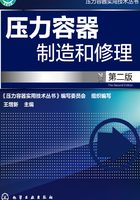
2.12 表面处理、油漆包装
2.12.1 表面处理
涉及压力容器零部件或产品的表面处理可包括两大部分,第一部分是钢材预处理,是指钢板、型材、管材在进入车间加工之前,预先进行除锈、除氧化皮,然后再涂上保护底漆的工序。钢材经预处理后进入车间,不仅大大减少了环境污染,提高了文明生产程度,而且对提高产品质量、延长产品使用寿命也显示出其优越性。国内在钢材预处理的生产线的设计、制造与应用上也已取得了可喜的成绩,特别是造船行业已初见成效。但是在压力容器制造行业中至今还是空白点。第二部分便是本章所涉及的,主要针对容器类产品竣工后的表面处理,包括除锈、酸洗钝化及抛光。
2.12.1.1 除锈
竣工后的压力容器,出厂前需进行表面涂装,它有一定的装饰性作用,但主要是防腐。涂装的第一道工序便是除锈。除锈清理的方法有手工、机械、化学除锈、火焰除锈,也可以采用喷砂、抛丸等方法除锈。为评定除锈的效果与等级,我国参照瑞典SSI的除锈标准,制定了GB 8923—2011《涂装前钢材表面锈蚀等级和除锈等级》标准。该标准规定用字母“Sa”表示喷砂或抛丸除锈,用字母“St”表示手工、动力工具除锈,用字母“F1”表示火焰除锈。根据除锈效果(清洁度)分成若干等级,如喷砂、抛丸除锈有Sa1、Sa2、Sa2、Sa3四个等级,一般为Sa2
级,钢板表面粗糙度约为30μm。对表面除锈质量要求更高的可选Sa3级。钢板表面粗糙度与采用喷射等所用磨料颗粒度、品种及喷扫速度等因素有关。如需涂油漆,过大的粗糙度会使波峰上的涂层较薄而引起早期锈蚀,过小则影响漆膜的附着力。除锈后的表面清洁度检测在GB 8923—2011中是采用照片实物做比较来判定的。粗糙度同样可用标准样块进行对照确定,但目前使用较普遍的是粗糙度仪,用指针直接在钢板表面刻划,由于指针的跳动而将非电量转化成电量,从而直接读出表面粗糙度值(Ra)。另一种是将试块放在显微镜(光干涉仪)下观察,可测得小于0.125μm的粗糙值(Rz)。国外还常用印(硬)膜法在现场对实物进行直接测读(Ra),检测过程十分简单,即采用一种专用塑料薄膜,直径约10mm,压在被测表面上,用金属笔套在薄膜上压划,使钢板表面粗糙度波纹刻印在薄膜上,再取下薄膜,在空气中凉十余秒钟,即固化,然后再用专门仪器检测该薄膜而直接读出粗糙度值。
①手工除锈 是一种简便易行的方法。它适用于一些较小的物件表面及没有条件用机械方法进行表面清理的设备外表。即用钢丝刷、砂布、砂轮片等将物件表面氧化皮去除,然后再用有机溶剂如汽油、丙酮、苯等将浮锈和油污洗净。
②机械方法除锈 适用于小型物件的局部除锈,如表面弯曲、狭窄、凹凸不平以及角缝处。采用电动或风动砂轮机、砂带机、百叶轮、风动针束工具等,可以用来清除氧化皮、铁锈、旧涂层、表面飞溅、焊瘤等。其特点是操作简便,效率高。
③喷砂除锈 对于如压力容器的外表面除锈,喷砂是采用最为广泛的一种除锈方法,它适合于大面积吹扫,可清除钢板表面的锈蚀、氧化皮及各种污物,使金属表面呈现出白色(或近白色)的均匀粗糙表面,以增加油漆漆膜的附着力。喷砂表面还适用于衬胶、表面热喷镀、表面堆焊等工艺的前期准备。对焊缝进行磁粉检测之前,采用喷砂清理效果最好。喷砂所用的磨料通常有石英砂、炉渣、淬火的钢砂或钢丝砂等。石英砂的颗粒度一般为1~4mm,钢砂为1.2~1.5mm。喷砂用压缩空气应经过脱水、除油处理,使用压力一般为0.5~0.7MPa。
④抛丸除锈 适用于清除正火处理(或热成形)中形成的氧化皮及锈蚀严重且附着力较强的厚氧化皮,但不能去除油污,也不适用于MT之前的焊缝表面清理。抛丸法通常是在密闭室内进行的,因此适用于中小型零部件,如厚壁封头与筒节等。抛丸所用钢丸直径为0.3~3mm。
⑤化学除锈(酸洗法) 常用于不锈钢和有色金属产品或零部件的表面处理。作为除锈方法,也适用于如钢管内外表面及一些形状复杂的构件的除锈清理。通常是将工件浸泡在酸液中,以清洗表面氧化物及油垢等。酸洗法主要有以下几种。
a.用50%的硫酸和50%的水(体积分数)混合成硫酸溶液,将零部件浸入,使表面铁锈洗除,再用清水漂洗。
b.用浓度为10%~20%的硫酸或浓度为10%~15%的盐酸进行酸洗;也可用含有5%~10%硫酸和10%~15%盐酸的混合液进行酸洗。还有用磷酸进行清洗。有时为减轻酸对金属的溶解,可加入少量(1%左右)缓蚀剂如乌托品。清洗方法可采用涂刷、淋洒或浸泡等。酸洗温度应于适当控制,采用硫酸时,一般温度为50~70℃,采用盐酸时,温度为30~40℃。经酸洗的金属表面必须用水彻底洗刷,然后用20%的石灰乳或5%的碳酸钠溶液,或采用其他稀碱液进行中和。经中和处理后再用温水漂洗2~3次,然后用干净抹布擦净,并经加速干燥后进行涂装工作。
c.用酸洗、磷化处理代替喷砂除锈,可大大改善劳动条件,降低成本,提高工效。酸洗后再进行磷化处理,使金属表面在空气中保持较长一段时间而不被氧化,且有利于提高油漆附着力。
磷化液配方见表2-24。
表2-24 磷化液配方

配制时,先在磷化槽内装一定量的水,按上述配方加入其他成分,搅匀后升温至40℃,然后加入明胶,再升温至80~90℃,最后放入工件,磷化时间一般为40~60min。
⑥火焰除锈 常用来清除一些局部的且附着力较强的氧化皮,采用氧-乙炔火焰对氧化皮进行加热、吹扫。如经热成形的封头、筒节,局部形成较致密的氧化皮,用喷砂也难以清除时,可用火焰清除。一般火焰除锈不适用于Cr-Mo钢及高强物件。
2.12.1.2 酸洗和钝化
①铝和铝合金容器的酸洗和钝化处理 对这类容器,如要求酸洗表面光亮,则必须先用浓度为16~66g/L的烧碱(纯碱或磷酸三钠)溶液进行碱洗。由于这一步是碱洗,兼有去油的作用,故无需预先做脱脂处理。但如表面油脂比较严重,也可先用溶剂进行去油,然后进行碱洗。碱洗之后可做光亮酸洗,目的是去除热处理遗留下来的锈斑,因为锈斑是不能用碱液洗掉的。酸洗时可在下述溶液中浸泡1min(体积比,下同):氢氟酸:硝酸:水=1:1:98。然后再在下述光亮酸洗溶液中漂洗几秒钟:硝酸:水=1:1,或硫酸2L、硝酸1L、水1.5L、盐酸4mL,操作条件为室温。
②杜拉铝容器的酸洗 酸洗液配方如下:NaF10g/L,硫酸188mg/L。然后再在上述硫酸-硝酸光亮酸洗液中漂净。
③铜和铜合金容器的酸洗 有以下几种酸洗液的配方。
a.硫酸法酸洗液 硫酸:水=1:9。操作条件:110~157℃。对于纯铜和铜含量大于85%的铜合金,由于其表面氧化物中含有CuO2甚多,采用硫酸法不易清除,必须采用下述含有氧化剂的酸洗液。
b.重铬酸法酸洗液 硫酸122mg/L;重铬酸钠16~33g/L。操作条件:室温~157℃。
c.硫酸铁法酸洗液 硫酸8.2g/L;无水硫酸铁8.2g/L。操作条件:低铜合金102~122℃;高铜合金122~157℃。
d.过硫酸铵法酸洗液 过硫酸铵180~240g/L,操作条件:室温。
pH值:新配溶液3.5~4。当pH值降至1.5~2时,溶液即需报废。新配溶液可用3~5天。
酸洗后,在做光亮处理之前,应先以下述溶液做除氧化皮处理,使表面预先光滑化,以延长光亮酸洗液的寿命。
硫酸:硝酸:水=2:1:5。
浸入工件后需进行搅拌。如反应激烈,可增加硫酸的含量。光亮酸洗液通用配方与①相同。
④不锈钢容器的酸洗 在不锈钢容器零部件上如存在锻造氧化皮或退火氧化皮,则很难用一般的酸除去,而必须采用两步酸洗法,第一步松动氧化皮处理,第二步消除氧化皮或光亮处理。如果氧化皮很轻微,则松动氧化皮处理这一步可省去。另外,在酸洗液中必须适当加入一些缓蚀剂。
a.氧化皮松动处理 其溶液配方有以下几种:
ⅰ.硫酸98.6g/L;操作温度162℃。
ⅱ.硫酸:盐酸:水=1:1:8。操作温度112~122℃。
ⅲ.高锰酸钾25~100g/L;纯碱25~100g/L。操作温度150~195℃。
b.消除氧化皮处理 其溶液配方有:
ⅰ.硝酸:氢氟酸:水=1:1.5:1.5。操作温度107~132℃。
ⅱ.硝酸1L;氢氟酸0.25L;盐酸0.125L;水9L。操作温度112~122℃。
ⅲ.硫酸31~63g/L;硝酸95~125mg/L;氢氟酸15~20L。
ⅳ.盐酸5L;硝酸1L;水14L;操作温度107~142℃。
c.光亮酸洗 在做光亮酸洗之前,必须先将不锈钢件在5%热硫酸中浸泡,以消除氧化膜。光亮酸洗液配方如下:硝酸:粗盐酸:磷酸:醋酸=4:1:1:5。操作温度142℃。
d.钝化处理 不锈钢件在酸洗处理之后,都必须接着进行钝化处理。钝化膜质量可用微带酸性的硫酸铜溶液进行试验,在钝化表面上不得有铜淀析出来。钝化液配方如下:
ⅰ.硝酸:水=1:4,操作温度102℃,操作时间20min。
ⅱ.硝酸:水1:1,操作温度为室温,操作时间1~2h。
对于高碳铬钢,在溶液中尚必须加入16~32g/L的重铬酸钠。
以上不同材质容器的酸洗、钝休处理需在专门的、通风良好的车间内进行,车间地面和墙壁应能耐酸、碱液的腐蚀,车间内的酸洗废液需经中和池处理后才能排放。车间内应配备必要的设备,例如碱洗槽、酸洗槽、钝化槽、清水槽等。对于最终不能进入清洗槽的大型容器,应采用专用的喷淋装置进行内外表面的整体酸洗、钝休处理。处理时必须采用强力通风和遥控作业。
2.12.1.3 抛光处理
与抛光相关联的工艺有打磨和精抛光。三者之间的区别是去除的金属量(包括一部分非金属夹杂物)不同。抛光处于打磨和精抛光之间。精抛光所去除的金属量最少。这里所说的抛光处理,实际上包括抛光和精抛光两种工艺。
抛光处理一般用棉织物制成的抛光轮,其中最硬的抛光轮是用帆布胶合在一起而成的,最软的抛光轮是用细棉布缝合在一起而成的。在抛光轮上采用特殊的胶合剂将磨料黏结在一起。磨料粒度大小与胶含量的关系见表2-25。
表2-25 磨料粒度大小与胶含量的关系

抛光常用磨料为熔融的氧化铝。一般需将这种粒料进行热处理,使它具有良好的毛细作用。此外,对于一些粒料需进行侵蚀或破膜处理,以改善它们的黏结性能。熔融的氧化铝既尖而硬,磨削快,耐磨损。其他磨料有碳化硅,它被用于特殊场合。由于这种磨料不易粘牢,故应用不广。在采用电炉熔炼磨料之前,曾采用过土耳其金刚砂(一种天然氧化铁的化合物)作为标准磨料,这种磨料不碎裂,磨损时慢慢地变成圆角,因此切削速度会逐渐降低,适用于精抛光。抛光时应采用润滑剂,以防止表面产生沟槽和减少摩擦热。
抛光轮的表面速度一般取1800~2430m/min。在抛光作业之后可根据需要再做精抛光,后者又分为4级,即毛面抛光、弱切削力抛光、次镜面抛光和镜面抛光。两种精抛光的表面速度推荐见表2-26。
表2-26 精抛光表面速度推荐表

不锈钢板表面的精整处理,从不抛光到精抛光,分为以下8级。
No.1不抛光 指热轧到指定厚度后,做退火和去氧化皮处理的无光泽的表面。
No.2D不抛光 指冷轧到指定厚度后,做退火和去氧化皮处理的无光泽的表面。也可能在无光轧辊上再做一次最终的轻轧。
No.2B不抛光 同2D处理一样。所不同的是,对于退火和去氧化皮处理的表面还要再接受一次在抛光的轧辊上进行最终的轻度冷轧,从而得到光亮的表面。它比No.1和No.2D的板更易于接受抛光。
No.3半抛光 最终采用粒度为50或80目的磨料进行抛光得到的表面。
No.4抛光 用100~150目磨料做光亮抛光得到的表面。
No.6精抛光 表面反射率低于No.4处理的无光精抛光表面。它是采用无油脂的200目磨料抛光,最终用白色铬粉进行精抛得到的。
No.7精抛光 指具有高度反射率的精抛光表面。它首先精抛到No.6的水平,然后再以白色铬粉做轻度抛光。
No.8精抛光 指反射率最高的精抛光表面。它采用粒度逐次变细的磨料逐次抛光,然后用极细的白色铬粉做深度精抛。
不锈钢容器的抛光,除采用抛光轮外,尚采用砂带式抛光机进行抛光。为减少抛光工时,一般先将板材在专门的平板抛光机上进行预抛光,待成形、组焊后再对焊缝做局部最终抛光。这样可提高抛光的机械化程度,并大大降低制造成本。
2.12.2 油漆
压力容器产品竣工后需对其进行总体涂装。除不锈钢及有色金属容器外,绝大多数碳素钢、低合金钢制压力容器,出厂前均需按照JB/T 4711规定进行油漆。
压力容器涂装的一般规定如下。
①涂装前的表面处理可采用除锈的方法,清除容器外表所有的铁锈、氧化皮、油污、尘土等物。表面处理的质量好坏直接影响油漆涂层的附着力,所以必须认真对待。为保证油漆施工质量,经喷砂除锈的容器,应于当日将底漆喷完。当对涂层质量有较高要求时,喷砂除锈后4h内应将底漆喷完。
②根据产品图样要求选用底漆、面漆,每层油漆必须使用同一厂家生产的油漆。常用油漆品种推荐按表2-27选用。对油漆有特殊要求时,可在产品图样上注明。
表2-27 压力容器常用油漆品种

③用于压力容器涂装用油漆应具有出厂合格证明书及使用说明书,国外的油漆公司通常的做法是在油漆说明书中还详细列出油漆施工要领,内容包括干料重量比、表面粗糙度要求、喷涂压力、喷嘴号数、胶管直径、每层涂层厚度及漆膜固化条件等工艺参数,并赠送湿膜测厚样板。有的油漆公司还负责喷砂、除锈及油漆施工全套业务,以此来保证该公司所供油漆质量可靠的信誉度。
④油漆施工场地应相对固定。对于经常承揽海外工程项目的厂家,为适应涂装质量的更高要求,应建有专用全封闭涂装车间,并配有与涂装施工要求相适应的照明、通风、防爆、防尘、干燥等设施。涂装用压缩空气应经脱水、除油处理。
⑤涂装可采用手工刷涂、辊涂、压缩空气喷涂和高压无气喷涂等方法。尽量采用高压无气喷涂法,它适应于大面积喷涂,不但效率高,而且漆膜质量均匀致密,附着力强,油漆利用率高,对空气污染小。
⑥一般加工件表面可涂防锈油脂,精加工件表面(如h6级精度的螺纹及密封件等)应涂无酸性工业凡士林。
⑦分段、分片出厂的容器、球壳板、组装焊缝坡口及其周边100mm范围内可不涂油漆,但需涂防锈用可焊性防锈涂料。
如欲对油漆做进一步了解,可查阅SH/T 3022—1999《石油化工设备和管道涂料防腐蚀设计规范》。
2.12.3 包装
压力容器产品的包装必须在油漆完工后,在发运之前进行。包装应按照JB/T 4711《压力容器涂敷与运输包装》的规定。精心而有效地做好包装工作,使产品安全、完整、可靠地运达目的地。
①容器类产品包装形式可分为裸装、框架、包扎、暗箱及空格箱。
a.裸装适用于容器产品的本体,如整台的塔器、反应器、换热器、贮罐、搅拌釜等,及长大型分段发送的塔器分段。裸装发运必须附设发运支架、托架,并有防翻滚、窜动设施。
裸装发运的容器上所有管口均需用盖板封闭。
b.框架适用于小型容器本体,大型分片发运的壳体、锥体、瓦片、球壳板等。
c.包扎适用于不易失散和损伤的零部件,如吊柱、弯管等,及件数较少、不用装箱的零件如保温支持圈、平台、梯子、格栅及管件等。捆装应做牢固包扎,以防止运输半途松散而丢失。选用何种包装形式还应根据运输方式、运输条件、路程长短及产品零部件的质量要求等因素进行选择,也可按合同约定进行包装。
d.箱装又可分暗箱(即密封箱)与空格箱两种,前者适用于精密、易损零件和怕潮、防腐、容易失散的标准件、外购配套件。后者适用于塔内件、人孔部件、大型配套件等的包装。
②所有包装形式一旦确定,在包装过程中应按照包装清单进行包扎、装箱和装架。包装清单应逐一列出所装零部件数量。所有包装全部完成后还应填写发运清单,以明确每一种包装方式的件数及总件数,以便于各环节的交接、清点、验收。
③每一种包装形式应逐件标明发运标志。该发运标志可用镂空模板喷刷在容器本体及包装箱上,也可直接手写。而捆扎、架装件可采用挂牌方式。