一样。但是,一旦温度提高到480℃,同样浸4min,则所获得的δ1相对减少,而脆性ζ相却增长几倍;外层的纯锌层η相亦因温度太高、流动性较好以及铁-锌间扩散的加剧而使纯锌层减薄了。特别在495℃时生成了特别明显的二次ζ相结晶,但是一旦达到500℃时,则又完全消失了。由于ζ相具有较强的脆性,所以在做冷弯试验以及因需要在镀锌后进行折弯时,纯锌层会很容易脱落下来或开裂。故在实际镀锌生产中,一般采用440~465℃之间的温度。采用这样一个温度范围还因为,在这范围内无论从钢件的铁溶解量以及锌锅的铁的溶解量均较低,这对于锌渣的产生量减少有很大的好处。图2-18所表示的是在同样的时间内,温度越高,铁在锌液中的溶解速率也越高。
从图2-17中可以看出,在锌液温度与铁损失量的关系曲线中,440~460℃范围铁损失量基本相同,是处在最低的极限范围,如果当锌液温度增加到470℃时,铁的损失量略有增加,但还是很少影响,一旦锌液温度升到480~500℃时,铁的重量损失呈直线形式出现,这时属于铁损失量最不利的情况,换句话说,这时对钢质镀锌的腐蚀最厉害,锌锅使用寿命最短。对镀锌钢件来讲,铁-锌合金层较厚,不影响使用寿命。大部分黏附在钢铁表面上成为镀锌层的一个组成部分,余下的另一部分便从镀层脱落而进入锌液中去,造成了锌渣增加,对锌耗及镀锌层表面质量有不良的影响,由于以上原因,故一般都限制了锌液的温度。
三、热镀锌时间对镀层的影响
图2-18所示为在相同的锌液温度下,浸锌时间与铁损的对应关系,时间越长工件的铁损越多。试验表明,用不同的浸锌时间对相同的厚度钢板进行热镀锌时,可以发现浸锌时间越长,钢板上附着的锌量比浸锌时间短的要多得多。浸锌时间长的铁-锌合金层厚,脆而挠性差,有时表面呈灰黑色;浸锌时间短的铁-锌合金层薄,挠性好,有些因时间过短,合金层不能形成,只在钢板上面形成一层薄锌,这种镀层很容易从钢板表面上脱落下来。
同样,在相同的浸锌时间下,当锌液温度较高时,镀锌钢板上附着锌量就多,铁-锌合金层就厚,脆而挠性差,表面有时亦可能出现灰暗色;相反当锌液温度较低时,镀锌钢件上的附着量就较少,铁-锌合金层就薄,纯锌层较厚,使其挠性好;如果锌液温度太低时,铁-锌合金层不能形成,只在钢件表面上附着一层纯锌层,也容易脱落,所以锌液温度太低或太高都不好。
总之,当锌液温度不变时,以较长的浸锌时间可获得较厚的镀锌层;反之,当锌液温度较高的时候,浸锌时间虽然较短,所获得的镀锌层与浸锌时间较长是一样的。
一般情况下,当确定对某一个品种钢制品镀锌时,先确定镀锌液的温度,根据用户对产品镀锌层厚度的要求而事先确定大约浸锌时间,以获得合适的镀锌层厚度。
例如,在浸锌温度为450℃,钢的成分为C 0.008%、Mn 0.40%、Si 0.006%、P 0.021%和Cu 0.02%的条件下,γ相的厚度达到正常的0.004mm时,需要不到1min的时间。对于工业纯铁,需要30~45s。ζ相起初生长得很快,超过了δ1相。在大约90min后,δ1相的生长速度就接近了ζ相,这表明了Fe通过γ相和δ1相的扩散比通过ζ相的扩散来得快。所以,当ζ相长大以后,锌必须经过更长的路径进行扩散,于是ζ相生长就落后于δ1相的生长,因此,在正常镀锌时(浸镀6~20s)ζ相最厚。这一点对镀层的塑性极其重要,因为此ζ相是脆性的单斜晶结构,ζ相越厚,镀锌层的塑性越差。所以,在热镀锌时,尽量缩短浸锌时间,可以减少ζ相的厚度,从而使镀锌层的塑性得到改善。
综上所述,锌液温度与浸锌时间对钢制品的铁损影响因素较大。现将国外学者的研究结果归纳如下(表2-18)。
表2-18 浸锌温度与时间t对铁损ΔW的影响

①当采用纯铁(阿姆克铁)时的数据,当采用工业纯铁含极微量硅(0.002%)时,会使曲线左移,出现括号内的数据。
由此可以看出,上述理论仅是在平衡状态下出现的情况(浸渍时间为1h,铁在锌液中的含量应达到规定的数值)。而实际上,热浸镀锌的时间大都很短,除了截面厚度较大的钢结构件(可达10mm以上)以外,一般浸镀时间都是几分钟(有时是以秒计),此时对镀件而言,铁损情况与表2-18会有差异;而对锌锅的腐蚀过程,具有较强的针对性。所以普遍认为锌液温度超过480℃,锌对铁的浸蚀过程加快,将浸镀温度控制在460℃以内,这对于延长钢制锌锅的使用寿命是十分必要的。
1.影响构件浸镀时间的因素
①浸锌温度越高,工件达到锌液温度的时间越短,工件表面上的助镀剂和锌液反应能较快完成,浸镀时间可缩短。
②工件有效厚度的影响。工件有效厚度(δ)越大热透时间增长,则需要较长的浸镀时间,举例来说,δ=6mm,需要3~4min;δ=10mm,需要5~6min;δ=20mm,需要10min或更长时间。
③一次浸镀工件总量的影响,一般情况下,每投入锌锅1t工件,锌液温度约降低1.5℃(指容锌量100t左右的锌锅)。如果投入工件吨位较大,锌液温度明显降低,此时,就必须延长浸镀时间。
④工件复杂程度的影响。如果形状简单(如型钢、板件、杆状工件),锌灰容易浮出液面,浸锌时间就短;如果形状复杂,就需要反复提动工件,浸锌时间就适当延长。
2.浸镀时间确定原则
①一般来说,把工件放入锌锅中,直到锌液面的“沸腾”现象停止,锌灰充分返出液面,即应毫不耽误地进行打灰,取出工件。对镇静钢而言,镀层厚度与浸锌时间成正比,因此浸镀时间必须尽量缩短。
②在有些情况下,正常浸镀后,镀层厚度并未达到国家标准规定的最低要求,此时,必须适当延长浸镀时间。
③尽量减少工件之间浸镀时间上的差异,以减少镀件之间或一个工件的不同部位的镀层厚度的差异。
四、镀锌温度对合金层成长速率的影响
关于镀锌温度对铁-锌合金层成长速率的影响问题的论述,在过去的镀锌技术文献中给予讨论的较少,本节在此引用两个经典曲线(图2-19、图2-20)。图2-19是由Proskurkin等学者在1975年给出的,它是铁在锌液呈饱和状态下(工业纯铁在锌液中保持2h),其合金层生长速率与锌液温度的关系。这与以上所述的温度与铁损的关系是一致的。但是,当浸镀时间较短时与该图的差别很大,图2-20为2min浸镀的情况。如果钢中硅含量较高,甚至可能出现温度增高、镀层总厚度反而减少的情况(图2-20)。从图2-20中可以看出,从450℃开始ζ相的厚度减少,到480℃ζ相消失,δ相厚度也随之降低,此时镀层由η相、较厚的δ相及Γ相组成。镀层总厚度随着温度的升高反而呈下降趋势,表2-19为实践中测出的数据。

图2-19 合金层生长速率与镀锌温度的关系(浸入时间为2h)

图2-20 锌液温度与合金层各相层厚度的关系(浸入时间为2min)
表2-19 镇静钢浸镀温度、时间与锌镀层总厚度的关系

图2-21所示为不同锌液温度下硅含量对合金镀层厚度的影响。从中可以看出,当钢中的硅含量增加到0.10%时,520℃下浸镀的锌层厚度低于460℃浸镀的厚度,这与表2-19所给出的数据是一致的。

图2-21 不同锌液温度下硅含量对合金镀层厚度的影响(纯锌,浸镀15min)
从表2-19中还可以看出,当浸镀时间延长到2min以上时,则随浸镀温度的升高,镀层厚度明显增厚。这是因为在短时间内,当浸镀温度达到490℃时,ζ相层在锌液中的溶解加速,ζ相层呈现不完整状态,从而使ζ相晶核的生成与相层的成长减缓。此时,锌液的流动性也提高了,所以合金层厚度与纯锌层厚度都呈下降趋势;如果继续延长浸镀时间就会发生以下变化:ζ相层全部溶解,δ相层可以直接从锌液中获取锌原子,从而δ相层得以快速增长,铁-锌合金层厚度随时间的延长继续增加。
通过以上分析可以看出,浸镀温度与时间对合金层厚度的影响较为复杂。但是对铁损的影响较为简单。对于镇静钢来说,延长浸镀时间对铁损和镀层厚度的增加程度就更为明显了。故在生产实践中,应当尽量缩短浸镀时间。