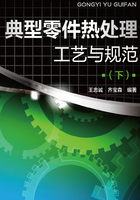
1.6 汽车齿轮的热处理工艺与规范
(1)汽车齿轮的工作条件和性能要求
汽车齿轮的种类较多,其中汽车减速器行星齿轮和半轴齿轮,在服役过程中,其承担着改变速度、输出扭矩、驱动车辆行驶等作用,因此齿轮在工作时,轮齿承受着很大的弯曲应力和接触应力,周期性作用于每一个齿上,同时承受重复交变应力的作用。另外,齿轮在传递扭矩或相对滚动过程中,会发生相对的滑动而产生摩擦作用。汽车、拖拉机齿轮的工作条件与一般的机械齿轮、机床齿轮相比,其服役环境差,对于耐磨性、疲劳强度、心部强度和冲击韧性等方面要求比机床齿轮高,因此,在材料的选用上,多推荐低合金渗碳钢,例如20CrMnTi、20Cr、20Mn2B、18CrMnTi、12Cr2Ni4A、20Cr2Ni4A等,图1-104为汽车变速箱齿轮的形状。

图1-104 汽车变速箱齿轮
汽车齿轮在多种应力的作用下,其失效或损坏的形式有齿根损坏(包括疲劳断裂和冲击折断)和齿面疲劳损坏(齿面的剥落、硬化层的剥落以及过度磨损和咬合),因此要求齿轮具有以下性能:①高的弯曲疲劳强度和接触疲劳强度;②齿面有高的硬度以及良好的耐磨性;③齿轮心部具有足够的强度和韧性;④提高精度以及低的传动噪声。
(2)汽车齿轮的机械加工工艺流程
目前齿轮的毛坯锻造已经广泛推广了精锻制造技术,其精锻工艺流程为:棒料切料→中频加热→热精锻→去飞边→余热退火→抛丸处理→切削加工→渗碳或碳氮共渗、淬火、回火→磨削加工。选用的材料为20CrMnTiH,其中余热退火是指将毛坯件冷却到600~700℃,保温一段时间后空冷,以获得珠光体+铁素体的组织,基体硬度在156~221HBW。
(3)汽车齿轮的热处理工艺
①技术要求、渗碳 (或共渗)层深1.0~1.3mm,碳化物为1~5级,马氏体、残余奥氏体为1~5级,齿轮表面与心部的硬度分别为58~63HRC和30~40HRC。
②齿轮的热处理工艺 齿轮的渗碳或碳氮共渗、淬火和回火是在密封的气体渗碳多用炉上进行,采用上述流程发现部分齿轮的淬火组织为粗大的马氏体,残余奥氏体较多,甚至出现个别马氏体组织超级缺陷,直接影响到其使用寿命。资料介绍,出现该缺陷的原因在于余热退火组织不良,导致马氏体组织粗大超级等,因此应进行再加热淬火,其目的是通过再加热调节那些影响晶粒度、残余奥氏体和碳化物等材料强度的主要因素,使齿轮获得良好的力学性能。该工艺比渗碳后降温直接淬火更能细化组织,改善心部和渗层组织。
汽车齿轮的热处理工艺与一般机床齿轮、机械齿轮的工艺相似,通常齿轮渗碳的热处理和工艺流程为:
在60~70℃清洗剂中除油→920℃渗碳、扩散→900℃预冷→缓冷至600℃以下→在850℃的保护性气氛中加热并保温120min→淬火→60~70℃的清洗剂中除油→在180~200℃回火炉内保温120min→进行30min的抛丸清理→成品检验。
而进行碳氮共渗的齿轮则是在共渗结束后直接进行淬火冷却,随后采用低温回火的热处理工艺[(180~220)℃×(2~3)h],其热处理技术要求同渗碳工艺。
根据齿轮渗碳或碳氮共渗后一般不进行直接淬火,在生产过程中一般有以下几种冷却方式。
a.空冷 多用于气体或盐浴渗碳(或碳氮共渗),应降温出炉,增加冷却速度,减少脱碳倾向。
b.冷却井或坑中冷却 为四周盘有蛇形管通水冷却的带盖容器,向其中通入保护气或加入煤油。
c.在700℃等温盐浴中保温后空冷 多用于盐浴渗碳或碳氮共渗,可减少齿面的脱碳。
d.在罐内冷却 多用于固体渗碳。
e.在缓冷坑中冷却或油冷 对于20CrMnMo、20CrNi3钢采用此冷却方式。
采用气体渗碳的工艺参数温度为920~940℃。对于要求渗碳层浅的齿轮,渗层为0.35~0.65mm时,工艺温度为870~890℃;一般渗层为0.65~0.85mm时,工艺温度为890~910℃;当渗层为0.8~1.0mm时,工艺温度为910~930℃。不同温度下渗层深度与渗碳时间的关系见表1-81。
表1-81 不同渗碳温度下齿轮渗层、温度和时间的关系

典型齿轮的渗碳工艺曲线见图1-105。

图1-105 20CrMnTi钢变速箱齿轮的低滴量气体渗碳工艺曲线
(4)汽车齿轮的热处理技术分析与实施要点
①首先应该明确高应力作用下的汽车齿轮选材与热处理工艺的关系,应当指出,对不同服役条件下的齿轮而言,应对材料和热处理后的性能进行具体的分析,在材料确定的前提下,选择最佳的热处理工艺,具体见表1-82。
表1-82 高应力作用下的汽车齿轮选材与热处理工艺的关系

一般而言,汽车用齿轮采用渗碳淬火强化,但淬火后带来极大变形,而感应淬火则克服了该缺点,而氮化齿轮在变形上,则具有更明显的优势。三者的材料是有一定区别的,应具体分析,淬火和回火后的齿轮表面淬硬层为中碳回火马氏体,齿面具有高的硬度、高的耐磨性、高的疲劳强度和良好的韧性等,可确保使用过程中能够承受较大的弯曲应力和冲击力的作用。可以看出汽车齿轮的服役条件大多为第一种类型,即选用低合金钢或低碳钢进行渗碳或碳氮共渗处理,以满足其工作需要。
②汽车齿轮的淬火处理有利于提高残余压应力,正确的磨削工艺并不改变残余应力的分布,但过多的摩擦热会导致次表层产生高的压应力。磨削热容易造成表面发热和冷却液的急冷而引入了新的应力,到热量过高时,造成表面过回火,使回火马氏体进一步分解,比容减小,导致表面产生拉伸残余应力,直接影响到齿轮的使用寿命,因此执行合理的磨削工艺是至关重要的。
③渗碳齿轮热处理后出现磨削开裂的原因有很多,应进行正确分析,一方面同磨削工艺不当或磨料不良、渗碳层过厚、有网状碳化物、残余奥氏体过多等有关,多半与齿轮的热处理工艺和选材不当有关,同时还与冶金、冷加工和热加工等有一定的关系。磨削裂纹的特征呈网络状、放射状和分散条状等,与磨削方向垂直,横向剖开后的裂纹分布于表层中并逐渐消失。因此应严格执行渗碳工艺和热处理技术要求,同时确保磨削参数的合理和规范。
④齿轮余热退火后获得的金相组织为片状珠光体、块状铁素体,部分晶粒局部粗大,因此其转变产物如马氏体、残余奥氏体以及非马氏体组织也将粗化。而采用渗碳后再加热淬火则可以通过再加热调节影响晶粒度、残余奥氏体和碳化物等材料强度的主要因素,与渗碳后降温直接淬火相比,细化了晶粒,改善了心部和渗层组织,故齿轮获得良好的力学性能。
⑤汽车齿轮进行气体渗碳的质量很大程度上需要热处理设备来保证,其炉内温度和碳势的进度、炉内温度和气氛的均匀性、淬火油搅拌和循环等,对渗碳和热处理后的质量有重要影响,因此应综合以上几个方面重点考虑,确保满足其要求。如有条件可尝试新的齿轮热处理工艺:直升式渗碳技术、齿轮锻坯等温退火工艺、齿轮渗碳预氧化处理工艺、低压(真空)渗碳技术、催渗渗碳技术以及齿轮淬火控制冷却技术等,这样既可保障齿轮的热处理质量,又可提高其服役寿命,将产生良好的经济效益和社会效益。
(5)汽车齿轮的热处理质量检验
对于渗碳或碳氮共渗齿轮,其质量的检验是依据其技术要求来确定的,具体如下。
①渗碳层深度1.0~1.3mm,采用金相法检查,利用显微镜检查。
②碳化物级别为1~5级,马氏体、残余奥氏体级别为1~5级,检查方法同上,应参考标准级别图来判断。
③齿轮表面与心部的硬度分别为58~63HRC和30~40HRC,采用洛式硬度计检测。
(6)汽车齿轮的热处理缺陷分析与对策
齿轮的化学热处理过程中,出现产品质量达不到技术要求的指标,其原因是多方面的。应当指出,齿轮的热处理方法有渗碳淬火、碳氮共渗淬火、感应加热淬火以及整体加热淬火,在其淬火冷却过程中,各种原因均有可能造成缺陷的产生。为此应进行具体的分析与讨论,一般汽车齿轮热处理缺陷以及产生的原因见表1-83。
表1-83 渗碳和碳氮共渗齿轮常见热处理缺陷及防止措施
